Table of Contents
Introduction
The following material was compiled by Dick Bing in April 2008 and updated in July 2010.
Please feel free to get in touch if you have details of the history of Pye in Waihi which you would like to share. frbing@xtra.co.nz
Contributors
Grateful thanks and credit for content is made to;
Graham Street
Ted Grant
Ben Foster
Peter Boland
Dick Spurr
Eric Lens
Henk Bouius
Lyall Bowen
Glen Mayclair
Peter Brown
Pye History
1932 - 1946: Keith M. Wrigley
Long before the Waihi Gold Mine closed in 1952, Keith Wrigley had, in 1932, established a radio sales and repair business with a capital of 52 N.Z. pounds (buying in complete radios) in lower Seddon Street, in what came to be called ‘The Dean Building’. He was the elder son of James Wrigley, a reporter on the Waihi Telegraph.
A plaque was placed on the building to mark the event, but this has been removed in later years.
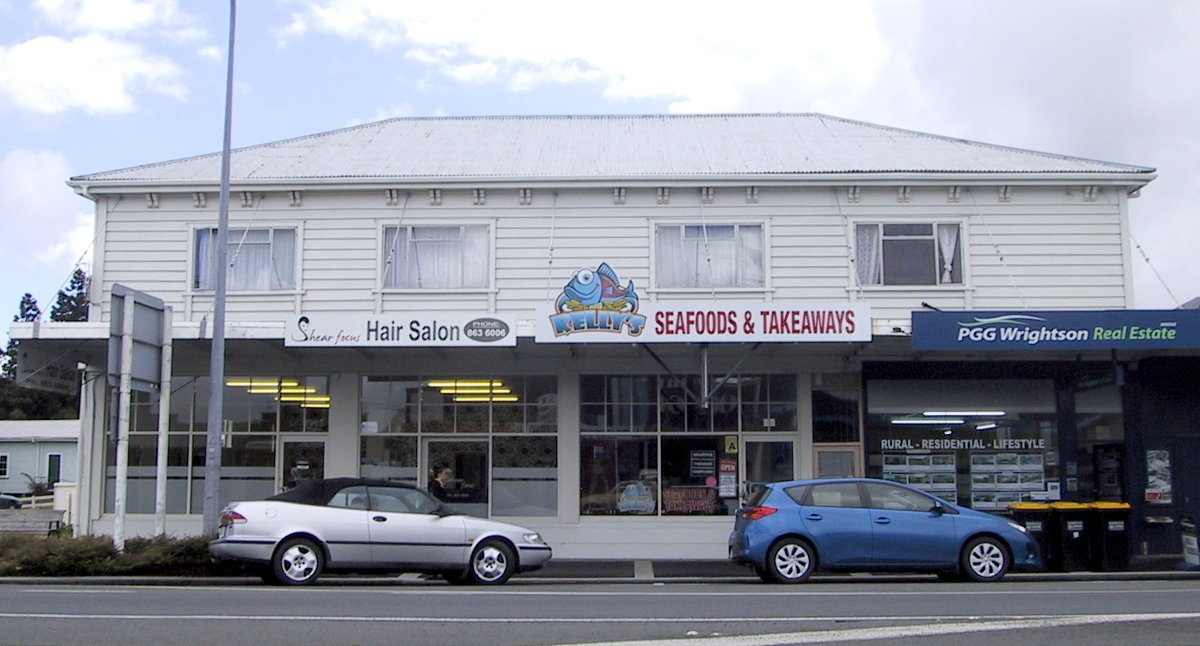
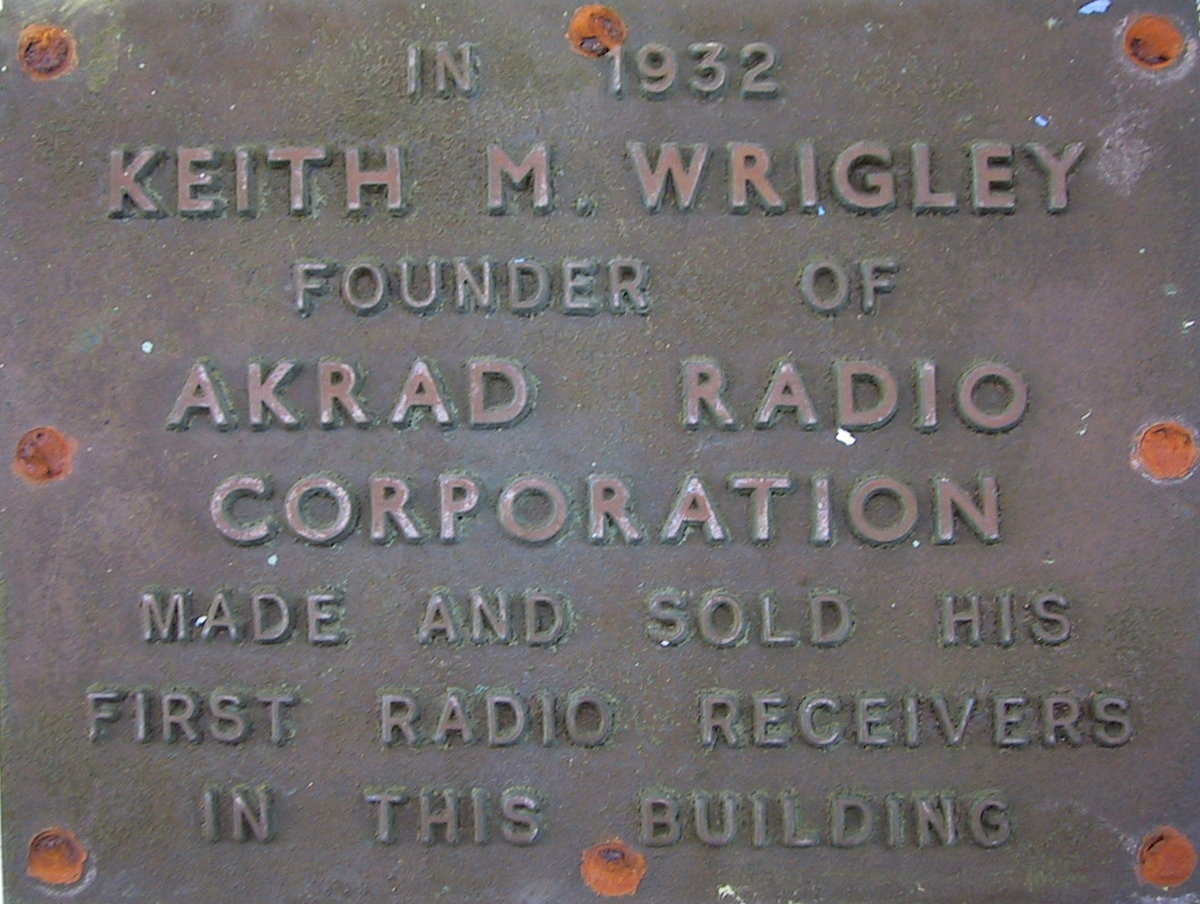
As the business grew, he moved to premises also in Seddon Street where he decided to manufacture his own sets, under the trade names of “Futura”, “Luxur” and “Everest”. This site later became the Waihi Dry Cleaning Co. Each set carried a plate reading “Made by Keith Wrigley”.
