Table of Contents
Merging the Process Map, FMEA and Control Plan
A Hybrid Approach
Steve Burkhart
hybridfmea@gmail.com
Abstract
This document explores the development and interaction of the Process Map, FMEA, and Control Plan as a single document, and outlines a novel approach to its creation. The ideas expressed here are the result of my practical experience over the years in using these documents, and my recommendations for improving them for ease of use and maintenance. These documents are traditionally formatted to exist as separate, stand-alone entities, fitting on an 8½” x 11” sheet of paper, which is inherently an isolating condition, creating opportunities for discontinuity and difficulty in implementation. Merging all three forms can both speed their completion and act as an effective error-proofing measure, helping to eliminate inconsistency between elements.
Keywords: Process Map, Process Flow, Failure Mode Effects Analysis (FMEA), Control Plan, Pre-Production Approval Process (PPAP), Advance Product Quality Planning (APQP), Automotive Industry Action Group (AIAG)
Introduction
Today, many industries require the effective implementation of APQP to make sure that the delivery of goods and services are planned for and executed in a way that meets their customer’s requirements for timing and quality. Cross-functional teams determine how specific customer requirements can be met by creating a process flow chart, next the FMEA that identifies the risks in product realization, and finally the Control Plan that demonstrates the specific measures the organization takes to ensure that the risks are mitigated and that defective units are not delivered to the customer.
If you are a Manufacturing Engineer or a Quality Engineer, you have probably been involved with developing these documents in a team setting, but often times in isolation, which is frequently the case when deadlines are looming and it is “All hands on deck!” Perhaps you have gone into a Control Plan development meeting, with printed copies of the FMEA for the participants, or you had to bounce back-and-forth between the electronic Process Map, the FMEA, and the Control Plan, while viewing them projected upon the conference room screen, unable to see them all at the same time. And why is it that we live with this juggling act? Admit it, if this were a production setting and an operator needed to have multiple sources of data available simultaneously for quick review, the Manufacturing Engineers and the IT folks would a have graphic user interface dangling at eye level with color coded data fields on a touch screen. So why is it that the very people who plan and execute the design and implementation of manufacturing processes, constrain themselves by the size of a sheet of paper?
You may be wondering what the size of a sheet of paper has to do with Process Maps, FMEAs and Control Plans, but it is this very thing, this limiting phenomenon that once shackled to our imaginations, robs us of the ability to see new ways of doing things. Paper is sized for what is most universally needed by the market that utilizes it. People want paper that when bound together is of a convenient size and weight to be used, carried, and stored. When computers were put into mainstream use, they were used to help simplify and streamline the creation and use of digital records and processes. People took their paper forms and duplicated them digitally. The monitors that we use to display them, while having modestly increased in size over the years, in effect have been made to replicate a “page” of useful data or images.
Problem Statement
We know that the FMEA must follow the steps of the Process Map, and the Control Plan must match the FMEA, line-by-line, otherwise we have not created a seamless plan for ensuring that the requirements of the customer are met. Knowing all of this, why are these three documents, separate documents? By separating them, but requiring 100% agreement, we are knowingly accepting the risk that we are sowing the seeds of trouble. Have you ever had an auditor find a specific failure mode in your FMEA that had no corresponding line in the Control Plan? Have you ever noticed that all of the steps of a particular Process Map were not quite reflected in the FMEA? How about discovering that because of unrealistic time constraints, under-staffing, or a combination of both, the FMEA was just a rough summary of the main processes, and the Control Plan was a gaping breach in the wall, ignoring many significant steps and risks? More times than I care to admit, I have seen desperate people do desperate things, creating three separate documents that could not talk to each other, but they were honestly able to say, “The FMEA (or Control Plan) is done!”
Solution Approach
What if each line of the Process Map was shared by the corresponding lines of the FMEA and Control Plan? Yes, that does seem like too much information all in one place. At first blush, your assessment would be that there is no way to do that, because the row would run too far off the right side of the monitor, requiring too much horizontal scrolling, and in order to see the entire form, the zoom level would have to be so high that the text would appear nearly microscopic. According to the standard AIAG formats, that would be the case, but if we were both creative and selective with the data we chose to display and the manner in which we displayed it, I believe there is a method to merge the Process Map, FMEA and Control Plan, so that they are effectively usable on one screen, and if so desired, able to be printed as one effective document.
There are many benefits to this type of arrangement. You would immediately notice that you would not have to refer back and forth between multiple documents when working in this format. This would especially be a blessing when creating the FMEA and the Control Plan, because the “source material” needed to proceed is right there in-line for you to reference. Another benefit is that it delivers on the requirement for consistency throughout all three documents; as long as each line is complete, you know that you have delivered something seamless; this is a huge advantage over other methods! If you were to utilize this convention, gone would be the days of needing to have two or three separate documents open at the same in order to perform a line-by-line check.
