Table of Contents
- Introduction
- 1 Gradients and Variables
- 2 Outline of the Grid Method
- 3 Choosing a Starting Point
- 4 Working Out the 35 Glaze Recipes
-
5 A Guided Tour
-
- Isolating Variables
- Standard Limestone Set (The 0.7 Limestone Set)
- Corner A - High Alumina
- Corner B - Low Flux
- Corner C - High Flux
- Corner D - High Silica
- Magnesia Glazes
- Strontium Glazes
- Barium Glazes
- Zinc Glazes
- Feldspathic Glazes
- Alkaline Glazes
- Volumetric Addition
- Clay Body and Firing
- Using the Grid
- Family Set
- Exploring the Limits
-
- 6 Preparing, Firing and Assessing a Grid Set
- 7 Volumetric Addition to a Set
- 8 Using the Grid Method with Natural Materials
-
Appendices
- Appendix 1 Equipment and Materials
- Appendix 2 Safety and Health
-
Appendix 3 Useful Maths and Chemistry
- Reading a Chemical Formula
- Some Raw Materials
- Three Ways to Look at a Glaze
- Recipe
- Oxide Weight %
- Seger Formula
- Comparing Recipe and Seger Formula for 3 Standard Recipe Grids
- Reformulating Glazes
- Chemically Identical Glazes from Different Materials
- Essential Maths
- Percentages
- Percentage Calculation:
- Ratios and Proportions
- Volumetric Addition to a Set
- Loss on Ignition - Calcining Calculations
- Calculating L.O.I.
- Calcining Calculations
- Appendix 4 The Recipe Table and Flux Breakup Tables
Introduction
Firstly we need to cover a few basics for those who’ve not met up with glazes before…. briefly:
What is a Glaze?
Glaze is a special glass.
A base glaze is the glaze before we add any colourants or opacifiers. It consists of three main ingredients:
- A glass former (this is essential), usually silica.
- Some fluxes (essential) to melt the silica at a reasonable temperature. Normally we use more than one flux.
- Alumina (nearly always) so the glaze is not too runny.
To the base glaze we can add colourants or opacifiers and other additives(optional).
We will learn the chemical formulae for the twelve oxides used in the base glaze as it only takes a minute, and it makes accessible a lot of useful information.
Ian Currie’s Blue-in-the-Face Chemistry Course.
The deal is I hold my breath until the student understands all the chemistry he or she needs for this method. I’ve not passed out yet. Starting now:
We need to be able to recognize the formulae of these 12 oxides.
\(\textbf{R}_{\textbf{2}}\textbf{O}\)-type fluxes: |
1. \(Li_{2}O\) is Lithium oxide |
2. \(Na_{2}O\) is Sodium oxide |
3. \(K_{2}O\) is Potassium oxide |
\(\textbf{RO}\)-type fluxes: |
4. \(CaO\) is Calcium oxide |
5. \(MgO\) is Magnesium oxide |
6. \(ZnO\) is Zinc oxide |
7. \(SrO\) is Strontium oxide |
8. \(BaO\) is Barium oxide |
9. \(PbO\) is Lead oxide |
This one is both a flux and a glass former: |
10. \(B_{2}O_{3}\) is boric oxide |
Stiffener: |
11. \(Al_{2}O_{3}\) is Alumina |
Glass former: |
12. \(SiO_{2}\) is Silica |
It’s also useful to know that: |
\(H_{2}O\) is water |
\(CO_{3}\) is carbonate |
These last two are sometimes found in the raw materials, but disappear during the firing. [Take a breath, Ian!]
There are more, but in this method we only need to know the formulae of these 12 oxides that go to make up the base glaze.
Raw Materials
Glaze theory would be easy if we made our glazes of just these twelve oxides, but when we come to mix the ingredients together in the bucket, for practical reasons only a few are used in the pure oxide form. (Some are soluble, some react with water etc.) Many raw materials are compounds of several oxides, some are carbonates, some hydrates (containing \(H_{2}O\)).
Oxide | Some Common Sources* |
---|---|
Flux Materials: | |
\(Li_{2}O\) | 1. Lithium carbonate, Petalite, Spodumene |
\(Na_{2}O\) | 2. Soda feldspar, Nepheline syenite, Frit |
\(K_{2}O\) | 3. Potash feldspar, Frit |
\(CaO\) | 4. Whiting, Limestone, Wollastonite, Wood ash |
\(MgO\) | 5. Magnesium carbonate, Dolomite, Talc |
\(ZnO\) | 6. Zinc Oxide |
\(SrO\) | 7. Strontium carbonate |
\(BaO\) | 8. Barium carbonate |
\(PbO\) | 9. Frit |
\(B_{2}O_{3}\) | 10. Frit, Colemanite, Gerstley borate |
Sources of Alumina and Silica: | |
\(Al_{2}O_{3}\) | Clay, Kaolin, Alumina |
\(SiO_{2}\) | Silica, Quartz, Flint |
Once again, there are many more sources than those listed here. But just for now, we are trying to get a feeling for how it all hangs together.
An Approach to Studying Glazes
Origins
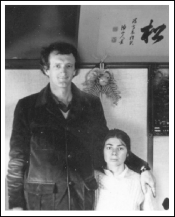
My wife Christine and I spent over a year in Japan in 1971 and 72. I went there on a travelling art scholarship to study Japanese Ceramics, and one of the things I focused on was the Japanese approach to studying glazes. It was interesting because they had applied western methods of glaze technology to their traditional glazes, and I found this fusion of the western scientific approach and traditional empirical methods. I learned from a variety of sources. We traveled around Japan to the various ceramic production centres visiting potteries and potters, and also visiting the local ceramic research centres. I also had a series of private tutorials with a leading glaze technologist, Mr. Masataro Ōnishi.
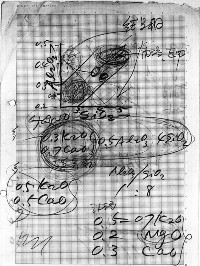
This was about thirty years ago, and in the west ceramic artists didn’t know anywhere near as much as we do now. It was common for potters to be completely secretive about their glazes, and to find this stuff being freely taught and in their textbooks made me feel I had come to the source!
Anyway, Mr. Ōnishi and I would sit on opposite sides of a coffee table, and he would scribble out notes while explaining. My command of the language was fairly basic at this early stage in the tour, but we both understood Seger formula, which is a universal language. At that time, many potters were of the opinion that for a glaze all you needed was the glaze recipe. He presented me with this 7 point approach to glaze research:
The 7 Point Approach:
1. \(R_{2}O.RO\) (Fluxes)
2. Alumina/Silica ratio
3. Amount of Silica
4. Colourants and/or opacifiers
5. Clay Body
6. Special requirements of any materials, e.g. special source, fine, coarse etc.
7. Special firing requirements
He introduced me to the concept of a standard limestone glaze. He would write the Seger formula for this standard:
\(0.3 K_{2}O\) | ||
\(0.5 Al_{2}O_{3}\) | \(4.0 SiO_{2}\) | |
\(0.7 CaO\) |
and locate it on an alumina/silica diagram as a kind of datum point in the middle of this glaze landscape, a peg in the ground so you knew where you were and from which you could look around. He would relate all glazes back to this one standard. This glaze is almost identical to the glaze right in the middle of the 0.7 Limestone Set, a set of 35 glazes which we will use as our own datum. I.C.
Some Standards
1. Standard Cone 9~10 Limestone Glaze
A recipe for Ōnishi’s glaze is: |
42% K Feldspar |
27% Silica |
18% Whiting |
13% Kaolin |
2. Bernard Leach Glaze Looking at the recipe in 1. we find it is close to another standard glaze:
Bernard Leach’s Cone 8 Limestone Glaze |
40% Feldspar |
30% Silica |
20% Whiting |
10% Kaolin |
(Published in his classic “A Potter’s Book” in 1940, an early 4:3:2:1 glaze.)
3. Standard pyrometric cones
In the midfire to porcelain range and higher the flux composition of standard pyrometric cones is the same as that in Ōnishi’s standard glaze. If we severely overfire the actual cones they produce a clear shiny limestone glaze. Ōnishi’s Standard Cone 9~10 Limestone Glaze has roughly the same chemical composition as cone number 4.
Extending the Range
There is a reason why glazes like this have been adopted as a standard. They are typical, reliable, middle-of-the-road glazes with a good firing range and few problems. Varying the 4 glaze ingredients produces a very wide range of possible glazes from high feldspar, to high calcium to high alumina to high silica glazes. And this glaze is more or less right in the middle of the possible range for Cone 9 to 10.
Later we will consider an exercise to produce the 0.7 Limestone Set. In this exercise we keep the \(\textbf{K}_{\textbf{2}}\textbf{O}\) and \(\textbf{CaO}\) constant in the proportions given in the Standard Cone 10 Limestone Glaze, and vary alumina and silica over a wide range above and below the figures shown above in the Seger formula. Mr. Ōnishi’s glaze sits almost exactly in the middle of this set. Similar sets are presented for midfire and earthenware firing ranges.
The high lime content of the 0.7 Limestone Set gives us a good stable base to start from. We can then explore the introduction of other fluxes by replacing some of the lime with magnesia (\(MgO\)), zinc oxide (\(ZnO\)), baria (\(BaO\)), Strontia (\(SrO\)) etc. Also the original balance of lime from the whiting and potash from the feldspar will be altered.
The set is named “The 0.7 Limestone Set” because in the Seger formula all 35 glazes contain 0.7 molecular parts of \(CaO\). The midfire and earthenware equivalent sets are similarly high in lime (\(CaO\)) but manage to lower the firing range mainly by addition of \(B_{2}O_{3}\) (in frit), and substitution of soda (\(Na_{2}O\)) for potash (\(K_{2}O\)).
The “grid method” facilitates the full 7 point approach of Mr. Ōnishi. The main focus presented in this book however will be to detail the use of the grid technique; no attempt has been made to provide once again the sort of basic ceramic information that is now so widely available.
A> I have a couple of friends who live in Parkerville in Western Australia. Tim is a geologist and Georgina a potter. There is a geological contribution from Tim in Chapter 8. Our Lives have been spliced together strangely by fate.
A>
A> Just after the War (WW2) when I was about 5 years old my parents and I went to liver at Parkerville. It was probably wher eI was happiest as a boy… our family was back together after the war and Parkerville is a very beautiful place. Eucalyptus open forrest bushland for the most part, then with very few houses, and a beautiful creek called Jane Brook bubbling through the middle. We had a small mixed farm there. Dad ran the only local milk run, and also sold eggs, and seasonally some fruit and vegetables. I dont know enough about this period of my parents’ lives. It seemed very happy but obviously didn’t work out. We were only there a couple of years and then we moved on.
A>
A> In the brief period I was there I connected with Parkerville as children do when they live in such a beautiful place. I had an aunt living nearby in a cottage along Falls Road. Her name is Betsy and she is 96 years old and has always been an artist. (She had her first solo show in 1999.) She lived there with an artist named James Linton in a small cottage he built. It was one of the special plaes in Parkerville. As well as having a currant-grape vine that we could raid, the house was full of wonderful objects. My aunt stil lhas in her flat the 4 feet tall plaster Venus de Milo that stood just inside the doorway. When I asked what happened to her arms, Betsy said she was run over by a train. Not many people know this. The house contained many oriental artifacts.
A>
A> Linton made serveral trips to China in the early twentieth century and had ceramics, chests, furnature, etc and one room of his studio had the smell of turps and oil paints. There were also carved objects made by Linton himself, and also Betsey’s brother Kitchener Currie (Photo in Appendix 3.)
A>
A> I first returned to Parkerville in 1980, and was surprised and delighted at that time ti find how little it had changes. And one of my main visits had to be Betsey Linton’s old house, which I visited twice on that trip. I always find it difficult to intrude and there were people there both times. However on the second visit I decided I wasn’t a shy 6 yea old any more, and plucked up my courage, went back and introduced myself as Ian Currie who had lived in the area 33 years ago and whose aunt used to live here and would they mind if I looked around. There was a man and a woman and a couple of kids.
A>
A> They said they didn’t own the house, were just looking with a view to buying, and who was my aunt? I told them and the woman exclaimed that Betsey Linton was a very good friend. They knew that she had lived in this house and they had heard it was for sale.
A>
A> I had a good look around the garden and through the house absorbing as moch as I could, then having come 33 years through time and thousands of miles through space to place my imprimatur upon the deal I stepped back into my Tardis and space/time-transported out of there. Tim and Georgina, for it was they, bought the cottage! I’ve been back numerous times since, and they have become dear friends. Seeing how the place affected me, they offered me “land rights” - the right to come and go in their home as I please - in the house where my Aunt Betsey and James Linton used to live! Now that is a gift!
1 Gradients and Variables
The Holy Grail
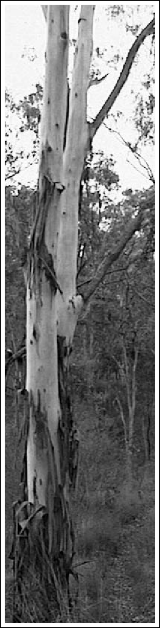
To some extent every problem contains its own solution, and every stumbling beginning contains the seeds of success. Every firing can be an experiment that points the way to the solution of problems, or further evolution. There’s a kind of paradox here that relates to the pursuit of uniformity. In industrial ceramics, the engineers are usually trying for total control, and to have kilns that fire with perfect uniformity. Most artist potters on the other hand regard control as just one tool that may be used in the pursuit of artistic excellence.
This attitude has an unexpected technological benefit. Imagine 100 identical pots being subjected to identical firing conditions. Any mistake that occurred would show on all the pieces. Despite the occasional paranoia that we have personally drawn this short straw, what usually happens is that problems appear only on some pieces and in some places. A close examination of what is different between success and failure allows us to guess at theories about the nature of the problem and its solution. So the lack of uniformity is revealing variables that can lead us to better results. There’s a sort of Darwinian selection process going on here, with the variation being caused by the crude technology, and the selection process being decided by human choice.