At this stage he decided to manufacture components as well, so he moved to a vacant dairy in Rosemont Road, next door to E. A. Clark pharmacy. In January 1938 he moved again to a two storey building in Upper Seddon Street close to the Anglican Church. This building later became Attwood Aluminium. By 1937 Wrigley formed “Akrad Radio Corporation” and was now employing 50 staff producing a wide range of radios and appliances, including electric fences. When war broke out in 1939 (second world war), he was still producing radios but by 1942 the government decreed “this had to cease”– “ and he make radio equipment for the services”. This required larger premises so, in 1943 he moved into the King’s Hall in Haszard Street.
Here they began work manufacturing signalling lamps, morse sets, buzzers, air raid sirens, radio components (coils and transformers) and battery adaptors.
Unofficially a small run (3 or 4), 12 volt battery operated domestic radios were made and delivered to the U.S. army in Auckland.
By 1945 the work force had grown to 90. As the acquisition of components became uncertain, Mr Wrigley introduced a new line, children’s tricycles. “The Akrad Flyer” reached its peak in 1947 when the 50,000th trike rolled off the line , and a few years later a total of 180,000 had been made.
The large Akrad Flyer below was made as a one-off to be used on special occasions. It is now held by the Waihi Museum and is ridden in the Christmas parade from the old factory (now Waihi Gold H.Q.) up the main street and back again. The smaller model in the picture is a standard production run.
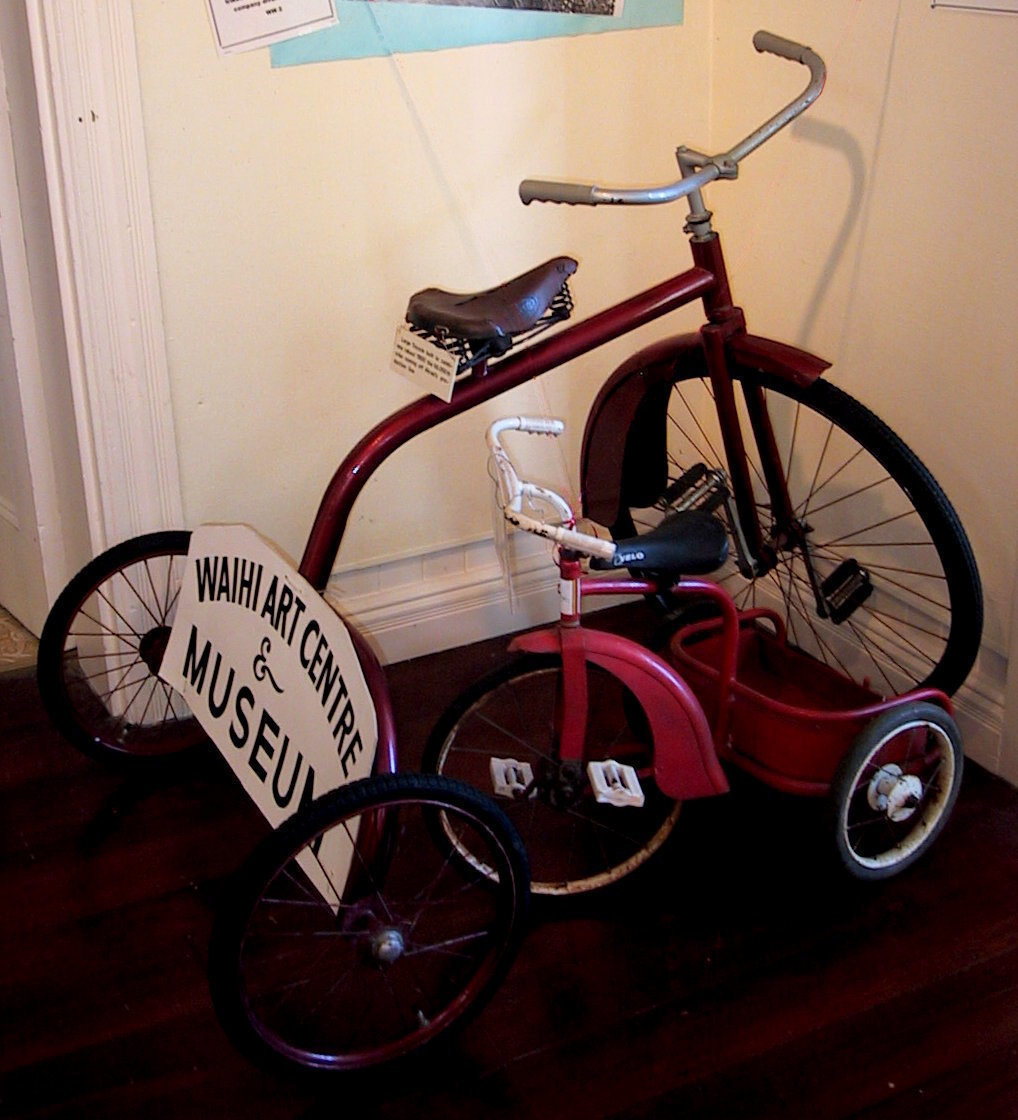
When the line was finally closed in 1969, about 200,000 had been made and Tonka Toys then bought that part of the business, running it for 5 years. In 1974 the “Akrad Flyer’ returned to Waihi when Brown and Brown (Waihi) took over production for a further 10 years. Both firms had made about 10,000 trikes a year, so from 1945 to 1984 approximately 300,000 “Akrad Flyers” had been turned out.