Here are the typical column headings used in most FMEAs and Control Plans:
• Operation Number
• Process Function
• Process Failure Mode
• Potential Effects of Failure
• Severity
• Class
• Potential Causes of Failure
• Occurrence
• Current Process Controls
• Detection
• RPN
• Machine, Device, Tool, Jig for manufacture
• Characteristic Number
• Product CharacteristicProcess Characteristic
• Special Characteristic Class
• Sample Size
• Sample Frequency
• Control Method
• Reaction Plan
• Recommended Actions
• Responsibility and Target Completion
• Actions Taken
• Severity
• Occurrence
• Detection
• RPN
You may be wondering what is wrong with that list. I tucked the Control Plan (sans “Part/Process Number” and “Process Name/Operation Description”) right in the middle of the FMEA. In order to merge the three documents, it is useful to remove redundant columns, but not mandatory. When using this hybrid document format to complete the FMEA, it may be advantageous to use the spreadsheet “hide” function to remove the Control Plan from view, and then “unhide” it to complete the Control Plan. Also, this gets the FMEA improvement section out of the way while working on the Control Plan.
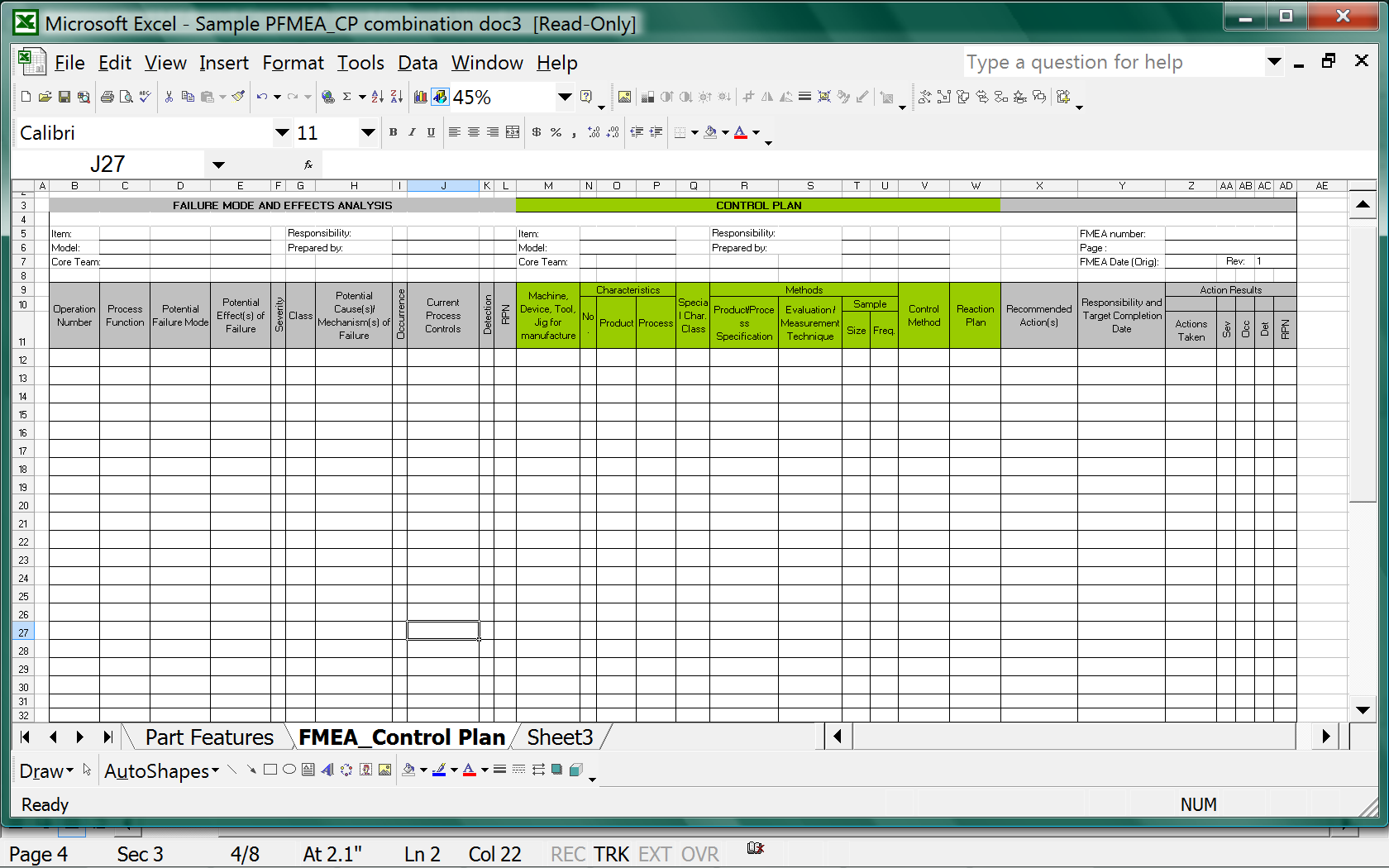