In China and Korea stoneware glazes first developed as a result of potters observing the results of a very haphazard technology. In the first place they noticed that the pots that got hottest became stronger and non-porous. This was fairly easy for an observant potter to discover with such difficult and uneven kilns; it was obvious the pots next to the firebox became tougher. So as a result of the inefficiency of the kiln, a temperature gradient well understood by the potter was pointing the way to better pots. To get stronger and less porous pots they fired higher and higher. Eventually something interesting happened; a shiny, runny glaze appeared on the front of pots near the firebox. Careful observation through the kiln as they unloaded the fired pots would have confirmed that it was simply melted ash. There would have been a gradient through the kiln going from near the firebox where the ash melted to where the ash was completely unmelted, with every stage in between.
Any sort of gradient can provide useful information; we artificially create a glaze composition gradient when we create a line blend. There are all sorts of gradients through the kiln and across a pot. They are caused by variations in temperature and kiln atmosphere, heating and cooling rate, glaze thickness, wood ash and vapour deposit. By observing where changes occur and where they don’t the potter is able to detect subtle variables that can eliminate a problem or promote a benefit.
Thinking further about this built-in evolutionary trend in any primitive technology we are able to see also how it leads in the longer term to cycles of building up followed by stagnation, devolution and then regeneration. Thinking back to the example of the ancient potters using the gradients in the kilns to guide their improvements, we can see that for many it has now evolved to the opposite end of the scale, where a high degree of control and predictability is possible by many potters. For some, the reason for making pots is to make money. This guides the hand towards choice of reliable and reproducible methods and materials.
Sometimes we find ourselves doing this for sheer economic necessity in the effort to avoid the starving artist syndrome. But for those drawn to ceramics out of a love of creativity, there is a sting here. Just when we are getting things under control and could gain a little wealth, stability, certainty in our lives, something happens and we feel bored. This seems unfair, but upon reflection we discover that it is inevitable. As sensitive and creative people, we are excited by discovery, revelation and insight whether from our own efforts or the efforts of others. When something is predictable, there is no discovery, no insight, and no revelation… just a predictable variation on an old tune. Boring!
Once our kilns and materials and techniques produce the same perfect thing every time, not only does it become boring (except for the thought of the money it might bring!) but also we are suddenly not learning anything from each batch of pots we fire. We are cut off from a natural source of evolution. If we want improvement we have to consciously conduct a research program.
There is nothing intrinsically wrong with all this, but something that probably started with idealism and great enthusiasm can thereby become tiresome. We need a balance. And the balance comes from a return to basics. We need to reclaim the excitement of discovery, and the satisfaction of taking big risks and being lucky. And so we start anew like the old potters with their primitive kilns and glazes and the cycle begins again… we arise phoenix-like from the ashes of certainty and boredom to reclaim life.
Some have a problem with this treadmill. What is the point? Will we ever achieve true satisfaction and happiness and the perfect glaze?! Yes indeed! But we must be aware that we never stop growing. The Holy Grail once achieved does not guarantee eternal bliss! Once obtained, perfection provides the launching platform for the next endeavour. It’s the old story of the journey being more important than the destination - and it generates meaning in our lives. And attitude is everything! The ancient potter on seeing the runny shiny stuff on some of his pots could have viewed it either way: an annoying flaw or a gift of possibilities - a doorway to be ignored or entered through.
Isolating Variables
Line Blends
We have seen above how gradients can reveal important variables. The gradient makes the variable visible and tangible. We can see the effect of the variable with our own eyes, and seeing the effects, we can deduce causes. This helps point the way to better results. Experimenting with glazes we can use line blends to artificially create gradients of glaze composition. Line blending is one of the basic experimental procedures that the ceramic artist needs to understand. This is not difficult, but by putting a little thought into the experimental design we can get more from the results.
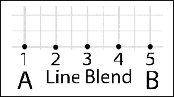
A line blend is a series of glazes obtained by blending two glazes together. The compositions of the blended glazes are intermediate to the two original glazes. In our diagrams we will represent a line blend as a series of dots as illustrated here.
If possible we design our line blend so there is just one variable. If we do this, we get more than just a range of glazes; we can see a clear indication of the effect of the one chosen variable, without being confused by others.
So to come to grips with fundamental cause-and-effect principles we need to design our experiments so we can isolate or separate out the variables. We can understand this point with a few examples of different sorts of line blends…
Different Kinds of Line Blends
- Addition Line blend - 5 Recipes
Glaze No: 1 2 3 4 5 Glaze X 100 100 100 100 100 Colourant 0 2 4 6 8 The only variable here is the colourant.
- Crossover Line Blend - 5 Recipes
Glaze No: 1 2 3 4 5 Glaze A 100 75 50 25 0 Glaze B 0 25 50 75 100
With a crossover line blend there is no guarantee of being able to neatly separate out a single variable. After all, the two glazes could be completely unrelated, and we might be dealing with a dozen variables from the two glazes all changing at once.
If however the two glazes are carefully chosen, we can have a crossover blend with just one variable. See the example following in “Working Out the Recipes in a Line Blend”.
Working Out the Recipes in a Line Blend
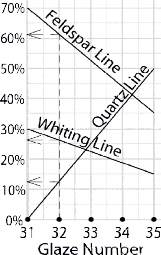
The simplest way to visualize the maths of a line blend is to plot one out on a piece of graph paper. Consider the two recipes:
Glaze Name | Glaze C | Glaze D |
Feldspar | 70 | 35 |
Whiting | 30 | 15 |
Quartz | 0 | 50 |
Draw the “Feldspar Line” from 70% above C to 35% above D (see graph). Similarly draw in the Whiting and the Quartz Lines using the figures from the table.
Five glazes occur at equal intervals along the horizontal axis. If for example we wish to get the recipe for Glaze 32, we follow the dotted line up from 32 and see at what % it intersects the three sloping lines. We read the % figures at the arrows:
Glaze No. 32:
61\(\frac{1}{4}\)% Feldspar
26\(\frac{1}{4}\)% Whiting
12\(\frac{1}{2}\)% Quartz
Check that the figures add up to 100% or very nearly. We can achieve this accuracy if the graph paper is large enough. Use at least an A4 or standard Letter size.
Note that as well as the original 5 recipes we can read off the percentages for glazes that fall between them.
Biaxial Blends
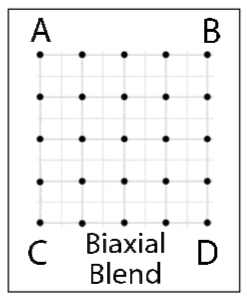
A biaxial blend is a two-dimensional experiment in a grid format. The two dimensions allow us to separate out a maximum of two independent variables. Any of the rows of glazes horizontally or vertically is a line blend. In the example, the whole set of 25 glazes can be prepared by blending from the four “corner glazes” A, B, C and D. The standard “grid” used in the experiments in this book is a 5 X 7 biaxial blend, totaling 35 glazes.
Blending and Trending - A Puzzle
In a line blend we will often see a steady trend in glaze characteristics from one end to the other. Our common sense tells us that this should be so. However this is not always the case. It is possible for example to blend between two stiff matt glazes hoping for a combination of desirable properties somewhere in the middle only to find the intermediate glazes are shiny and runny. This will happen if we choose to blend between two glazes on opposite sides of a strong eutectic trough (see references). In some cases where we are blending from one colourant to another the colours blend as colour theory would predict. But this also can give surprises. For example, mixing manganese and chrome oxides will not produce an intermediate colour. Instead we get dark opaque colours resulting from a chemical reaction between the colourants.
In the next chapter, we see how to incorporate the idea of isolating variables into a coherent standardized experimental method
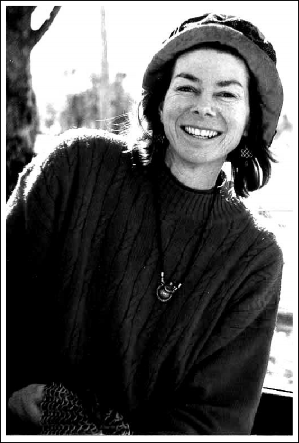
2 Outline of the Grid Method
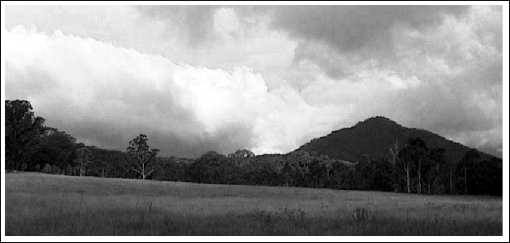
The 3 main variables in the base glaze are fluxes, alumina and silica. The power of this method comes from the systematic variation of these variables using a standardized and simplified experimental approach.
The Standard Grid
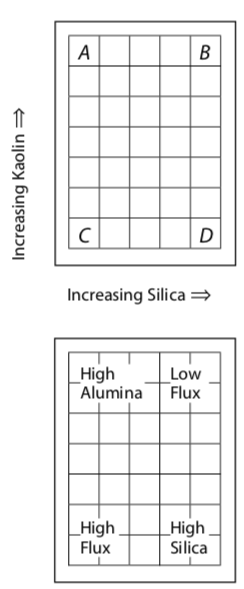
Varying Alumina and Silica: The central experimental format is the “grid” of 35 glazes on one large tile in a 5 X 7 layout displaying 2 of the 3 main variables:
1: alumina increasing from bottom to top (as a result of increasing kaolin) and 2: silica increasing left to right.
Varying Fluxes: In any one set, the proportion of flux materials, one to another, remains constant. To alter this third variable, we have to do a different set of 35 glazes.
In the second diagram we can see four zones that result automatically from the way we have increased the alumina and silica. The zone in the middle of the set can usually be regarded as “well balanced” glazes, or in other words, not “high” or “low” in anything. Don’t forget that all the glazes contain fluxes as well.
Starting Point
An examination of these two diagrams will show that corner C has minimum alumina and silica. To understand the grid method this is where we start; the glaze in this corner is a mix of just “flux materials”. We refer to Glaze C as the “Starting Point” for the set. For example it might consist of 70% feldspar plus 30% whiting*.
Varying Alumina and Silica
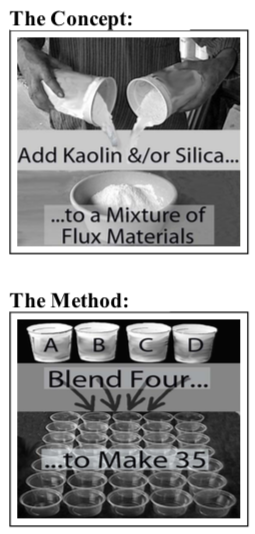
Starting in Corner C made from just flux materials we add in silica (or quartz or flint - these are all more or less pure \(SiO_{2}\)) to move from left to right across the grid. We add kaolin (our source of variable \(Al_{2}O_{3}\)) to go from bottom to top. The 35 glazes are always related to each other in exactly the same way. Essentially, the kaolin and added silica percentages across the grid are the same in every set. These percentages are laid out in the Standard Recipe Grid (see the next page).
To understand the relationship between the 35 glazes, imagine this: Initially we decide on the composition of glaze 31, the starting point glaze, which is composed of 100% flux materials. We could obtain the rest of the 35 glazes in the set by adding kaolin and/or silica to Glaze 31. Therefore the flux materials don’t change as kaolin and silica increase. But this is not how we actually prepare the glazes…..
To prepare a set, we make up the 4 glazes at the corners of the set, numbers 1, 5, 31 and 35, and blend them to produce the rest. [This is just to prepare the set of 35 glazes. Glazes that we might choose from the set to use in larger quantities are prepared in the normal manner. See Chapter 4 for the recipes.]
One set represents the “story” of the set of flux materials originally chosen for glaze 31, examining how it changes as we increase alumina and/or silica.
The Standard Recipe Grid (base glazes)
Glaze Recipes and Glaze Numbering: This diagram shows the recipes for each glaze in the grid (to the nearest 1%). It also shows the standard layout of the glaze numbers from 1 to 35. This layout does not change. [*Note below: “ Fl.Mtl.” = “Total Flux Materials”]
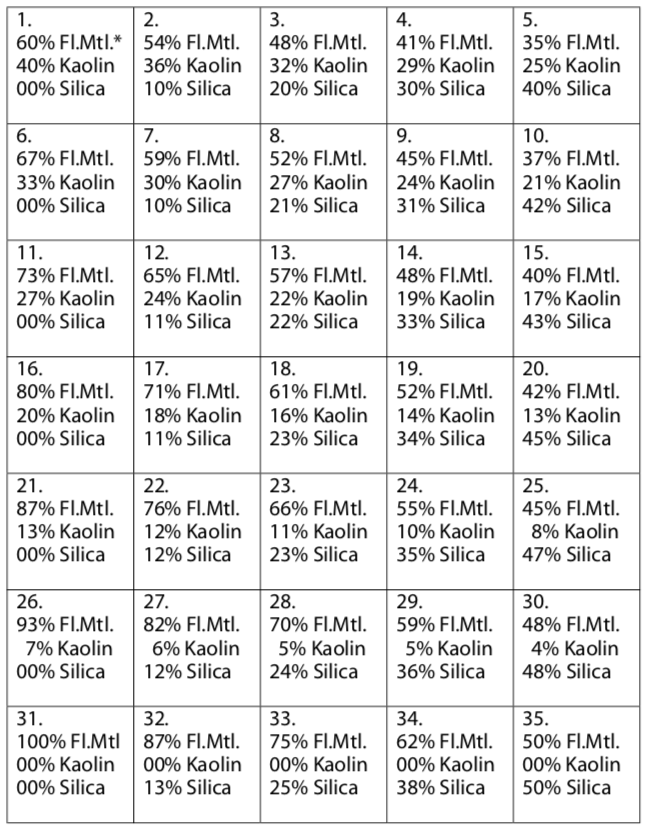
Note the following in the Standard Recipe Grid: 1. Glaze 31 is 100% flux materials. This is Corner C. 2. The bottom row contains no kaolin. 3. The left-hand vertical row contains no added silica. 4. The maximum amount of kaolin is 40% in Glaze No.1 (Corner A). 5. The maximum amount of added silica is 50% in Glaze No.35 (Corner D).