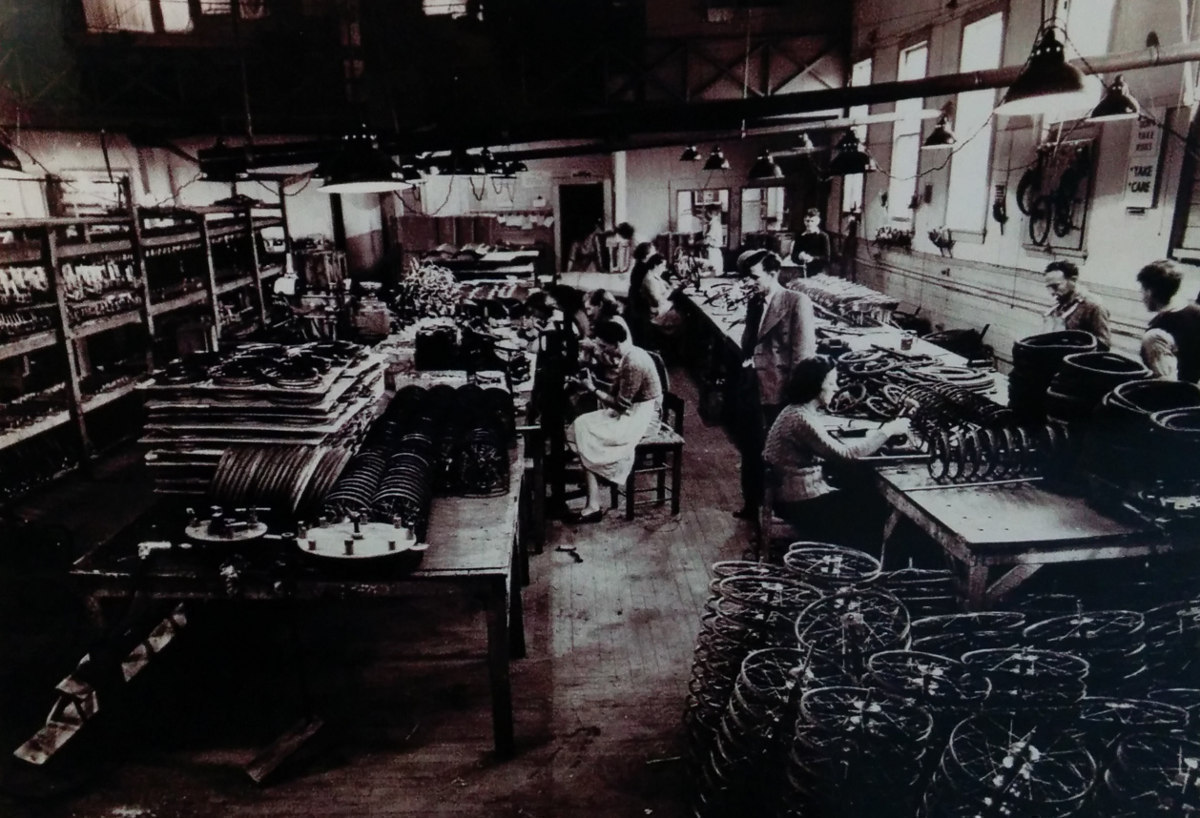
Unfortunately on New Year’s day 1946 Mr Wrigley died suddenly, from osteomyelitis, at the age of 33, ending a 14 year development of Akrad.
1946 - 1947: G. A. Wooller
At this stage Akrad was in considerable financial difficulties through having to meet death duties and income tax.
George Wooller had been production manager at Radio Ltd, Auckland, and had been in this position for the duration of the war. This association led to George Wooller forming G. A. Wooller and Co., acting as a distributing company for Akrad manufactured products and this in turn had a profound effect on the post war growth of Akrad.
Under Keith Wrigley’s will, a company was formed under the direction of the Public Trustee. As they had no knowledge of radio manufacturing, they called on George Wooller and Mr Moore Haszard (along with W. Leitch and W. Meiklejohn.) to manage Akrad through this difficult period.
1947 - 1957 (approx): T. J. F. Spencer
In 1947 Tom Spencer was appointed manager and ‘Akrad Radio Corporation Ltd.’ was formed with a capital of 30,000 pounds. This put Akrad on a firm financial footing. In 1948 Mr Spencer was made managing director. Prototypes of motor scooters and a trial run of 50 rotary lawn mowers (the first in New Zealand) were introduced. A trial run of kit-set refrigerators imported from Australia and assembled here were also tried, but these innovations were shelved as the directors felt they were not the company’s prime objective.
A chain of Akrad dealers was set up to sell the radio products - small portable radios to large cabinet models, under the brand names of “Pacific”, “Regent” and “Five Star”.
In 1947, Green and Cooper who were the New Zealand agents for Pye (U.K.) VHF radio-telephones, supplying Auckland Traffic Department, followed by Auckland Fire Brigade. Then Wellington Taxis were supplied with 30 VHF units made in the Waihi factory. By 1962 Pye was the leading manufacturer of radio-telephones in New Zealand, the sets being produced both in Waihi and Wellington.
By 1949 with the world wide growth of T/V the directors felt it would be best to be associated with an overseas company, so an approach was made to Pye Ltd, Cambridge, England.