Control Plan Visible
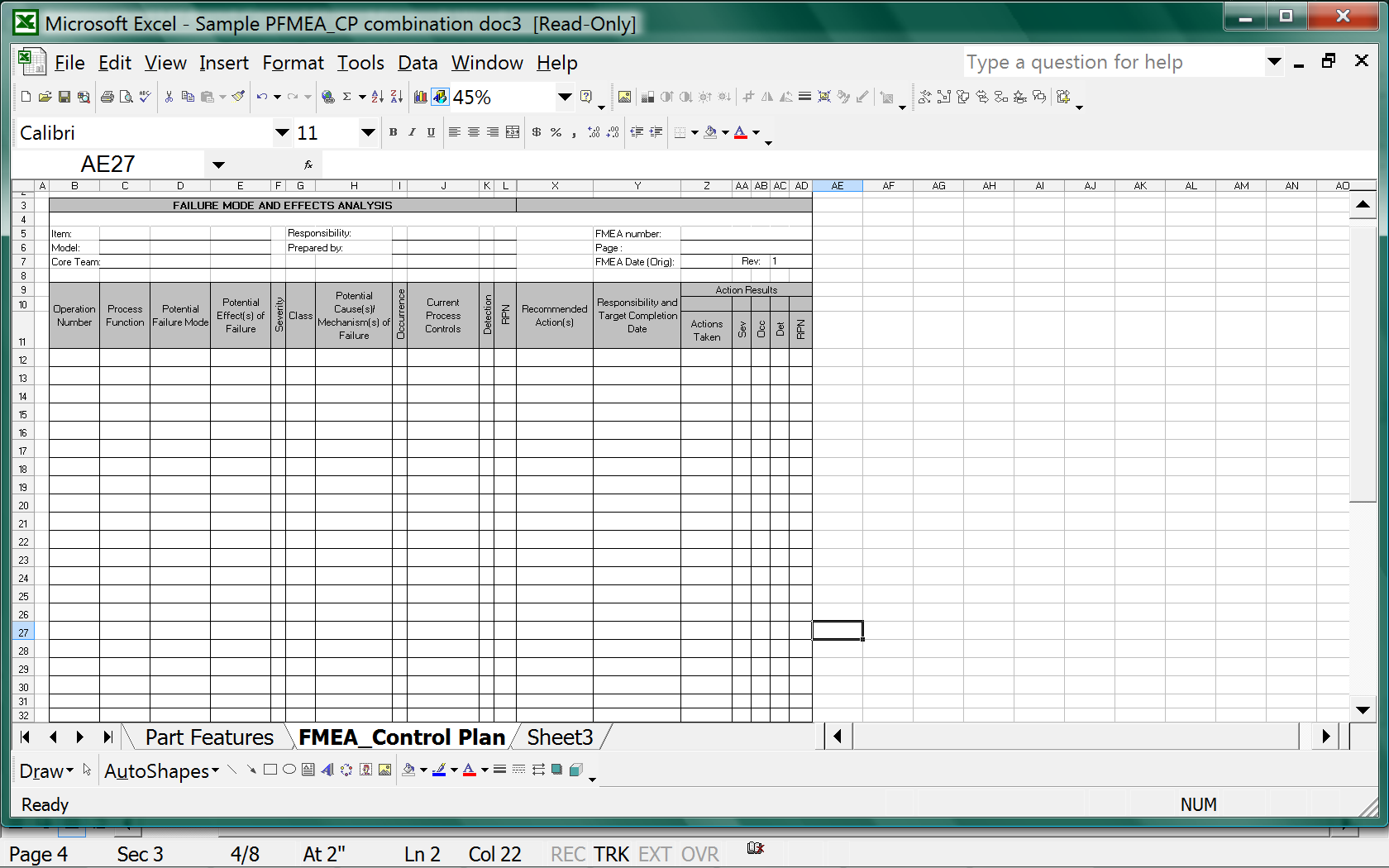
Control Plan Hidden
The benefits to this hybrid format are readily apparent to anyone who has had to create and maintain separate documents before. Begin the Process Flow by populating the “Operation Number” and “Process Function” columns with the FMEA. Create the FMEA by inserting additional rows within the Process Flow. Create the Control Plan by reading across the FMEA, ensuring that the controls you establish are specific to the failure modes identified within that same line.
Conclusions
- No special software is needed to implement this method; use your favorite spreadsheet program
- It is more difficult than the standard methods, to have logical discontinuity between elements
- Editing and building a completed document is streamlined because:
- You can copy and paste whole lines, or entire operations
- No switching is needed between documents
- The completed document prints conveniently in landscape view on 11”x17” paper
- Auditing is simple and straightforward
I hope that this out-of-the-box approach to Process Maps, FMEAs and Control Plans is helpful to you and to your organization.
References
AIAG Production Part Approval Process
www.aiag.org