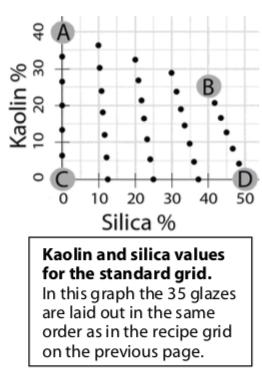
Working out the Flux Material Breakup
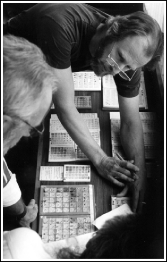
One of the important features of this method is that the percentages in this recipe grid do not change, irrespective of the flux materials used. If the set uses only one flux material, then these are the final recipes… for ANY set. Usually however there is more than one and we have to find the breakdown of flux material. There are several easy ways of doing this, and these will be given in a later section.
One Glaze Recipe Explains the Whole Set
Another result of using this approach is that all the glaze recipes can be worked out once we know the recipe for the Corner C glaze. This is a natural consequence of standardizing the method. This means the only recipe we need to record is Glaze C. From this anyone understanding the method can work out the rest of the 35 recipes if and when required. It also means that we can think of a whole set of glazes just by stating one recipe, Glaze C. We can compare whole sets of glazes one with another just by comparing the C-corner glazes; the difference between sets can be fully understood by examining the difference between the two C-glazes. This is because a particular glaze number always has the same amounts of kaolin and silica in the recipe.
Colourants and Opacifiers in the Standard Grid
It is important when designing an experiment to separate out the variables. In a two-dimensional grid format experiment we can cope with a maximum of 2 variables - for example, silica increasing from left to right and alumina from bottom to top. If we decide to add colourant or opacifier to the standard grid as outlined here, we simply add the same percentage to each of the 35 glazes. This means that the addition of colourant or opacifier is not a variable in this experiment of 35 glazes.
The general rule that will apply for this method is that colourants and opacifiers will be added as a percentage on top of the 100% of the base glaze. See the following example.
Glaze Recipe:
100% Base Glaze
+10% Red iron oxide
Revealing Glaze Principles
As well as discovering interesting glazes, the standard grid method also reveals glaze principles because wherever possible we are separating out the variables. This reveals cause and effect. For example, a glance at a fired standard grid tile reveals immediately the effect of altering alumina or silica on a given set of fluxes. Also, we can see the effect of altering fluxes by comparing the grid tiles for 2 different sets, if they have been fired on the same clay under identical firing conditions.
3 Choosing a Starting Point
The starting point in each set is Glaze C (Glaze No. 31) which is composed of one or more “flux materials” (see List of Flux Materials in this chapter). The purpose of this chapter is to outline some methods for choosing the flux materials for a set. A beginner would be excused for not knowing where to start.
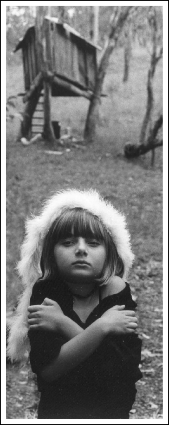
Those new to this approach would be well advised to start with a standard set, perhaps one of the example sets below. It soon becomes apparent however that there are large uncharted oceans awaiting the adventurous explorer. This chapter outlines a way of navigating the unknown and discovering treasure, while gaining deep insight into glaze principles.
Several approaches are given in this chapter:
- Example Sets
We can use some of these suggestions as a starting point. Once a few grid sets have been prepared, the student will inevitably develop a sense of how to choose a set of flux materials for Glaze C. - “Rules of Thumb”
Refer to rules of thumb given in this chapter. - Family Set
We may just choose a known recipe that does something interesting and decide to base a set around the fluxes it uses. This produces the family of glazes with the same set of fluxes as the original recipe (and the same set of colourants/opacifiers, if these are used) but with varying alumina and silica. - Random Selection
If we know nothing, we may even choose a set of flux materials at random! This is not as daft as it sounds.
For this chapter we will focus on gaining some of the theoretical knowledge necessary for making a rational choice of fluxes. It is then up to us individually whether or not we wish to be rational, or go for option 4 above. :) Seriously!
1. Example Sets
Glaze C Recipes
Most of the examples given here are base glaze sets, but we can add a small amount of colouring oxide to all the glazes if we wish. The small amount ensures that the colourant should not significantly alter the glaze characteristics like surface, opacity, crystal formation, maturity, opalescence etc. In other words the glazes should be very similar to the base glazes alone, but with colour. There will be some differences however. For example, there might appear some colour break in some of the glazes. This is where the glaze breaks from one colour to another as thickness varies. Usually we find that the effect is there very subtly in the base glaze set, but the colourant brings it out. Sometimes the colourant, especially iron oxide, will substantially increase the intensity and distribution of opalescence or milkiness in the high silica glazes.
The barium glazes should not be used inside utilitarian ware unless tested safe for barium release.
Although these are all “recipes” we must remember that they are the starting point recipes for the whole set of 35 glazes. It is not intended that students make just these recipes; they are over-rich in fluxes and in many cases will not melt at the suggested temperature range. When we make up a whole set based on one of these starting points however, we should find plenty of melted glazes.
Example Sets - Glaze C
Set 1 - 0.7 Limestone Set - (S)
70 Potash Feldspar
30 Whiting
Set 2 - Feldspar Set - (S)
90 Potash Feldspar
10 Whiting
Set 3 - High Lime Set - (S)
30 Potash Feldspar
70 Whiting
Set 4 - Magnesia Set - (S)
60 Potash Feldspar
17 Whiting
23 Heavy Magnesium Carbonate
Set 5 - Zinc Set (Oxidation only) - (M,S)
60 Potash Feldspar
17 Whiting
23 Zinc Oxide
Set 6 - Barium Set - (M,S)
45 Potash Feldspar
15 Whiting
40 Barium Carbonate
Set 7 - Low Temperature Set (Oxidation only) - (E,M)
60 Ferro Frit 4108 (also 4508 or 3134)
20 Nepheline Syenite
20 Zinc Oxide
Set 8 - Nickel Pinks and Blues (Oxidation only) - (M,S)
40 Potash Feldspar
40 Barium Carbonate
20 Zinc Oxide
(Try adding 2% nickel oxide)
Set 9 - Talc Set - (M,S)
30 Ferro Frit 4108 (also 4508 or 3134)
30 Nepheline Syenite
20 Whiting
20 Talc
(Try adding 0.5% cobalt carbonate.)
Set 10 - Alkaline Set (Includes some matt alkaline glazes) - (M,S)
50 Barium Carbonate
30 Ferro Frit 4110 (or 3110)
20 Whiting
(Try adding some colourant.)
Set 11 - Earthenware Alkaline Set - (E,M)
100 Ferro Frit 4110 (or 3110)
Alternatively, use any low temperature frit.
(Try adding some colourant, e.g. 2% copper carbonate for turquoise.)
Set 12 - Low Temperature Set - (E,M)
50 Gerstley Borate, or High \(B_{2}O_{3}\) Frit
50 Spodumene
Set 13 - Copper Red Set = (M, S)
55 Soda Feldspar
30 Ferro Frit 3134
15 Whiting
+1% copper oxide
+1% Tin Oxide
Set 14 - Magnesia Matt Sett - (S)
40 Potash Feldspar
26 Whiting
20 Talc
10 Dolomite
4 Lithium Carbonate [+ 3% Tin Oxide]
2. Rules of Thumb for Choosing a Flux Set
Broad Principles
- Among the flux materials, we usually choose at least one that contains alumina and silica in addition to the flux component. In the List of Flux Materials these materials are marked with an asterisk *. These are materials like feldspars, frits, and many wood ashes, powdered rock materials etc. We can sometimes use these materials up to 100% in Glaze C, but we usually add other flux materials as well.
- Unless we have very specific objectives, we can put together almost any mix of fluxes in almost any proportions and expect to find glazes that are useful or excellent under some conditions of firing and clay body. In this method there is no “correct” temperature or firing cycle or clay body for a given set. In a particular firing, there will always be some glazes in a set that will be useless (e.g. over- or under-fired) but the systematic variation of kaolin and silica determines that useful (and regularly excellent!) glazes will appear at just the right combination of kaolin and silica. Usually we don’t know just what this combination will be until we do the experiment. Any set can usually be usefully fired over a range of 200 deg. C (360 deg. F) or more.
- To get most of the 35 glazes to melt at mid-fire (1200 deg. C or about 2200 deg. F), we can put up to 35% of frit into Glaze C.
To get most to melt at earthenware (1100 deg C. or about 2000 deg F) we can put 50%, or even up to 100%, of frit into Glaze C. (It is possible to achieve low temperature glazes with just the right mix of “stoneware” fluxes, alumina and silica, but most of the 35 glazes in the set will be unfused.)
Table - List of Flux Materials
Material | Formula | Max C% |
---|---|---|
Barium carbonate | \(BaCO_{3}\) | 50 |
Barium sulphate | \(BaSO_{4}\) | 50 |
Bone Ash (arguably not a flux) | \(Ca_{3}(PO_{4})_{2}\) | 50 |
Calcite | \(CaCO_{3}\) | 60 |
Chalk | \(CaCO_{3}\) | 60 |
Colemanite | \(2CaO.3B_{2}O_{3}.5H_{2}O\) (variable) | 50 |
Cornish stone * | variable | 80 |
Dolomite | \(CaCO_{3}.MgCO_{3}\) | 40 |
Feldspar (Potash) * | \(K_{2}O.Al_{2}O_{3}.6SiO_{2}\) | 100 |
Feldspar (Soda) * | \(Na_{2}O.Al_{2}O_{3}.6SiO_{2}\) | 100 |
Frits * | various | 100 |
Gerstley Borate | Similar to Colemanite with some Na | 50 |
Lepidolite * | \(Li_{2}F_{2}.Al_{2}O_{3}.3SiO_{2}\) (variable) | 40 |
Limestone | \(CaCO_{3}\) | 60 |
Lithium carbonate | \(Li_{2}CO_{3}\) | 10 |
Magnesium carbonate | \(MgCO_{3}\) | 25 |
Magnesium carbonate (light) | \(3MgCO_{3}.Mg(OH)_{2}.3H_{2}O\) | 25 |
Manganese carbonate | \(MnCO_{3}\) | 100 |
Manganese dioxide | \(MnO_{2}\) | 100 |
Nepheline syenite * | \((K)NaO.Al_{2}O_{3}.4SiO_{2}\) (variable) | 100 |
Petalite * | \(Li_{2}O.Al_{2}O_{3}.8SiO_{2}\) | 50 |
Potassium carbonate (Pearl Ash) ~ | \(K_{2}CO_{3}\) | 25 |
Rock powder - Many rocks make excellent | 100 | |
flux materials, e.g. basalt, granite. * | ||
Sodium carbonate (Soda Ash) ~ | \(Na_{2}CO_{3}\) | 40 |
Spodumene * | \(Li_{2}O.Al_{2}O_{3}.4SiO_{2}\) | 70 |
Strontium carbonate | \(SrCO_{3}\) | 50 |
Talc | \(3MgO.4SiO_{2}.H_{2}O\) | 30 |
Whiting | \(CaCO_{3}\) | 60 |
Wollastonite | {$$}CaO.SiO_{2}{/$ | 40 |
Wood Ash (May contain solubles~) * | Variable, (often high in lime) | 100 |
Zinc oxide | \(ZnO\) | 25 |
- The last column on the right in the List of Flux Materials (previous page) shows the recommended maximum percentage of the material to be used in Corner C. (Note that a material used as 100% of Corner C will vary downwards across the set to a minimum of 35% at Corner B. We must think of the whole set, not just the glaze at Corner C.) These guidelines are necessarily approximate because the maximum amount possible in a glaze is determined by many factors including what other oxides are present.
To choose a set of fluxes to achieve a specific purpose requires some knowledge. This approach enables the beginner to achieve a lot with little or no prior experience, and in so doing actually begin to acquire that knowledge.
Advanced Principles
Flux Characteristics Chart
The following chart gives a summary of some outstanding properties of the main flux oxides. The real purpose of this diagram is to illustrate how we can build up a mental image of the properties of the fluxes. We can then better choose appropriate candidates from the List of Flux Materials (on the previous page) to promote particular characteristics, for example alkaline colour response, or large crystals. So this is not a complete list by any means. See the “Guided Tour” chapter for more detailed information on flux behaviour. Also see the references listed at the end of this chapter.