Mr C.O. Stanley (chairman of Pye U.K.) came to New Zealand for negotiations.
Pye (N.Z.) Ltd was set up in 1951 and Mr G. A. Wooller was appointed Managing Director. By 1952 Pye U.K. had a substantial shareholding in Akrad which led to an increased expansion of the company.
Mr Ted Grant, who joined the firm in 1940, became the chief engineer in charge of the “Lab” at Barry Road where 20 engineers and draftsmen (and ladies) were now employed. As the product range increased and the staff had increased to 31, room for more Research and Development space was required . The ‘Lab” was doubled in size in the 1960s.
Television was getting established and when Queen Elizabeth II came to N.Z. in 1953/4 Pye brought in a T/V rack mounted transmitter and cameras from Pye UK to cover the Queen’s dinner in the Wellington town hall. The system was operated by Pye UK engineers except for the audio side, which Ted Grant operated. Other smaller demonstrations were also staged at that time. The equipment remained the only unit of its kind in the country for several years.
The first outside T/V broadcast of a rugby match, staged by Pye engineers at Waihi Rugby Park in 1954, was the game between Harlequins and Barbarians; the pictures and commentary (using the same system as above) being transmitted to some 100 Pye T/V sets round the ground, Waihi Hospital and several private homes. Ted Grant, Ken Tribble and Trevor Corder operated the “control room ”.
At the 1954 Auckland Easter Show, a T/V studio was built, with telecasts transmitted to Pye sets in Green Lane Hospital and several private homes. Pye Waihi provided engineers to operate and supervise the equipment. Using the rack mounted equipment and cameras, several demonstrations were organised for dealers, plus a few hospital operations were covered on CCTV, Ted Grant being the camera man.
In 1955 a further reconstruction of the Pye group in New Zealand took place when G.A.Wooller and Co. Ltd and Green and Cooper Ltd were both absorbed into the group and the company changed its name to Pye Ltd; Akrad remaining the group’s principle manufacturing unit.
1958 - 1960: G. Rowe
Production of Pye designed black and white television sets began in July 1959 at the rate of 10 a day. 300 of the 21inch model 201T were made for closed circuit T/V in Auckland as transmission of T/V had not started in New Zealand.
By 1962, T/V transmission in parts of New Zealand had begun. 10,000 various models were produced annually and by 1966 over 150,000 had come off the line, after two “soak tests” of more than eight hours. In 1965 Mr Graham Street was in charge of T/V production, taking over from Mr Barry Babbage.
Demand for Pye products grew even more, so production had to keep pace. The Waihi work force in 1982 stood at 405 at No. 1 and 2 plants (more women being employed than men) with 75 employed in Paeroa and 31 at the Barry Road Lab. In all, nation wide, Pye employed almost 1500, including a depot in Christchurch.
Quality control of all Pye’s products was becoming more important and as a result a new section was introduced to cover this area with Mr Laurie Horton to manage it; he also became factory manager in 1981 to 1982.
1960 - 1981: R. Skinner
From 1960, Mr Ron Skinner was factory manager, Mr Henry Jensen production manager, Mr Ross Vickery in charge of the machine shop (Mr Lyall Bowen took over in 1979) and Mr Henk Bouius was running the tool room. Mr Arthur Lindsey (Artie) was head of the King’s Hall winding and coil section. Also in King’s Hall, Mr Murray Radford was looking after the trike line, the relay line and the speaker department.
In 1962 Pye Waihi manufactured 26inch black and white T/Vs and between 1962 and 1977, 250,000 sets had been made. Colour T/V came on the scene in 1972. Production of the first Pye colour set designed under Mr Ken Trible’s guidance, using printed circuit boards (PCBs) commenced with a small run of 100 units. Ken soon developed a system to mount the PCBs vertically, thus reducing the depth of a T/V cabinet by 76mms. Pye was first to use the 26inch Toshiba In Line Gun colour tube, before Japan.
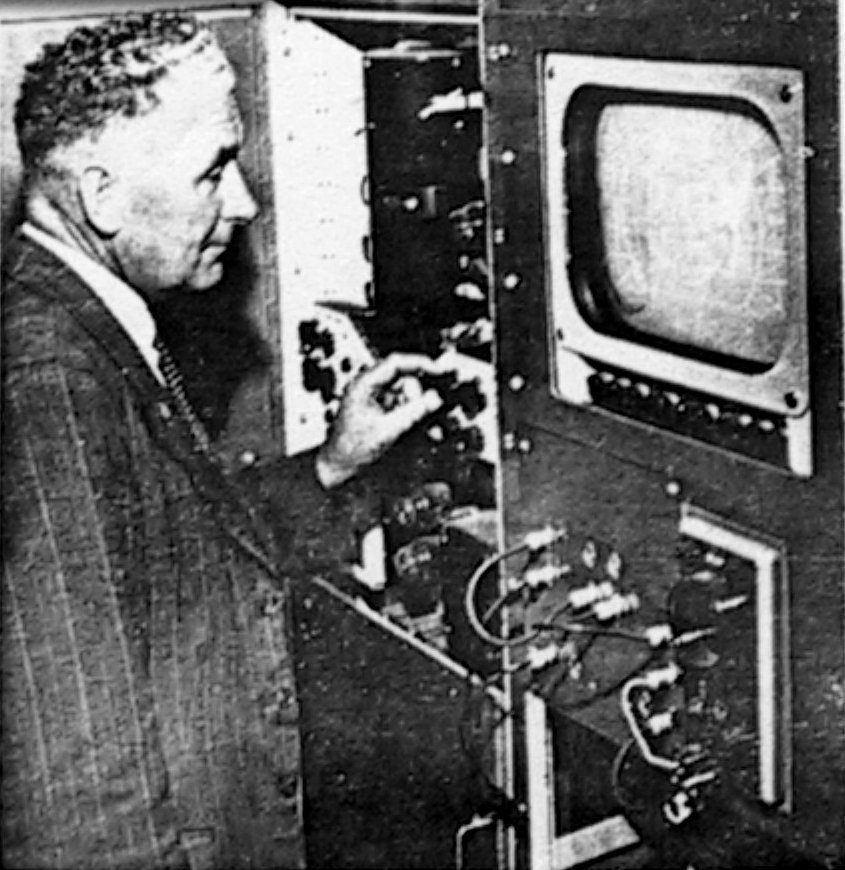
By 1962 the company had grown to include:- Pye Electronics Ltd, G. A. Wooller & Co Ltd., Green & Cooper Ltd., Radio Corporation of N.Z. Ltd., International Records Ltd. as well as the Akrad Radio Corporation Ltd. Two factories were opened in Paeroa: Pye Records and the “Winding Room” making transformers , coils and runs of small portable radios.
In 1960/1 Pye U.K. invested 1 million pounds in a massive up-grade of the Waihi factory. A new machine shop, plating , paint shops and tool room were built alongside the King’s Hall (No 1 plant) ; the main assembly, office and cafeteria seating 200, (No 2 plant), went up in Moresby Avenue, opening in December 1962 and the Research and Development Laboratory in Barry Road was constructed.
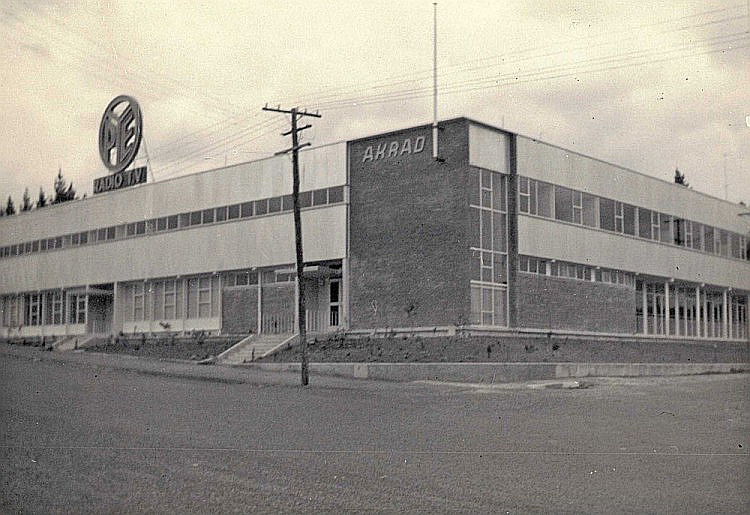
Now the work force had grown to 200, with staff commuting from Katikati, Waihi Beach, Paeroa and Whangamata. Pye N.Z. was spreading its wings over the North Island. In Auckland the head office was set up, with Pye Consumer products, Pye Telecommunications and Industrial Electronics. Near Hamilton at Te Rapa, Audio Products including Akai reel-to-reel and cassette recorders plus their “Dolby” systems (under licence) were manufactured. Development of these products took place in Waihi. At Frankton, Cabinet Productions was set up. In the early 1970s, another first was being used in the cabinet factory, a precision wood cutting machine, made in the Pye tool room. This could cut a 90 degree slot in the material leaving a fraction of a millimetre, without breaking through. It cut three V slots and a 45 degree cut on each end, so with glue added to these slots and ends the sheet was then bent in another machine which also applied the glue, to form the top, bottom and sides of the cabinet; it then only needed a front and back. The Frankton factory also made coffins. Moving south to Wellington, Wire & Cables was born, and R.C.A. records came under Pye control. Thus many of the products required to produce both radio, T/V and consumer goods were “in house”
Dick (Richard) Bing began work with Pye NZ in Waihi in 1964 having worked for Pye in Britain in a range of roles. His time in Waihi was to see him employed in the factory on fault repair, in the relay department designing radio and HiFi units, in the Lab in Barry Road, managing the instrument section and then quality control. All up he was with Pye/Phillips (who took over Pye) for 38 years.
A production line to produce relays was set up in the ‘60s; Pye U.K. had been making relays for some time under the name “Magnetic Devices “ so most mechanical parts were imported but the coils were wound here. The main production was the ripple control relay for the Power Board, 800 were produced a week. Small runs (50 or 100) would be made to special order for other types of relay.
In 1966, Waihi had a festival week called “Mardi Gras”. Outside the Memorial Hall an ‘Igloo’ was set up (thanks to Mr Erny Hands) and Jim Gurney (a Pye employee) lived in it for the week. Jim operated a sound system, installed by Pye engineers, to cover part of Seddon Street and Rosemont Road.
This led to the concept of a sound system to cover the centre of town; the first in the Country. Pye donated the materials, which included two kilometres of cable and thirty speakers with transformers, cabinets and grills. Pye engineers, with help from The Chamber of Commerce, did the installation.
In 1966, Mr Dick Spurr was in charge of the silk screen room and in 1971 the first printed circuit boards (PCBs) were made. This eliminated the tangle of connecting wires. The first material was copper-clad fibre glass. At first these could not be punched without board damage, so they had to be hand drilled. Later a method was found to punch all the component holes in one operation.
To produce the boards, first a map of the tracks with etch resist was put on the copper side using silk screening, then the unwanted copper was etched away. This was labour intensive and time consuming . The boards had to be put into stainless steel racks, then into a hot agitated solution of ammonium persulphate and took about 5 minutes per batch to etch. They were then washed, the resist stripped off , washed again, then dried ready for punching. About this period transistors had been developed and incorporated into design and production of radio sets using PCBs. Pye was the first manufacturer to market them in N.Z. under the brands of “Ultimate”, “Astor”, Ultimate-Ekco” as well as “Pye”.
In 1971, a spray etch machine using Oxytron 21 {replacing the ammonium persulphate } was purchased ( the first in N.Z.). The boards then came out in a continuous stream. Only two operators were required for this process as board handling was reduced to a minimum. Silk screened boards were fed in at one end of the machine and the finished boards came out the other, dry and ready to be punched with holes for the components.
The use of the flow soldering machine meant that the printed circuit boards were held in a cradle after all the components were put in place and all were soldered in one go when the board was moved across the solder surface. This saved a lot of time as each component had to be soldered by hand prior to the machine being installed.