Table - Some Flux Characteristics
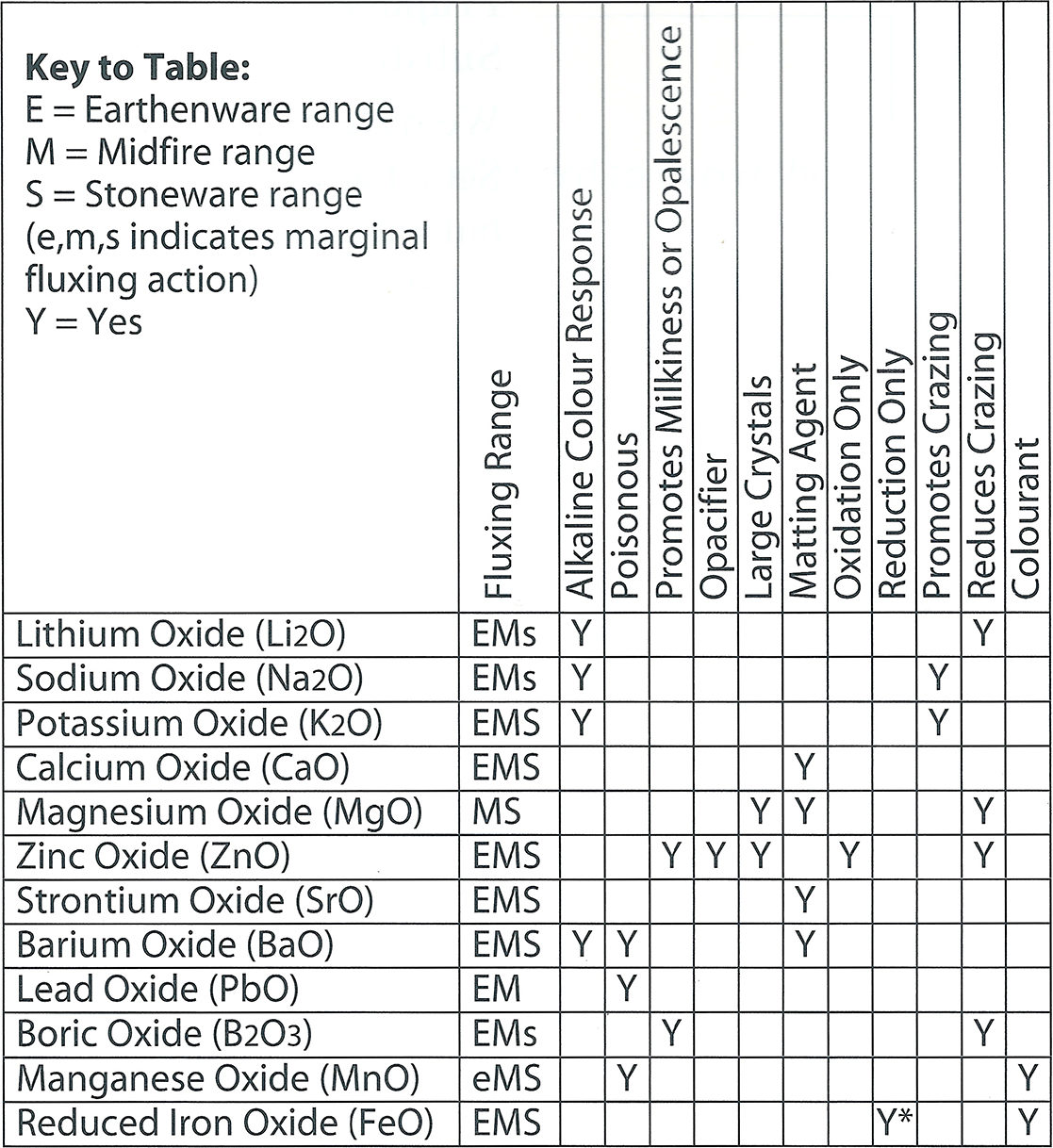
This table lists some of the properties for the main fluxes. Note the inclusion of two not mentioned previously, Manganese oxide (MnO) and reduced iron oxide (FeO). These are normally regarded as “colourants”. Many colouring oxides are fluxes but they are used only in small percentages in the glaze. However iron and manganese are both “weak” colourants and can be introduced in large amounts, large enough for their fluxing action to become important. Iron oxide has a special property - it acts as a flux only in reduction. Zinc oxide on the other hand is wasted in reduction; it changes to the metal and vaporizes, unless already incorporated in a glass or frit.
Proportions of Fluxes - Systematic Substitution
We have already mentioned the 0.7 Limestone Set. The range of possible flux sets is enormous, but we can get a handle on it by starting with this set and changing it. This set has the fluxes: \(0.3 K_{2}O + 0.7 CaO\) (in the Seger formula) and we saw in the Introduction chapter that this is a standard reliable middle-of-the-road set of fluxes for stoneware temperatures.
The first thing to change is the relative proportions of these two fluxes; we can go from one extreme where the only flux is \(K_{2}O\) (potash) to the other where the only flux is \(CaO\) (lime). The recipe for Glaze C in the 0.7 Limestone Set is 70% potash feldspar + 30% whiting. We would vary the proportion of feldspar-to-whiting to go from one extreme to another. The Limestone/Feldspar Series Table (page 46) shows the flux oxides and flux materials in Glaze C for a range of sets. Looking at the top 2 rows of figures, we can see that Glaze C goes from 100% whiting to 100% potash feldspar.
The middle two rows show that the series is divided into equal steps by molecular parts (M.P.) in the Seger formulae. Looking at the other two sets of numbers it is evident that this does not mean equal steps by weight parts. ”Recipe%” and ”Ox. Wt%” are both measures of weight, and they both have big jumps on the whiting end and small on the feldspar end of the table.
Divine Joke
*Table - Limestone/Feldspar Series
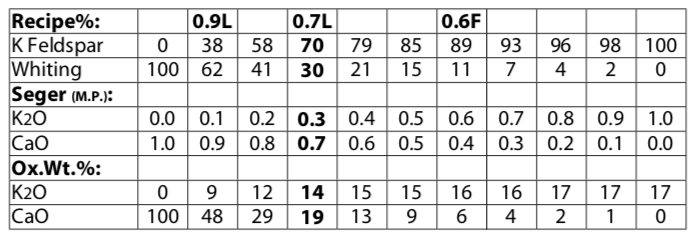
We will study the 0.7 Limestone Set (marked ”0.7L” above) in some detail in the Guided Tour chapter. Students wishing to study this series further could do the 0.9 Limestone Set (”0.9L”) and the 0.6 Feldspar Set (”0.6F”). This gives a reasonable spread.
Looking at the 0.7 Limestone Set, we can begin to introduce other flux oxides. One way to do this is by replacing some of the \(CaO\) with for example \(ZnO\), \(MgO\), \(BaO\), \(SrO\). For example replace 15% of the whiting with 15% of zinc oxide or magnesium carbonate, barium carbonate or strontium carbonate. We can also replace some of the \(K_{2}O\) with \(Na_{2}O\) or \(Li_{2}O\). For example replace potash feldspar with a soda feldspar or nepheline syenite. If introducing lithium carbonate, use maximum 10% in Corner C; on a weight% basis it is a very powerful flux. (In general this method works well substituting fluxes on a weight-for-weight basis, but we can sometimes run into problems. To explore the theory of this we need to move into Seger formula or oxide weight percentage calculation, which is outside the scope of this book.)
Table - Introducing Other Fluxes
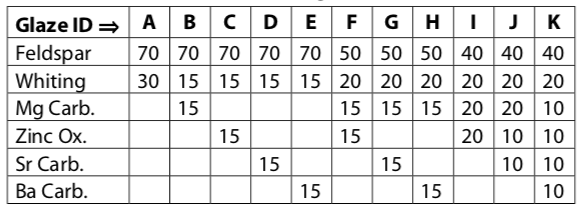
Study this table for a moment to see how we can start with the flux materials in the 0.7 Limestone Set (ID.”A”) and replace the feldspar and whiting with other flux materials - e.g. in “B” to “E” we are replacing half the whiting. The rest illustrate some of the feldspar being replaced as well. As we study this it becomes evident that this represents a very small proportion of the possible combinations; it becomes obvious that the possibilities are almost endless.
We are looking here at a vast landscape of glazes with every conceivable kind of aesthetic and functional real estate. The mind boggles at thinking how to begin exploring the possibilities. We are using here the 0.7 Limestone Sets as a sort of home base to begin our explorations. By exploring the Limestone/Feldspar Series Table we lay down a major thoroughfare through the topography. It took oriental potters hundreds of years to discover and explore, but standing as we do on the shoulders of the old potters, and living in an age of widespread information sharing we can now cover the same area in a couple of weeks. From this we can explore further into the landscape by introducing other fluxes one at a time as illustrated in the table above.
We can choose a safe conventional set of fluxes if we wish or alternatively choose fluxes at random, probably biasing towards high temperature fluxes if firing high, or vice versa if firing earthenware. We should not be afraid to take big risks, especially if we have a group helping and doing lots of sets. It’s quite unusual to get a set that doesn’t do something interesting in the right conditions on the right clay, and the more risk we take the greater the possibility of finding something exciting and new. We should push the boundaries, explore the fringes. But we mustn’t lose sight of our responsibility to use glazes appropriate and safe for whatever use we choose; whenever in doubt, do not use a glaze inside a functional vessel. If necessary read the safety guidelines given in the Appendix.
Remember there is no “right” firing cycle for a given set. A set that seems boring at first might produce brilliant things when we change firing conditions or clay body. The aim is to reveal exciting new glazes and discover important basic glaze principles. The new glazes seem to fall out of almost every set. The illustration of glaze principles emerges as a result of the orderly way the experiment is designed.
Firing Temperature - Choosing an Appropriate Set of Fluxes
It’s possible to come up with some rules of thumb for formulating a set of fluxes for different maturing temperatures. Some of the flux oxides are ineffective at low temperatures (e.g. MgO) and some burn out at high temperature (e.g.PbO).
All these suggestions are for Glaze C recipes, expressed as percentages.
Stoneware: Cone 10 - 12 and higher | High \(R_{2}O\) Series | Medium Series | High \(RO\) Series |
---|---|---|---|
Potash Feldspar | 80 80 | 60 60 | 40 40 |
Whiting (providing CaO) | 20 | 40 20 | 60 40 |
RO Flux Materials containing one or more of MgO*, ZnO, BaO or SrO | 20 | 20 | 20 |
The mid-fire series are similar to the stoneware, but we replace the potash feldspar with nepheline syenite, plus 30 - 60% of frit. Check what is in your frit. For health reasons lead oxide (PbO) has not been included here.
Midfire: Cone 5 - 6 and try firing as high as Cone 10 | High \(R_{2}O\) Series | Medium Series |
---|---|---|
Nepheline Syenite | 40 40 | 30 30 |
Frit** (usually has some CaO) | 40 40 | 30 30 |
Whiting (providing CaO) | 20 | 40 20 |
RO Flux Materials containing one or more of MgO*, ZnO, BaO or SrO | 20 | 20 |
In the earthenware series, notice the similarity between the Frit/RO series and the High R2O Series in the stoneware series.
Earthenware: Cone 06 - 02 and try firing as high as Cone 5 | Frit/RO Series |
---|---|
Frit** (usually has some CaO) | 80 80 |
Whiting (providing CaO) | 20 |
RO Flux Materials containing one or more of MgO***, ZnO, BaO or SrO | 20 |
So basically we are determining the temperature range of the set by deciding the main \(R_{2}O\)-type flux material we use, e.g. feldspar for high temperature, fit for low temperature and with nepheline syenite in between.
3. Family Set
Designing a Set Based on a Particular Glaze Recipe
If we wish to learn more about a favourite glaze we can design a grid set based on the flux materials and colourants/opacifiers it uses. The set will produce variants of the original but will look far beyond the original glaze. For example, the 0.7 Limestone Set is the family set for Mr. nishi’s Standard Cone 9~10 Limestone Glaze. The first step is to work out Glaze C. If this is done correctly we should find the original glaze (or very near to it) included in the grid somewhere. (Note the qualifications outlined in the box.)
To get Glaze C:
First we take the recipe and delete any clays (kaolin, china clay, ball clay etc.) and delete any silica, quartz, flint from the recipe. The remainder (just flux materials plus colourants &/or opacifiers) is Glaze C in a set that should encompass our original glaze somewhere. We can blend up the set in the usual way. We will usually need to convert this Glaze C to a % recipe so we can use the tables or the recipe grid to calculate the other glazes. (If we use the “Calculation Page” at the author’s web site, Glaze C does not have to be expressed as a percentage.)
Example
Original Glaze The following glaze called Periwinkle Blue and attributed to Pete Pinnell was mailed to ClayArt:
1% Lithium Carbonate
20% Strontium Carbonate
60% Nepheline Syenite
10% Ball Clay
9% Flint
+4% Copper Carbonate
+0.15% Cobalt Carbonate
This is an interesting blue glaze. A grid was designed using the set of fluxes and colourants from the glaze.
Producing Glaze C for this set:
Remove the clay (here it’s ball clay*) and the added silica (here it’s called flint) and glaze C is:
1 Lithium Carbonate
20 Strontium Carbonate
60 Nepheline Syenite
+4% Copper Carbonate
+0.15% Cobalt Carbonate
This recipe can be entered into the “Calculation Page” to produce all the recipes, or if we decide to use the Recipe Tables, or the Recipe Grid method, we need to first convert this recipe to percentage figures. Percentage calculation is explained in the Appendix. The percentage version of glaze C here becomes:
1.2% Lithium Carbonate
24.7% Strontium Carbonate
74.1% Nepheline Syenite
+4% Copper Carbonate
+0.15% Cobalt Carbonate
Use this recipe to obtain the 4 Corner Glazes for blending and also any of the glazes that you find interesting. Pete’s original glaze would have been somewhere around No. 27 or 26.
Developing the Set Further
The set above was mostly immature or dry at Cone 6. To get more glazes to mature at midfire temperatures, 10% of frit was added to Glaze C, mostly at the expense of the nepheline syenite. Also lithium carbonate was increased from 1.2% to 2%. Lithium is a powerful flux, and these two changes have caused a significant increase in the number of glazes maturing.
The new Corner C Glaze:
10% Frit 3134
65% Nepheline Syenite
23% Strontium Carbonate
2% Lithium Carbonate
+4% Copper Carbonate
+0.15% Cobalt Carbonate
(See Family Set page in the Guided Tour chapter for a photo of this set.)
4. Random Choice
There is not much to be said for this method which is more of a philosophical than a technical approach to developing glazes. The chances of discovering new and exciting glazes are high, as are the chances of a disappointing set. The suggested maximum values for any flux material in Glaze C should help avoid disasters; see the List of Flux Materials in this Chapter.
4 Working Out the 35 Glaze Recipes
In our examples we will use the “0.7 Limestone Set” presented earlier. The “starting point glaze” for this stoneware set, Glaze C, is:
70% Potash Feldspar 30% Whiting.
Having chosen Glaze C, the recipes for all the other 34 glazes fall into place automatically, because in the standard grid method, the amounts of kaolin and silica in all 35 glazes remain at predetermined values. [For example Glaze A (Glaze No.1) always has 40% of kaolin and zero silica (quartz or flint) in the recipe.]
So having chosen our starting point we need to be able to work out the recipes of the other 34 glazes. There are several easy ways to do this:
- Access the “Calculations Page” at the following web site: http://ian.currie.to/index.html
- Look them up from a set of tables in the back of this book.
- Use the Recipe Grid Table and work out the flux material breakup (if using more than one flux) by simple percentage maths.
- Use Glaze Calculation Software
1. Using the Calculations Page at the web site.
This is the easiest method of getting a printout of all 35 glazes for a set, assuming one is able to access the web page.
Go to the web site: http://ian.currie.to/index.html and click on “Calculations Page” in the Index. Read the instructions there; a summary is given here.
Towards the bottom of the Calculations Page in the row called “1 Name”, insert the words “K Feldspar” under “Flux 1” and “Whiting” under “Flux 2”. Then go to the next line, called “2 Amount” and type “70” under “Flux 1” and “30” under “Flux 2”.
[If we decide the set is to consist of base glazes (with no colouring oxides or opacifiers in the recipes) then rows 3 and 4 are left blank.]