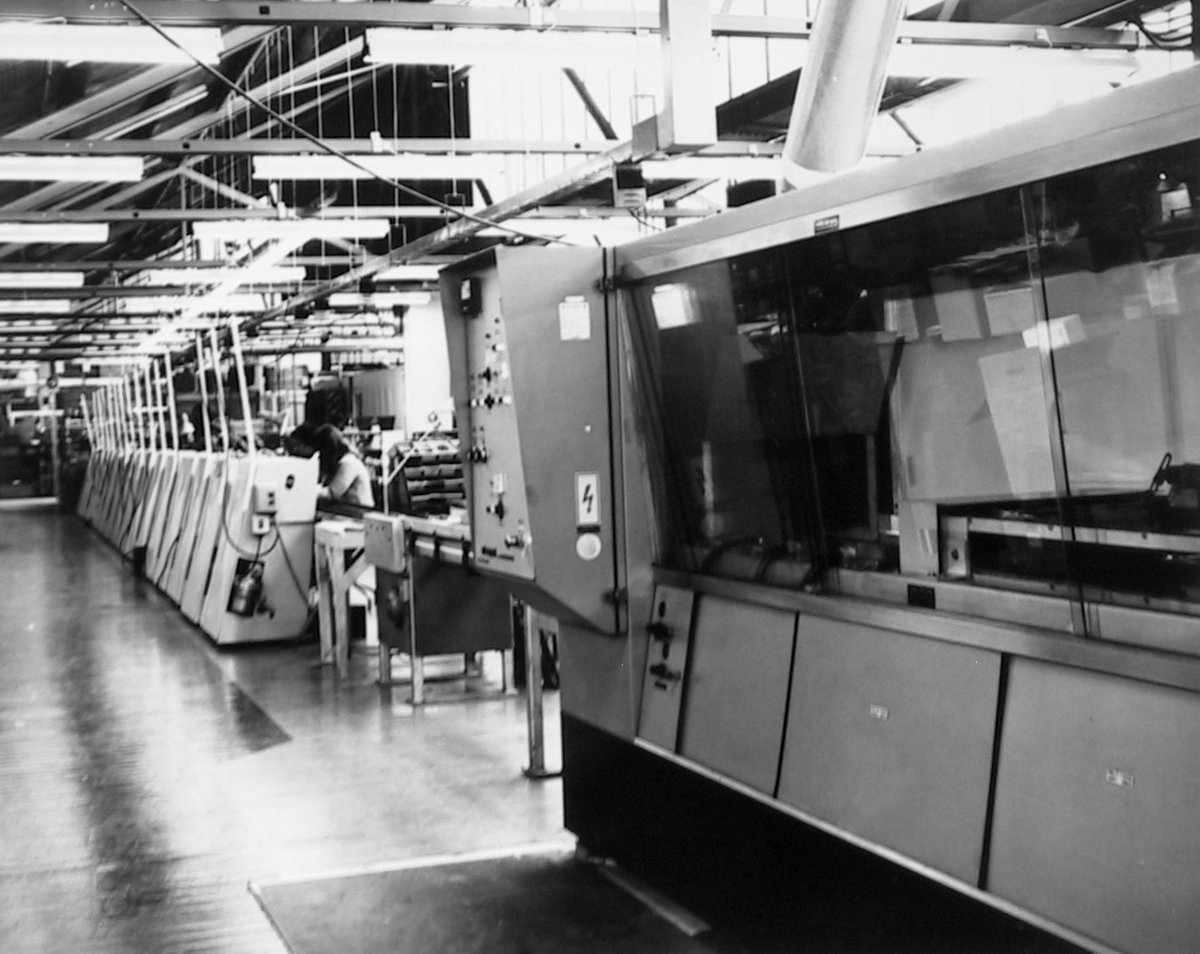
1972 saw the board base material change to copper-clad bakalite, though fibre glass was still used for special work. The tool room was the section of the plant where punch and die sets to go in the presses were made, as well as specialised tools for production. About this time Mr Ben Foster was in charge of the technical side of radio production.
Colour T/V production soon grew - Pye producing three more models, CT101, CT102 and CT103. As well as supplying the home market, sets were being exported to Hong Kong. The first batch, sent in 1977, being able to compete against European and Japanese competitors.
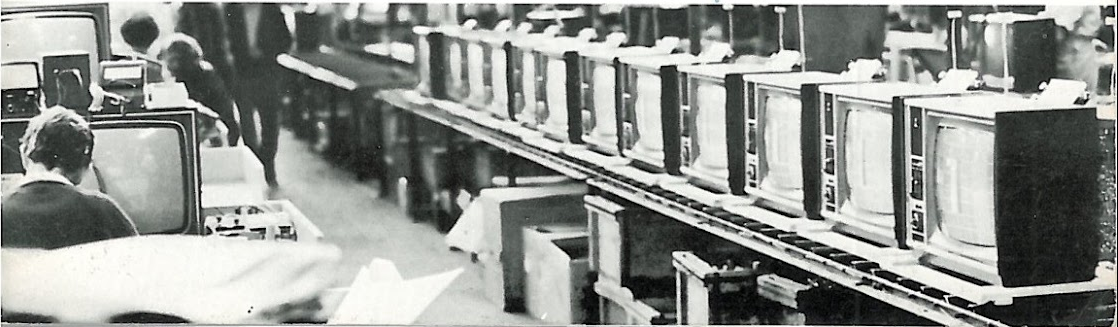
In 1977, Pye came up with another “first”, a three year guarantee on parts and labour on all their sets. Later, in 1978 Pye was exporting the latest colour T/V CT104 [ a single vertical printed circuit board set ] to :- Singapore, Malaysia, Sri Lanka, Brunei, Fiji and China, as well as Hong Kong. Fifty percent of the colour T/V production was being exported. In 1979 Mr Ken Tribble and Mr Grahan Street went over to China to negotiate with production staff at the No 1 T/V factory in Shanghai. The aim was for them to produce 1,000,000 CT104 T/Vs per year under licence, with the royalties going to Pye N.Z. But at this time Philips had taken over Pye U.K. and they did not want competition in China, so the arrangement was squashed. This would have been another first for Pye.
1981 - 1982: L. Horton
In late 1967, the Dutch organisation Philips had taken control of the parent company,( Pye U.K.) and by 1981 Pye Waihi had come under their influence making audio equipment using their name.
1982 - 1983: J. Foster
Philips re-organised the No.2 production floor in 1981/2 holiday period but later took T/V production to their plant in Naenae near Wellington; this was to make space and to concentrate on audio production in Waihi.
1983 - 1986: R. Evans
Philips had said several times that the Pye Waihi factory would not close. However when the Government removed the import duty on Asian goods, Pye and all other major electronic factories in New Zealand could not compete on price and had to close.
Pye had been a world wide organisation, having established numerous factories in the U.K., Eire, Canada, Australia and New Zealand. Thus in September 1986 a 55 year era of electronics (started in Waihi by 18 year old Keith Wrigley, under the name of “Akrad”) came to a sad end.
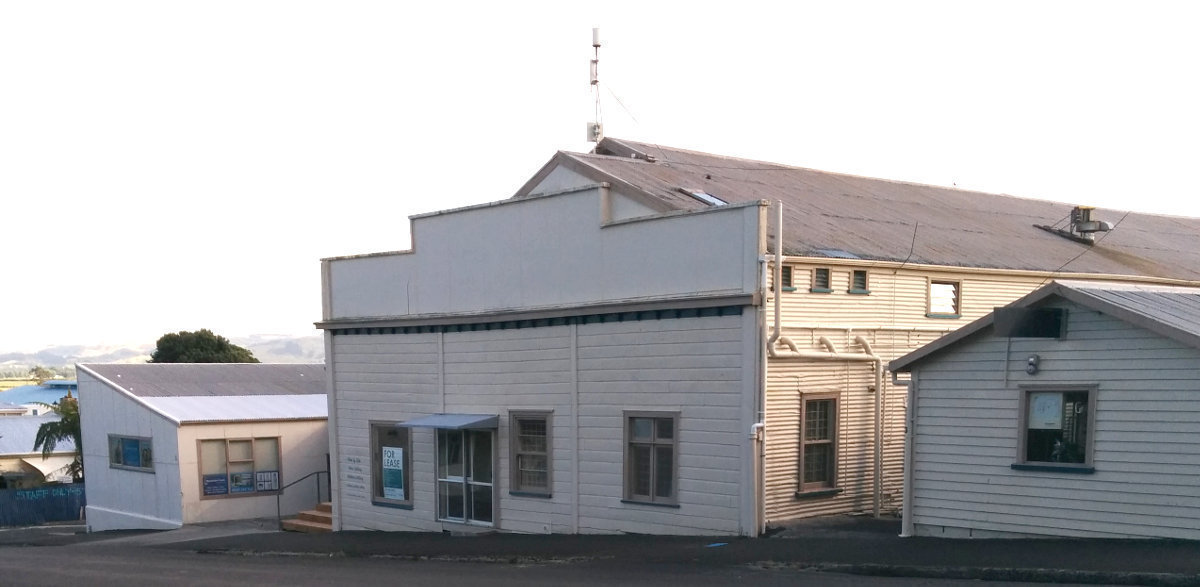
Footnote :- On 26th September 1986, Mr Graham Street placed a time capsule in No 2 plant.
Tables
1947 | Rotary lawn mowers, (small run) |
1954 | Outside T/V broadcast of a rugby match at Waihi Rugby Park |
1958 | Single-cabinet stereograms |
1959 | 21 ins black and white television |
1970 | Cabinets made from a single sheet of material |
1971 | Printed circuit boards |
1971 | Radios using transistors and integrated circuits |
1972 | Colour television production started |
1973 | Toshiba in line colour tube |
1977 | Colour television exports to Hong Kong |
1977 | 3 year guarantee on parts and labour |
1932-46 | Keith M. Wrigley |
1946-47 | G. A. Wooller |
1947-57(approx) | T. J. F. Spencer |
1958-60 | G. Rowe |
1960-81 | R. Skinner |
1981-82 | L. Horton |
1982-83 | J. Foster |
1983-86 | R. Evans |
1932 | Business founded by Keith M. Wrigley |
1933 | Commencement of manufacture of “Akrad” brand radios - “Futura”, “Luxor” and “Everest” |
1942 | King’s Hall purchased for 600 pounds. Defence contracts secured. Production of morse keys and buzzers. Signal lamps and sirens for local defence. Radio components for the services |
1945 | G. A. Wooller & Co. founded - distributors for Akrad. Staff numbers up to 50 |
1946 | January 1st, Keith M. Wrigley died |
1947 | T. J. F. Spencer appointed manager. Akrad Radio Corporation Ltd formed. Limited capital of 30,000 pounds |
1949 | Began preparations for black & white TV. Approach Pye of Cambridge |
1951 | Pye N.Z. set up. G. A. Wooller appointed Managing Director |
1954 | First N.Z. outside TV transmission from Waihi’s Rugby Park |
1955 | G. A. Wooller and Green and Cooper (Pye’s N.Z. agents) absorbed. Akrad principal manufacturing unit |
1958 | Development and production of first single cabinet stereogram. First use of printed circuits in New Zealand |
1959 | First production run of black and white television |
1960 | First Paeroa factory opened in leased premises |
1961 | First Hamilton factory opened |
1962 | Opening of Moresby Avenue plant |
1963 | Opening of Barry Road research and development laboratory |
1963 | Opening of own building in Paeroa |
1964 | Staff peak at over 500 in production of black and white television. Paeroa factory gutted by fire and rebuilt. Opening of Paeroa record pressing plant |
1966 | Introduction of highly successful “Sea Phone” line |
1967 | Pye of Cambridge sold to Philips |
1974 | Colour television production commenced |
1977 | Paeroa record factory closed. Takeover of Pye U.K. completed |
1979 | Philips took over Pye N.Z. Ltd |
1981 | Paeroa closed. Philips policy of universal rationalisation introduced. Colour TV moved to Naenae and all audio production to Waihi |
1982 | 50th anniversary celebrations |
1983 | Frankton closed. Major redundancies |
1984 | Sees the beginning of climb back to full production. Introduction of non-audio lines |
1986 | Pye Waihi factory closed |
Appendices
Speaker Production in Waihi
After the second world war Pye U.K. was getting back into domestic production using (amongst others) makes of speakers Reproducers & Amplifiers Ltd (R & A), of Frederick Street,Wolverhampton (Celestion, Goodman and Elac were also used in production sets in Cambridge).