It should look like this after entering the data:

Row “2 Amount”
When reading the instructions at the Calculation Page note the restriction against using decimals in the input figures in Row “2 Amount”. This is simply a limitation of the computer code that calculates the table. If any of our input figures were to have, say, one decimal place, then we should multiply all base glaze figures by 10 before inputting; the input figures here do not have to be expressed as percentages. What matters is that the relative proportions are correct. In the case of the 0.7 limestone set, we could input “7” under “Flux 1” and “3” under “Flux 2” and we would get the same correct list of 35 glaze recipes.
Click on the “Calculate Now” button at row 5 and after a while a new page will appear showing all 35 glaze recipes. The first 12 are shown here:
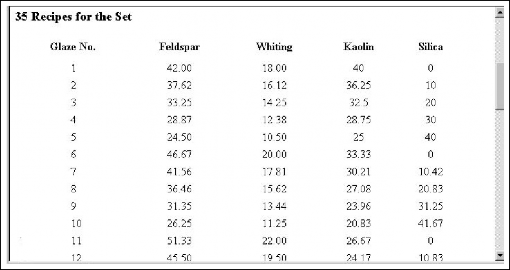
At the bottom there are batch recipes for the four “Corner Glazes”. These are the four glazes used for producing the whole set using the volumetric blending technique. The default batch size is 300 as we use 300 grams of glaze for each corner glaze to produce enough to blend up 48ml each of the 35 glazes. If necessary alter the default and click “Recalculate”.
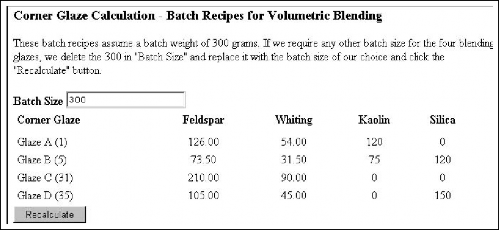
Dealing with Decimals in Row “2 Amount”, and Entering Colourants and opacifiers:
Decimals: If the recipe for Glaze C were: 3.5 Feldspar, 2 Whiting, 1.5 Zinc oxide, we would multiply the numbers by 10 to eliminate the decimals. See the entries in Row “2 Amount” below.
Colourants and Opacifiers: If we are adding colourants or opacifiers to the set, we enter the names into Row “3 Name” and the % addition into Row “4 Percent”. For example, if we want 0.5% addition, we type in 0.5 (don’t include the “%” sign). There is no restriction with entering decimals in Row 4.
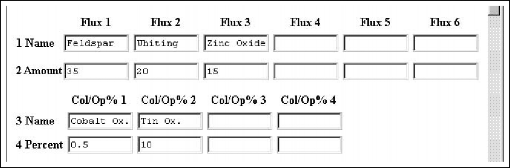
Part of the resulting printout is shown below:
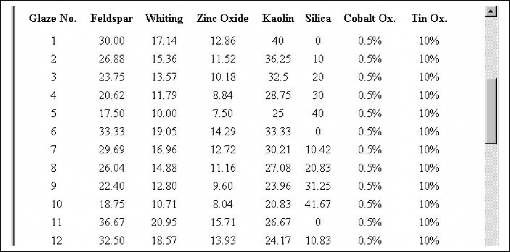
2. Using the Flux Breakup Tables
The Recipe Table opposite is the same data as originally presented in the Standard Recipe Grid (but shown here to two decimal places accuracy). There is only one column for total flux materials. It is unusual for a set to contain only one flux material so we need to be able to calculate the flux material breakup. The method once again hinges on Glaze C (No. 31). For the tables to work, Glaze C must be expressed as % figures. In other words the base glaze must add up to 100. The standard grid method defines Glaze C (our starting point) as consisting of 100% flux materials. In the Recipe Table on the opposite page you can see that Total Flux Materials for Glaze C is 100%:
Glaze No. | Total Flux Materials | Kaolin | Silica |
31 (C) | 100.00 | 0.00 | 0.00 |
In the following set, we have chosen Glaze C to have 2 flux materials (in bold):
Glaze No. | Feldspar | Whiting | Kaolin | Silica |
31 (C) | 70 | 30 | 0.00 | 0.00 |
These percentages, 70 and 30, tell us which columns to look up in the Flux Breakup Tables in the Appendix. (Don’t try to understand this at this stage. Trust me!!) They indicate we should use the 70% column for feldspar and the 30% column for whiting. Repeating: Glaze C base glaze must be expressed in % figures for the tables to work!
The Recipe Table
Glaze No. | Total Flux Materials | Kaolin | Silica |
---|---|---|---|
1 (A) | 60.00 | 40.00 | 0.00 |
2 | 53.75 | 36.25 | 10.00 |
3 | 47.50 | 32.50 | 20.00 |
4 | 41.25 | 28.75 | 30.00 |
5 (B) | 35.00 | 25.00 | 40.00 |
6 | 66.67 | 33.33 | 0.00 |
7 | 59.38 | 30.21 | 10.42 |
8 | 52.08 | 27.08 | 20.83 |
9 | 44.79 | 23.96 | 31.25 |
10 | 37.50 | 20.83 | 41.67 |
11 | 73.33 | 26.67 | 0.00 |
12 | 65.00 | 24.17 | 10.83 |
13 | 56.67 | 21.67 | 21.67 |
14 | 48.33 | 19.17 | 32.50 |
15 | 40.00 | 16.67 | 43.33 |
16 | 80.00 | 20.00 | 0.00 |
17 | 70.63 | 18.13 | 11.25 |
18 | 61.25 | 16.25 | 22.50 |
19 | 51.88 | 14.38 | 33.75 |
20 | 42.50 | 12.50 | 45.00 |
21 | 86.67 | 13.33 | 0.00 |
22 | 76.25 | 12.08 | 11.67 |
23 | 65.83 | 10.83 | 23.33 |
24 | 55.42 | 9.58 | 35.00 |
25 | 45.00 | 8.33 | 46.67 |
26 | 93.33 | 6.67 | 0.00 |
27 | 81.88 | 6.04 | 12.08 |
28 | 70.42 | 5.42 | 24.17 |
29 | 58.96 | 4.79 | 36.25 |
30 | 47.50 | 4.17 | 48.33 |
31 (C) | 100.00 | 0.00 | 0.00 |
32 | 87.50 | 0.00 | 12.50 |
33 | 75.00 | 0.00 | 25.00 |
34 | 62.50 | 0.00 | 37.50 |
35 (D) | 50.00 | 0.00 | 50.00 |
Reading off a Single Glaze:
As an example, let’s take Glaze No. 28 - so far what we have from the Recipe Table is:
Glaze No. | Total Flux Materials | Kaolin | Silica |
---|---|---|---|
28 | 70.42 | 5.42 | 24.17 |
We already have here the figures for kaolin and silica; we just have to work out the breakup of flux materials for this glaze.
We use the Flux Breakup Tables in the back of the book…
Feldspar%: We go to the 70% column in the Flux Breakup Tables and read off the % figure for Glaze No. 28….. = 49.29%
Whiting%: we go to the 30% column in the Flux Breakup Tables and read off the % figure for Glaze No. 28….. = 21.13%
Double Check: Add the two together to make sure they equal the 70.42 (Total Flux Materials for Glaze 28)….. 49.29% + 21.13% = 70.42%
Compiling a Full Set of 35 Recipes:
The easiest way to understand the use of the flux breakup tables is to prepare a full table of 35 recipes for a set.
One advantage of setting out the 35 glazes in a table (rather than the grid format) is that we can easily use a photocopier
to prepare a list of all the glazes in the set. We can simply photocopy the 70% column (and call it Feldspar), and
the 30% column (and call it Whiting). Then copy the Kaolin and Silica columns from the Recipe Table, cut them out and
paste them all down to give a set as follows:
Cut and Paste a Table of Recipes for a Set Glaze C: 70%Feldspar + 30% Whiting
70% | 30% | |||
---|---|---|---|---|
Glaze No. | Feldspar | Whiting | Kaolin | Silica |
1 (A) | 42.00 | 18.00 | 40.00 | 0.00 |
2 | 37.63 | 16.13 | 36.25 | 10.00 |
3 | 33.25 | 14.25 | 32.50 | 20.00 |
4 | 28.88 | 12.38 | 28.75 | 30.00 |
5 (B) | 24.50 | 10.50 | 25.00 | 40.00 |
6 | 46.67 | 20.00 | 33.33 | 0.00 |
7 | 41.56 | 17.81 | 30.21 | 10.42 |
8 | 36.46 | 15.63 | 27.08 | 20.83 |
9 | 31.35 | 13.44 | 23.96 | 31.25 |
10 | 26.25 | 11.25 | 20.83 | 41.67 |
11 | 51.33 | 22.00 | 26.67 | 0.00 |
12 | 45.50 | 19.50 | 24.17 | 10.83 |
13 | 39.67 | 17.00 | 21.67 | 21.67 |
14 | 33.83 | 14.50 | 19.17 | 32.50 |
15 | 28.00 | 12.00 | 16.67 | 43.33 |
16 | 56.00 | 24.00 | 20.00 | 0.00 |
17 | 49.44 | 21.19 | 18.13 | 11.25 |
18 | 42.88 | 18.38 | 16.25 | 22.50 |
19 | 36.31 | 15.56 | 14.38 | 33.75 |
20 | 29.75 | 12.75 | 12.50 | 45.00 |
21 | 60.67 | 26.00 | 13.33 | 0.00 |
22 | 53.38 | 22.88 | 12.08 | 11.67 |
23 | 46.08 | 19.75 | 10.83 | 23.33 |
24 | 38.79 | 16.63 | 9.58 | 35.00 |
25 | 31.50 | 13.50 | 8.33 | 46.67 |
26 | 65.33 | 28.00 | 6.67 | 0.00 |
27 | 57.31 | 24.56 | 6.04 | 12.08 |
28 | 49.29 | 21.13 | 5.42 | 24.17 |
29 | 41.27 | 17.69 | 4.79 | 36.25 |
30 | 33.25 | 14.25 | 4.17 | 48.33 |
31 (C) | 70.00 | 30.00 | 0.00 | 0.00 |
32 | 61.25 | 26.25 | 0.00 | 12.50 |
33 | 52.50 | 22.50 | 0.00 | 25.00 |
34 | 43.75 | 18.75 | 0.00 | 37.50 |
35 (D) | 35.00 | 15.00 | 0.00 | 50.00 |
3. Using the Recipe Grid Diagram.
A simple calculation can work out the flux breakup from the Recipe Grid diagram shown on Page 32.
Worked example for Glaze No. 19:
The recipe is reproduced here, and it contains a total of 52% combined flux materials (“Fl.Mtl.”). The key to the breakup is Glaze 31 (Glaze C). We know the breakup there because we decided that ourselves. Remember that “choosing Glaze C” is the first decision we have to make when designing a standard grid experiment. Again we will use the 0.7 Limestone Set where Glaze C is:
70% Feldspar
30% Whiting
So the proportions of the two fluxes are 70 of feldspar to 30 of whiting. This proportion remains the same across the set of 35 glazes, so it can be used to work out the breakup of the 52% combined flux materials in Glaze No. 19.
Feldspar in Glaze 19…
= 52% X 70%
= 0.52 X 70%
= 36.4% Feldspar
Whiting in Glaze 19…
= 52% X 30%
= 0.52 X 30%
= 15.6% Whiting
Double-check the calculation by adding the two percentages to make sure they equal the original combined flux material % for Glaze 19:
36.4% + 15.6% = 52%
4. Glaze Calculation Software
The grid method outlined in this book is now widely recognized and is included in several glaze-calculation software packages. Both those listed below provide the ability to calculate the 35 recipes from Glaze C.
Matrix Glaze Calculation Software:
“Matrix is a glaze calculation software package available for both PC and Macintosh computers. The application was developed at the School of Art, Otago Polytechnic, Dunedin New Zealand, and has many unique, user-friendly features. Both versions have the capacity to generate line, triaxial and biaxial (and quadraxial) blends producing a worksheet which enables the mixing of the blends using volumetric techniques as described in Ian Currie’s approach to glaze research. Blends can be designed from unity formulae or from recipes and can be created in a variety of sample sizes. In the PC version you can automatically generate a Standard Recipe Grid after entering and saving on disc the original base glaze.”*
Matrix is the product of Lawrence Ewing
21 Slant St, Careys Bay, Dunedin,
NEW ZEALAND
lewing@clear.net.nz
Extensive and detailed information about Matrix may be viewed on line at
http://www.Matrix2000.co.nz
This site also contains an online interactive instructional package on glaze chemistry called GlazeTeach and has tutorials to help new users of Matrix.
Matrix is supplied to PC owners on a CD which includes GlazeTeach and Matrix Tutorials.
Glaze Chem
*“GlazeChem is a general-purpose glaze database and calculation program for P.C’s . It includes Currie recipe blending among its many glaze testing and mixing options. Starting from any glaze, you can generate a set of glazes based on his recipe-grid method with only a few mouse clicks.