Prior to Pye U.K. acquiring R & A in the 1950’s, Akrad (Auckland Radio) was assembling Celestion speakers in kit set form where the line was set up in an extention of The King’s Hall, known in those days as, ‘the second saw tooth’, and supervised by Ernie Thompson.
A motor driven high current D.C. generator (part of which was mounted under the bench) was used to energise the speaker magnets. The magnetic field was so strong, the operator had to remove their watch or it would be damaged.
After the take-over of R & A, Pye U.K. were producing speakers but kept the name R & A. then after 1951, when Pye U.K. took a controlling interest in Akrad, R&A speakers were supplied to Akrad in kitset form, so a new line to assemble them was set up in the King’s Hall.
Towards the end of the ’50s it was felt that speakers should be manufactured in Waihi, not just assembled from kitsets, so Mr Ron Skinner went over to Pye, Cambridge, to arrange for the R & A machinery to be shipped to N.Z.
This machinery was crated and loaded in the U.K. onto a ship in early 1960. In the shipment were five large presses which arrived in Auckland in late 1960. The largest press was 100 tons and there were four smaller ones of 75, 60, 25 and 10 tons and other equipment (including a centerless grinder, a broaching machine, two Ward lathes and a lot of “go no go ” gauges to check the machined parts, etc). These were put onto railway wagons to go to Waihi.
At Waihi station, the presses were manoeuvred off the railway wagons, using a crane operated by Billy Brooks, onto trucks to transport them to the factory. The crane then lifted the presses off the trucks where the crates were removed and some parts like the fly wheels taken off to lighten them. With the aid of 10 ton hydraulic jacks, they were then tipped on their sides. The next stage was to get them up a special ramp built in the loading bay and into the machine shop. Danny Farmer’s bulldozer was called on to do this. Heavy wooden planks were laid on the machine shop timber floor to carry the weight, so the presses could be manoeuvred to the concrete pads which had been poured well before hand. The jacks were again used to stand the presses upright. The whole operation was organised and supervised by Henk Bouius. With these presses and all the other machines operating in the machine shop, there was a considerable amount of noise generated.
During the production process, wear and tear of the machines would require them to be maintained. The broaching machine repairs could not be done in New Zealand so the parts needing repair had to be sent back to Sheffield in the U.K. Other repairs could be carried out in the tool room.
To paint the speaker parts an electrostatic painting system had to be set up in the paint shop along with a conveyer belt. Operators had to be earthed or they would be electrostatically charged as well.
The assembly line had been set up in the King’s Hall alongside the coil winding section, where the speech coils were wound. Four winding machines were set up on half the stage, the other half became the relay department. The speaker line was run by Murray Radford.
Speakers from 3 inch (tweeters) to 10 inch (woofers) were produced under the label ‘R & A Made in New Zealand’, with the type number hand written at three o’clock. Later this label was dropped and in the mid 1970’s was replaced by ‘Pye, Manufactured in New Zealand’ with the type number (hand written again) in the centre.
To magnetise the speakers a very powerful magnetic field was required and an electric motor driving a D.C. high current generator was again used. Later a three phase power and rectifier system was built to magnetise the speakers. Again the operator had to make sure that his/her watch was removed or the magnetic field would damage it. The speaker magnet assembly was of the ‘closed pot’ type, which was needed for television since with no external magnetic field there was no distortion of the picture. Thus the speaker could be mounted in the T/V cabinet close to the picture tube.
In 1977, when the Paeroa record factory was closed, the speaker production line was moved to take its place. Speaker production continued until Philips closed the plant in 1986.
Departments in No 1 plant.
- Plastics:- Producing T/V backs and tube surrounds.
- Winding room:-Coils and transformers.
- Speaker Dept.
- Relay Dept.
- Trike line.
- Plating Shop:- Nuvat de-greasing tank, zinc plating tank, barrel plating, passivating (standard plus brown and black). Aluminium treatment. Buffing room.
- Paint Shop:- Conveyor belt spray booth with water screen and drying oven. Chlorothene V.G. de-greasing tank.
- Silk Screen Room:- Producing radio dial scales and printed circuit boards.
- Machine Shop:- Presses (up to 100 tons), fly presses, lathes, bending machines, power and foot operated guillotines, milling machines and shapers. Granodine chemical tank.
- Tool Room:- Electronically controlled machines making press tools. Lathes, grinding machines, drilling machines and special production tools. Drawing office.
- Store:- Sheet metal, tube, tools and drills.
- Locker room and toilets.
Departments in No 2 plant.
- Ground floor.
- Main office:- Board room, accounts, purchasing, offices for factory manager, production manager, chief accountant and management team. Personnel officer’s office. Cafeteria. Toilets.
- Production floor with loading bay.
- Goods in, goods out. Main store. T/V production line. Portable and table radio, radiogram and HiFi audio production lines. - Telecommunications production line. Spares store. Offices for supervisors. Closed circuit T/V transmission equipment room (test pattern piped round both No 1 and No 2 plants). First aid room. Locker room and toilets.
Bibliography
Go Waihi, “The Pye Story”, 2011
NZ Vintage TV & Radio Blog, “NZ Vintage TV & Radio”, 2014
Skinner, R E , “The Story of Akrad Radio Corporation Ltd.”, The Waihi Leader, July 4 2000
Waihi Museum, “Museum and Research”, 2012