GlazeChem includes features for modifying Currie’s “standard” recipe-grid method - more or less grid points, different clay/silica proportions in the corners, and your choice of materials along each axis. The program also includes graphing features that (for example) let you plot your original glaze against the grid glazes on a graph of Al2O3 vs. SiO2.”*
It is a shareware program available from the author Robert J. Wilt. It may be downloaded from the following Web site http://www.dinoclay.com/
5 A Guided Tour
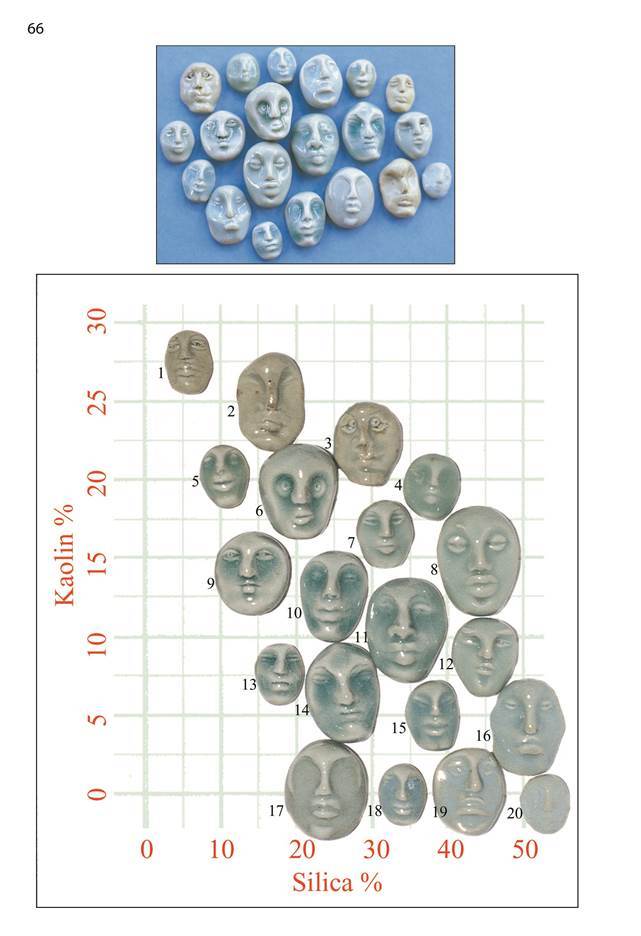
Isolating Variables
The page opposite shows two photographs of the same set of glaze samples. If we are provided with all the recipes and details of the clay body, firing etc. then a competent potter could reproduce the glazes. But looking at the first photograph where the heads have been jumbled at random, we really can’t make much sense of why the glazes are different. Looking closely at the recipes we will find the glazes are very similar; they all have the same amount of black iron oxide (1%) and if we bothered to do the calculations we’d find they all have feldspar and whiting in the ratio of 7 to 3. The only thing varying is the amount of kaolin and silica in the recipe. This is interesting, but is not much help until we rearrange the heads as in the second photograph, placing them in their correct positions on the kaolin/slica graph.
Suddenly we can see trends and zones of similarity, and we can come to conclusions regarding cause and effect. In this case we can reach some conclusions about the role of kaolin and silica in celadon glazes.
We can see that high kaolin celadons can develop a brown or greyish tinge, high silica can cause opalescence and eventually opacity. We can see how to manipulate crazing and bubble size and density. Although it’s not obvious on the photograph, we can easily determine trends in melting point and glaze stiffness or runniness. The interesting question to ask is “Where did all this extra knowledge come from?” All the glaze recipes and other information necessary to reproduce the glazes was provided, but only now we can start to reach conclusions about glaze principles.
It comes from the order we put into the experiment. In particular it comes from isolating variables, in this case kaolin and silica, and displaying them appropriately. Looking across the graph from left to right the only variable is added silica. Going from bottom to top the variable is kaolin.
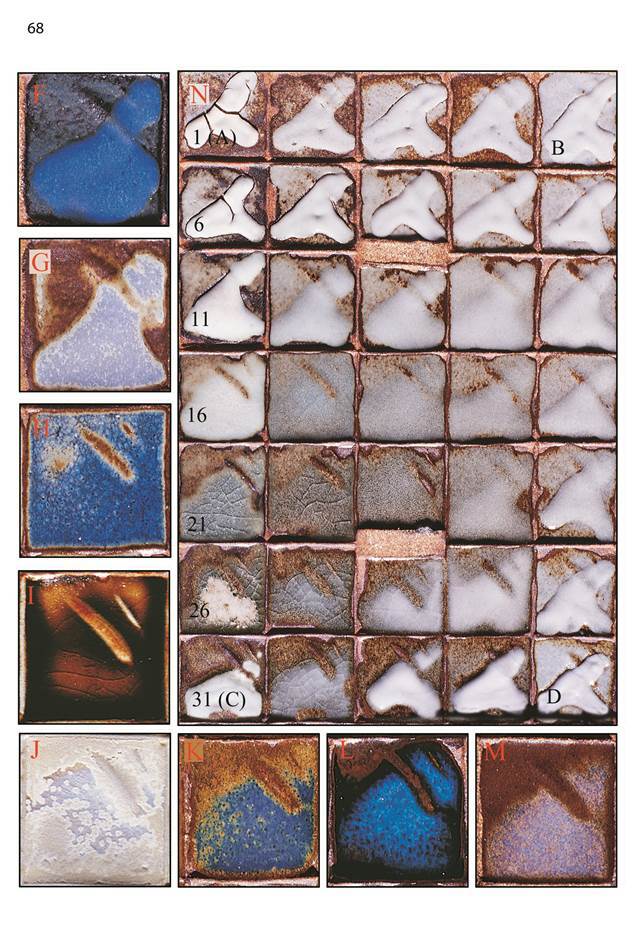
Standard Limestone Set (The 0.7 Limestone Set)
All the glazes of the opposite page have the same set of stoneware flux materials, namely feldspar and whiting in the ratio of 7 to 3. The enormous range of qualities is the result of varing additions of kaolin and silica and also two colourants and one opacifier. This set of glazes was first mentioned in the book Introduction and is used throughout as a standard or reference set. For anyone wishing to come to grips with glaze principles it is an excellent place to start. The stoneware set is the “standard” set, but similar sets are offered on page 99 for midfire and earthenware temperatures.
The Starting Point Glaze (No. 31) for the 0.7 Limestone Set is:
70% Potash feldspar
30% Whiting
This is the recipe for Corner C for this set. The rest of the set of 35 recipes can be obtained by adding kaolin and/or silica to this glaze.
Glaze No. 18 - This glaze right in the middle of the set is almost identical in composition to the standard limestone glaze used by Mr.Onishi as his reference glaze. (See page 15) At cone 10 this is a stable, stiff (non- runny), reasonable transparent and shiny glaze free of crystals. On most stoneware bodies it is uncrazed. By today’s standards it is a fairly uninteresting glaze unless we add colourants or opacifiers. It is however a stable and reliable glaze.
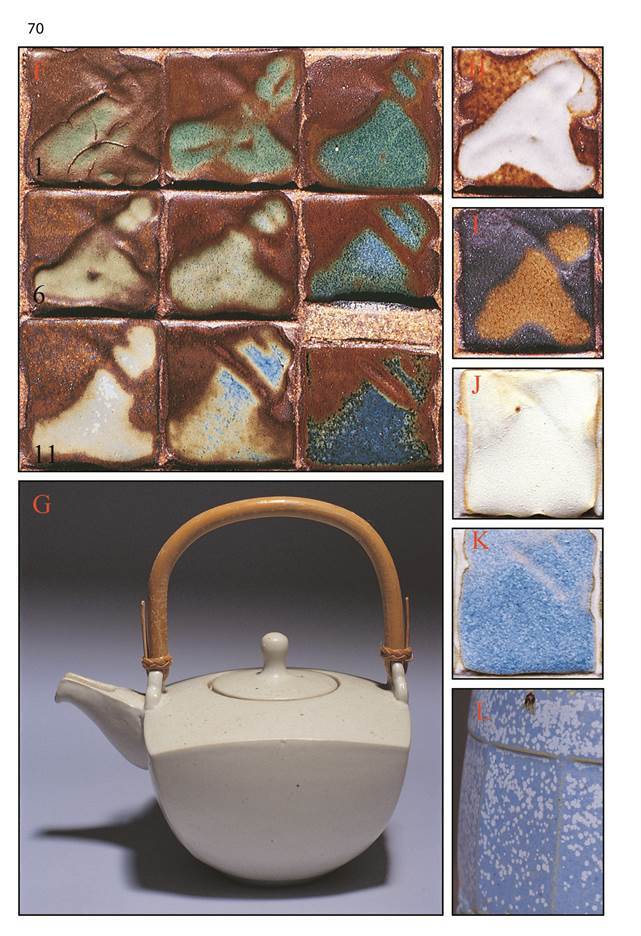
Corner A - High Alumina
The high alumina corner at stoneware or midfire is typified by dry or matt glazes that are semi-opaque or opaque. They are stiff and the high kaolin content often causes the glazes to crawl unless some or all of it is calcined. Over a dark body, these glazes usually exhibit colour- break (colour changing sharply) where glaze thickness varies. They are often uncrazed.
If most of the glazes in a grid tile are mature (properly melted), then moving from the middle of the grid towards A we move from shiny to matt glazes, passing through a zone of semi-matt that will often have subtle and rich surface qualities. The teapot on page 91 illustrates such a glaze.
At earthenware temperatures matured alumina matts usually don’t develop. Dry matts are possible however.
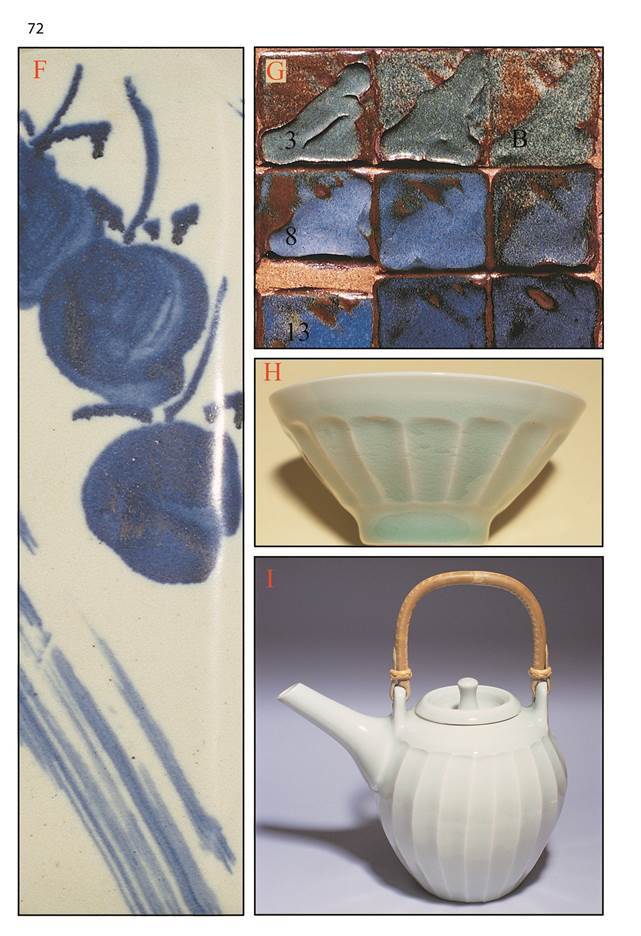
When a grid tile is fired high enough, there is often a zone of shiny transparent glazes extending from C diagonally to B. This table outlines some of the differences between B-corner and C-corner glazes:
B Low Flux | C High Flux | |
Melting Point | High | Low |
Firing Range | Wide | Narrow |
Runniness | Stiff | Runny |
Pigments | Stable | Unstable |
Crystals grow | No | Yes |
Crazing | Less | More |
Durability | Strong | Weak |
Reaction with body | Normal | V. reactive |
Corner B - Low Flux
The low flux (high alumina / high silica) corner is typified by stiff, stable, semi-opaque slightly immature glazes that are uncrazed. They mature if fired high enough, and become transparent (assuming no opacifying additions) and shiny. The stiffness and stability make them good for use with colouring oxide application where it is desirable that the colourant not move or flow.
The diagonal zone between corner B and glaze no.18 (the middle of the set) is good for choosing a stable uncrazed liner glaze that is reasonably resistant to chipping and scratching (depending on glaze fit). This area is in fact the source of many strong, stable and dependable commercial glazes. The downside is that the glazes can be somewhat lacklustre, or not so interesting. As in so many things, there is a tradeoff between dependable and exciting!
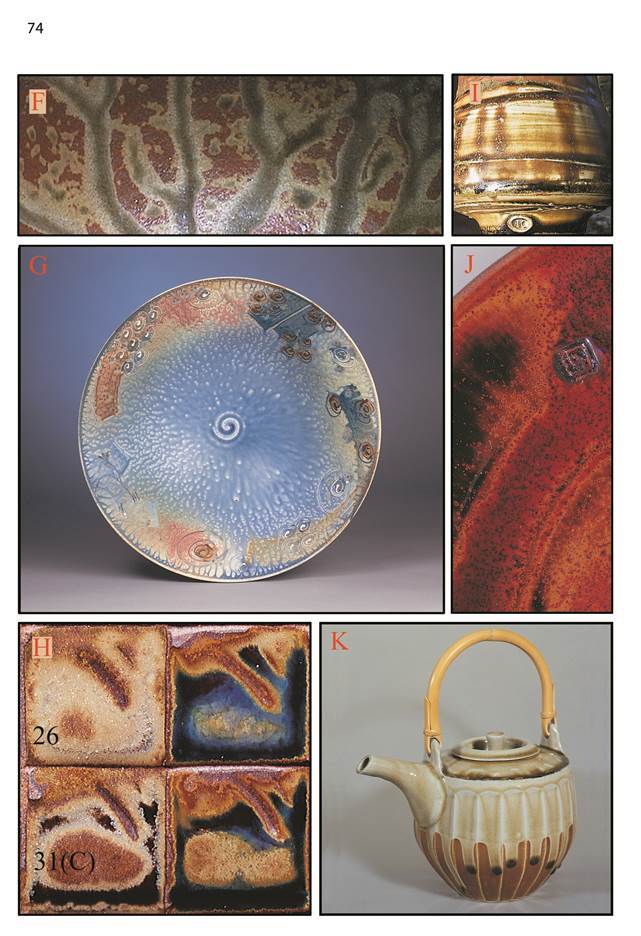
Corner C - High Flux
The high flux glazes are in many respects the opposite of corner B. (See the comparative table on page 73.) They are very runny once they have melted, are crazed, soft (easily chipped or scratched) and applied colouring oxides flow and diffuse away. In extreme cases they are water- soluble. They often develop “stringing” or “webbing”. They are highly sensitive, mobile glazes that often develop crystals, unusual colour responses from colourants and often provide very interesting effects.
Soda Glazing and salt glazing will convert many glazes into a “Corner C” type exhibiting high- flux characteristics. (See J). Also, C-corner glazes will often flash or thinly glaze the surrounding bare clay with volatile fluxes like soda, lithium, barium etc. evaporating from the applied glaze during the firing.
One might imagine that glaze 31 would always melt first. After all it does contain maximum flux material, and the fluxes are there to facilitate melting. Paradoxically many of the flux materials have very high melting points and are themselves “fluxed” by alumina and silica. Glaze 31 (C) will be first to melt only if it contains enough low melting flux material, such as a frit. However it will melt well before the other corners.
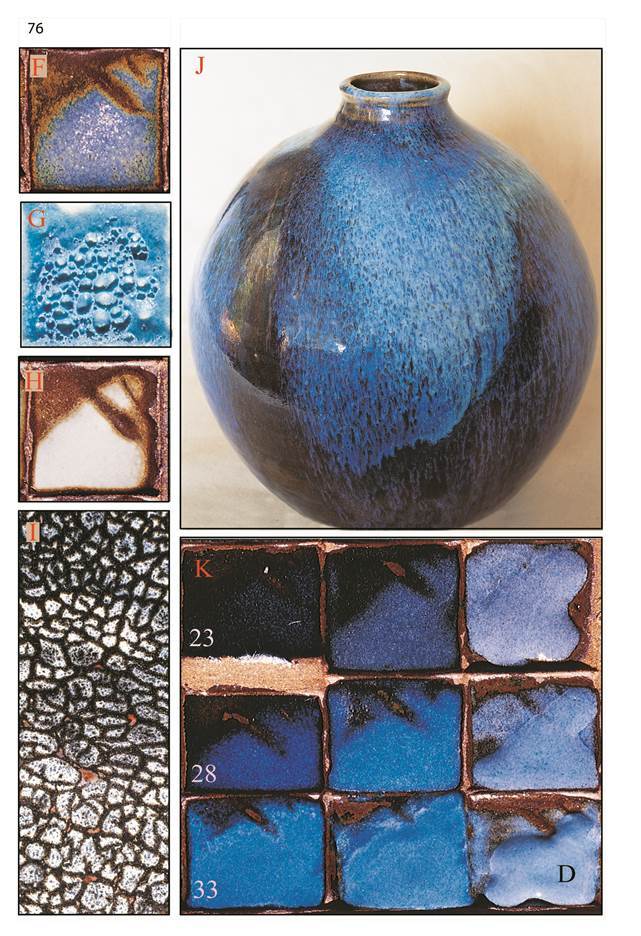
Corner D - High Silica
There is normally a transition from underfired glaze right at D through to shiny transparent glazes towards the middle of the grid. This is evident in K opposite. (Note: 23 is a very dark transparent glass.) Next to D is a zone of opaque glazes, white in the absence of colourants. They may have a shiny sugary surface. Between the opaque zone and the transparent is sometimes a zone of opalescent blue glazes, e.g. 28 in K. In high fired reduced glazes these are helped by titanium (on page 87 compare tiles H and I) and iron oxide. The iron can be from the body, or a slip or glaze underneath. In lower fired oxidised glazes zinc and boric oxide help to produce a milky opalescence; on page 87 see tile F, glaze 21. (At lower temperatures the effect is not necessarily near D; the pattern of zones is not as consistent. However these glazes are still apparently a transition between the higher-silica opaque and the transparent glazes.) Here the addition of titanium (page 87 tile G) added to the zinc and boric oxides opacifies most of the glazes pushing the opalescent zone right across to the upper left.
High frit/high silica glazes often bubble and fail to smooth over. The bubbles can be smoothed with a grinding stone and/or abrasive paper. This sort of glaze is usually not very stable. Don’t use them inside functional pots. See G.
The lizard skin texture in I is usually associated with A-corner glazes high in raw clay, however diatomite shrinks like a clay, so it can be used to achieve this effect in the D-corner. Here the silica in a chun-glaze recipe has been replaced by diatomite. There is some difficulty getting it to stick on a vertical surface.
Increasing silica in the glaze usually (not always) decreases crazing.
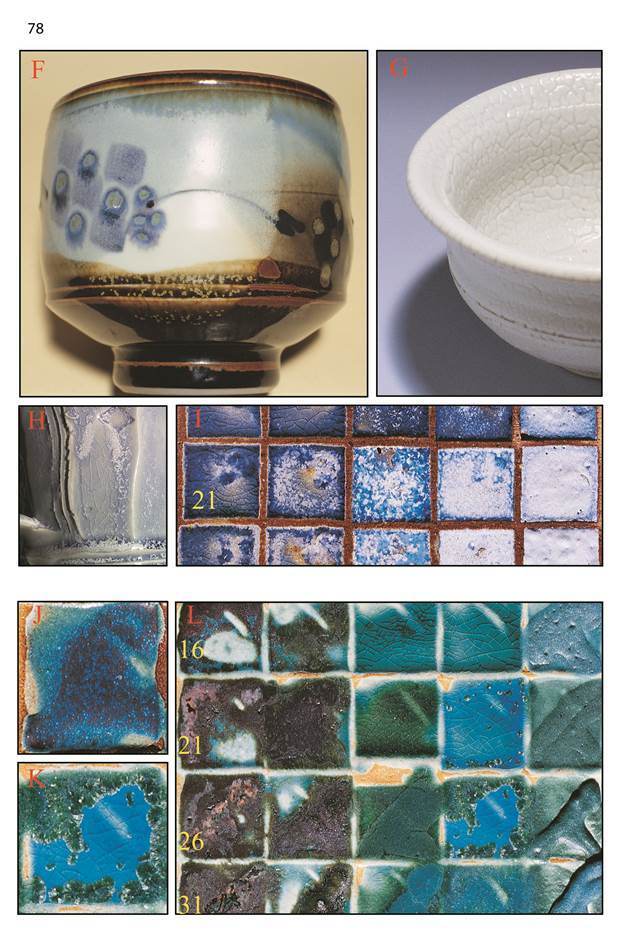
Magnesia Glazes
The white glaze on Craig Martell’s cup (F) displays several of the typical characteristics of magnesia glazes: 1. A beautiful satin matt surface. 2. A lilac colour with cobalt pigment (small squares to the left) 3. yellow “teadust” crystals with iron oxide (on the bottom where it mingles with the black tenmoku glaze). These three things are caused by the production of pyroxene crystals, which are favoured by medium-to-low alumina and medium-to-high silica, so high silica matts are possible. High alumina magnesia matts work too, but tend to easily go shiny and craze if overfired.
Light magnesium carbonate causes crawling if used in excess (see G). This crawling does heal over more or less with higher firing (unlike the crawling caused by for example colloidal zinc oxide).
I: The dramatic development of pyroxene crystals on this sample is probably caused by a combinatinon of slow cooling and the choice of clay. Some rough clays seem to promote large pyroxene crystals in magnesia glazes.
Substituting magnesia (from talc, magnesium carbonate or dolomite) for some other fluxes can reduce crazing.
Strontium Glazes
A relatively recent addition to popular use, strontium is sometimes dismissed as similar to lime or barium. Most fluxes can be substituted at times with little change to the glaze, but to get the big picture, the grid method is hard to beat. The segment shown in L shows some interesting features, including some reliable macro-crystals in 24 and 29, turquoise in many of the glazes (an alkaline colour from the copper) and an interesting overload in the low silica zone (A to C) from the copper. There is no matting on the high silica side, only a sharp transition from shiny to underfired. Some of these characteristics are similar to barium, but a grid tile substituting barium for strontium is quite different.
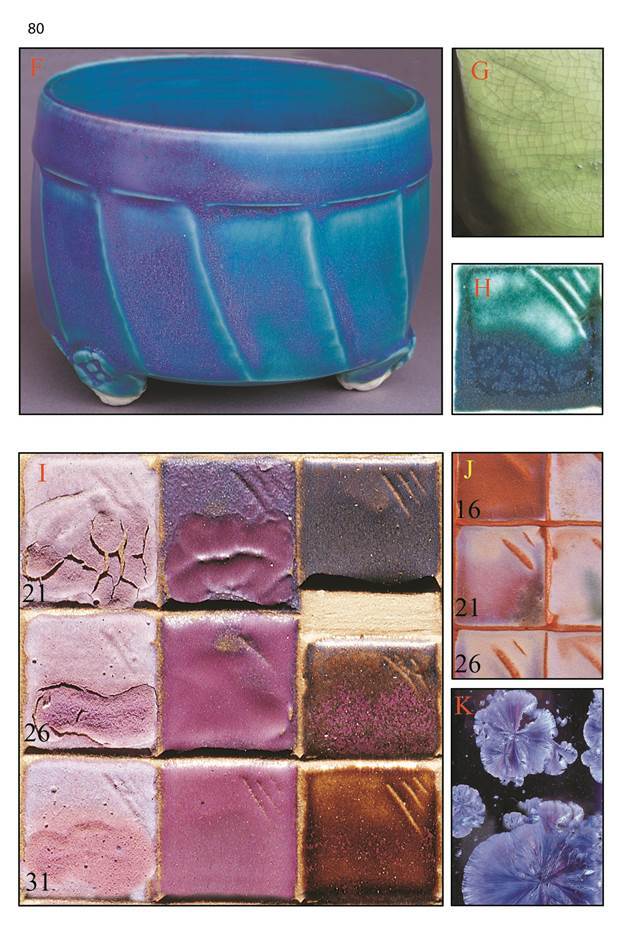
Barium Glazes
Barium carbonate produces excellent matt glazes in the low silica zone of the grid (corner A to corner C). The mattness persists even when the glazes are overfired and runny (c.f. magnesia).
Barium promotes alkaline colours such as turquoise or other blues from copper (see F and H), and pale apple greens with a small amount of chrome oxide (G).
In combination with zinc, pinks and blues are possible with nickel oxide (see I).
Zinc Glazes
Zinc oxide (ZnO) is lost from reduced glazes. (See Hamer.) It should be possible to use zinc as a flux in reduction if it is already incorporated into a glass such as a frit.
As well as being a flux, ZnO is an opacifier, or if the opacifying particles are small enough it gives rise to milkiness and opalescence (see J).
Zinc oxide in low alumina glazes will produce large fan- shaped crystals if the glaze is adequately matured and slowly cooled (K).
Zinc oxide tends to reduce crazing. It also tends to change many matt glazes to shiny.
Feldspathic Glazes
If the flux materials are high in feldspathic ingredients then the glaze is necessarily high in alumina and silica (see the diagram on page 149). They are therefore fairly stiff at normal stoneware temperatures. A standard grid using 100% feldspar or nepheline syenite as our starting point will have stiff glazes in corner C and they get stiffer and drier as we move away from there. We will probably find little change from cell to cell on the grid. (We could adequately sample the grid omitting every second row, leaving 12 glazes.)
On normal stoneware clays the glazes are usually crazed because of the high soda and/or potash, and in spite of the high alumina and silica.
Guan (Kuan) are traditional Chinese glazes high in feldspathic material. F and G belong in this family. See also the discussion and photo by Steve Harrison on Page 88, 89.
There are a large range of shino-type glazes possible, depending on materials, body (or under-slips) and firing. H is based on nepheline syenite, J on soda feldspar. A relatively new extension of the theme has emerged replacing some of these materials with lithium materials and soda ash to produce so- called “carbon trap” shinos. [See “Revival Fires: Another Face for Shino” by Jim Robinson - Studio Potter, Volume 21, #1, December 1992, for a comprehensive discussion.]
There are some unusual colour responses, see I and K on the opposite page. The cobalt green in K however is not confined to high feldspar glazes. See for example the top row in photo F on page 70; this is based on the standard limestone set. The green colour requires cobalt and titania (titanium dioxide) in a high alumina glaze; a feldspathic base helps, as does barium carbonate.
Traditional oilspot tenmoku glazes have a high- feldspathic base.
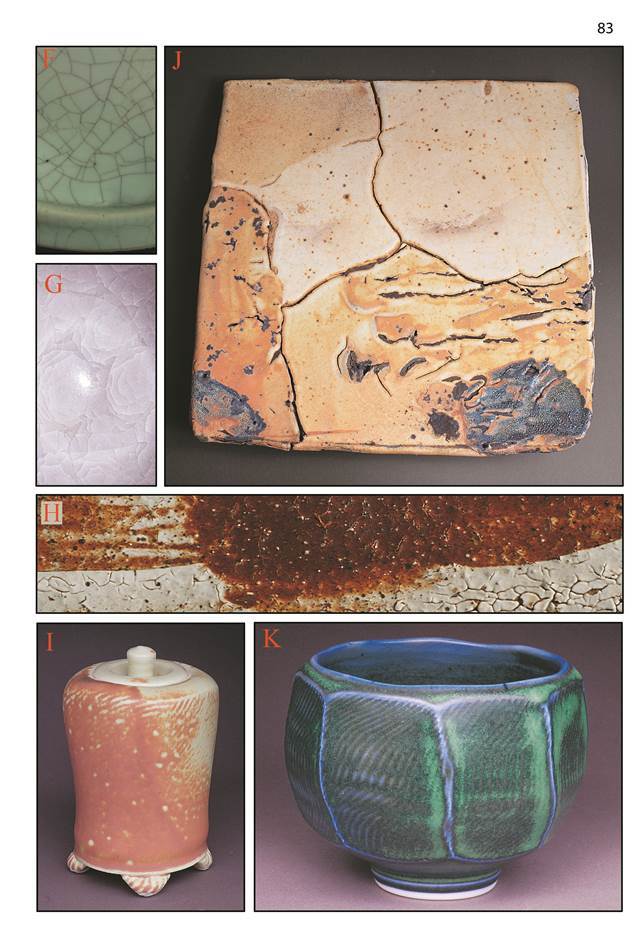
Alkaline Glazes
These glazes are rich in the alkaline fluxes: soda, potash, lithium oxide and barium oxide. They are usually also low in alumina (cf. feldspathic glazes, previous page); increasing alumina decreases the “alkaline” characteristics (e.g. colour). See also in Hamer’s Dictionary*.
Alkaline Frit Glazes - alkaline colours often occur if a colouring oxide is added to a low melting point frit. This alone is usually too runny and soft to be much use, but we can add kaolin and silica to stiffen the glaze up. Excess kaolin addition will change the colour towards a more “normal” colour response. The addition of silica will usually maintain the alkaline colour and eventually produce coarsely bubbled glazes around Corner D that can be ground back to produce a crater glaze (see G on page 76, 77). High frit alkaline glazes are usually used at low temperature (earthenware or midfire) and in oxidation. One can develop a palette of different colours that run together nicely once the glazes start to move (see the teapot in H)
One of the “gradients” that we can explore is transparent to opaque colour. If we use a lot of high sodatrit such as Ferro frit 3110(=4110) we get transparent heavily crazed glazes such as in the narrow tiles in G. On the other hand a high B2O2 frit such as Ferro 3134 (= 4108, or 4508) will produce milky opacity with colourants, especially where thin, simmilar to the platter in F. Note the transparent darker colour where thick. It is possible to blend frits to fine-tune these two properties.Obtain analyses of the frits available from your supplier and compare the relative amounts of the 12 base glaze oxides (see page 12). This will guide you in your choice
High Barium Glazes - For higher firing, alkaline glazes with matt surfaces can be achieved by the use of barium carbonate. In this case low alumina is not necessary.
Alkaline Colour - typical alkaline colour responses are illustrated on the opposite page: copper pigment (Cu) giving blue (turquoise), iron (Fe) giving yellow, manganese (Mn) purple, Chrome (Cr) in small amounts can give a soft apple green. Cobalt (Co) gives a brilliant blue here, but can give pinks in some alkaline glazes.
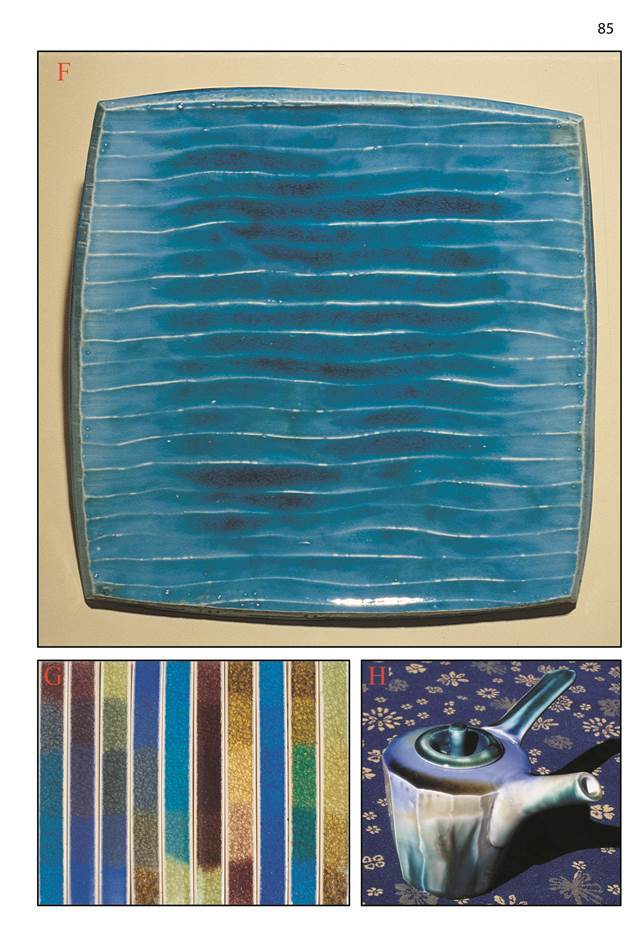
Volumetric Addition
If we take all the glazes in tile F (opposite) and add 5% titanium dioxide (TiO2) to each, we get tile G. Rather than make up a whole new set, we can use volumetric addition to produce the second set from the first with very little extra effort. This method is detailed in Chapter 7.
For a given pair (opposite page), the only difference is the addition; the base glazes are identical, the clay body is identical and the two tiles were fired in a stack near each other, so the firing is also identical. This means we can compare say, glaze 21 with glaze 21 in the other set, and know that any observable difference is caused by the TiO2 alone. This elimination of extraneous variables often throws up surprising results. For example if we compare glaze C in tiles H and I, even in the photograph we can detect a dramatic difference in fluidity. The TiO2 is strongly fluxing the glaze! This is unexpected, and suggests the existence of a nearby eutectic* with TiO2.
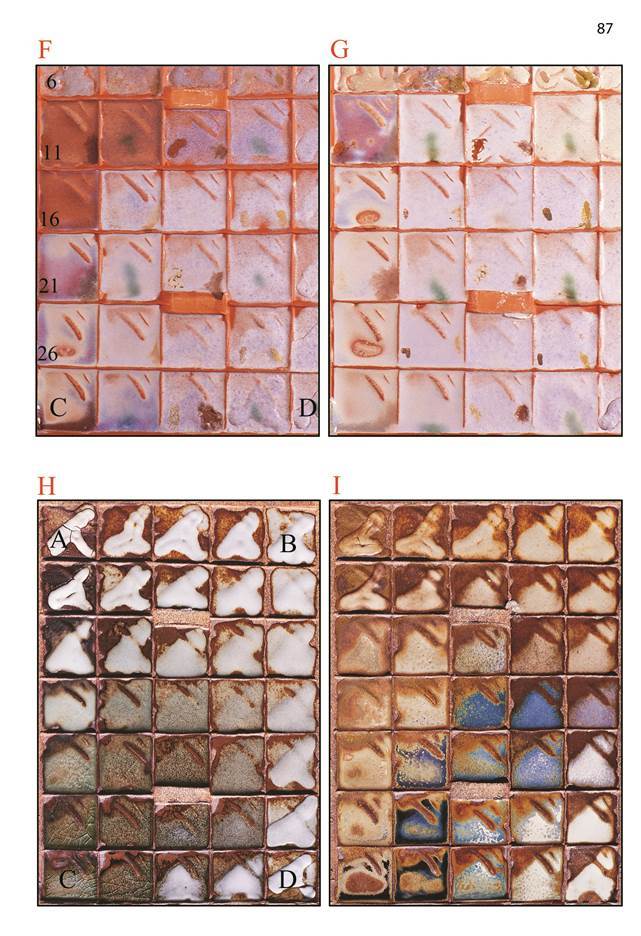
Clay Body and Firing
The firing and the clay body often have more impact on glaze quality than the glaze recipe itself. The grid method helps the study of these vital variables by facilitating easy production of “clones”, applying the same set of glazes to several grid tiles using more than one clay body. (Read also the box on page 105.) Close study of pairs of grid tiles fired under different conditions, or on different clays, will provide insights to important glaze principles.
Varying the Firing:
F and G (opposite) show the same glazes on the same clay body. Firing variables were as close as possible, with the exception of maturing temperature. F was fired tocone10,Gtocone12. Atcone10manyofthe glazes look very similar - opaque and semi-matt. The 10% of titanium dioxide is acting here as an opacifier and matting agent in most of the glazes. When the firing is elevated to cone 12 suddenly the extra heat has caused the titanium dioxide to act as an agent of diversity rather than uniformity. Now we see a diagonal band across the set starts to clear up (along the eutectic trough) giving a beautifully varied series of glazes showing changes in opacity, opalescence, shininess and textural breakup. Holding the two grid tiles side by side we see at a glance how the firing has brought these glazes to life.
Varying the Clay Body:
Grid tiles H and I are identical sets of glazes fired side by side on different clay bodies. Comparing the pairs of individual glazes we would be excused for thinking they are completely different, where in fact they are exactly the same glaze.
Interfaces
Another subtle lesson here is the importance of thresholds or interfaces or the marginal region between two different states. In tile G we’ve reached a state where some are starting to move from opaque to opalescent or transparent, and small changes in alumina and silica are causing big changes as we move from glaze to glaze, or even within the same glaze as we vary thickness. Similarly in H and I we can see how the use of a dark body can cause interesting colour changes with glaze thickness. The iron in the body is bleeding through and even where it is thick the glaze is often a completely different colour; where the glaze is thin it is changed utterly, breaking to a different colour.
This illustrates the trade-off between the responsive and the foolproof. Commercial glazes rarely have this sort of life in them, because commerce needs reliability. To express ourselves we need a responsive medium - one that responds to our smallest inputs! It is the very antithesis of foolproof. The use of “foolproof” materials and processes leads to a boring uniformity and can disempower the artist.
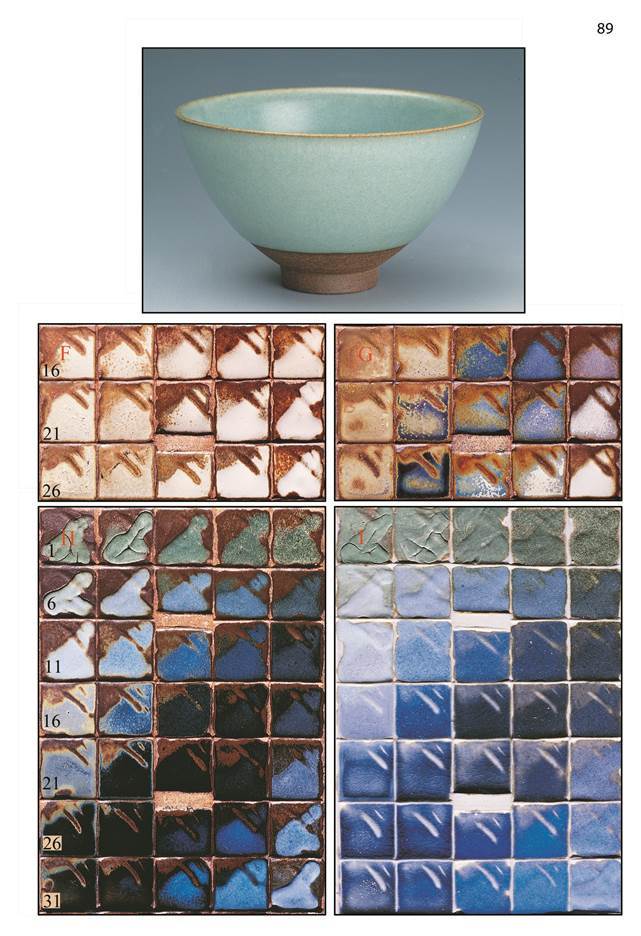
Using the Grid
There is more to studying glazes than the grid method! However the systematic variation of fluxes alumina and silica gives deep insights into the nature of glazes, and often it takes us to what we seek in one step.
The glaze on the teapot opposite came out of the very first alumina/silica grid experiment I performed. I had been seeking such subtle surfaces for some time believing some secret ingredient was involved. However all it required was just the right balance of kaolin and silica with feldspar and whiting. We’ve moved on a bit since then, but the principle is as effective as it ever was: when we go fishing for beautiful new glazes we really are searching blind, and a blind angler should use a net rather than a spear!
The use of the “net” or the grid enables… - the location of sensitive marginal phenomena such as opalescence, special surface, colour break, crystal formation etc. - the manifestation of the chosen variable - the variable and its range of effects is laid out in front of us to see. - the following of phenomena as they move across the grid with change of temperature, firing rate, material purity, etc. See for example how the blue opalescence in F (opposite page) moves to the right with the more intense firing in G - the quality in 28 moves at least to 29, and probably down a bit as well. - the adjustment of recipe to maintain glaze properties as materials change. This applies especially where the main change is variation in alumina and /or silica - a common problem with kaolins and feldspars. - the comparison of glazes a set at a time rather than one by one; if we use “standard” grid sets we can comprehend and compare the data in sets of glazes just by comparing the C-recipes. This is because when using standard grids the kaolin and silica percentages in the 35 glazes remain consistent from set to set. Therefore the one glaze (C) describes the whole set. Surfaces similar to the one on the teapot occur in many types of glazes at midfire and stoneware temperatures. With the help of the grid they are easily found. (They are more difficult at earthenware.) This glaze was found between the middle of the set and Corner A. Assuming the set is fired high enough, we will usually pass from a clear shiny glaze at number 18 through to full matt glazes around A. We can usually locate one or more candidates for these beautiful surfaces in the transition zone between shiny and matt. We can fine-tune the surface by adjusting firing temperature and cooling rate or by interpolating between the glazes on the fired grid tile.
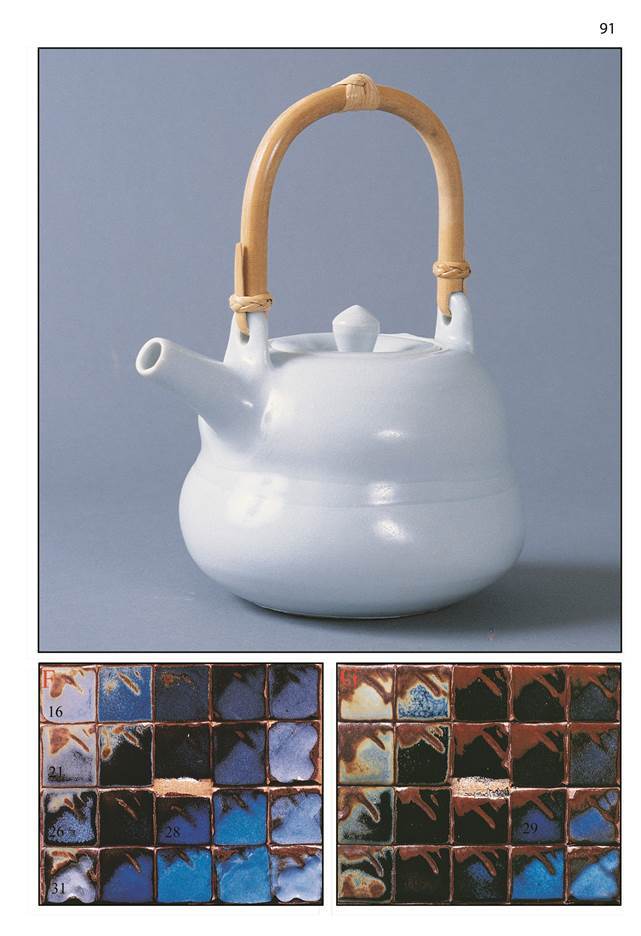
Family Set
We can take any glaze and make a standard grid around it, thereby producing a set of 35 glazes with the same set of fluxes and colourants/opacifiers, but varying alumina and silica. The set here is an example based originally on a midfire glaze attributed to Pete Pinnell.
The photograph shows a family of glazes closely related to the original, illustrating the sort of variation we can expect moving around the grid. We also have many interesting glazes that are quite different from the original; the extent of the standard grid usually takes us well beyond any single glaze type.
The evolution of this set is detailed in Chapter 3; see page 50 “Family Set - Designing a Set Based on a Particular Glaze Recipe”.
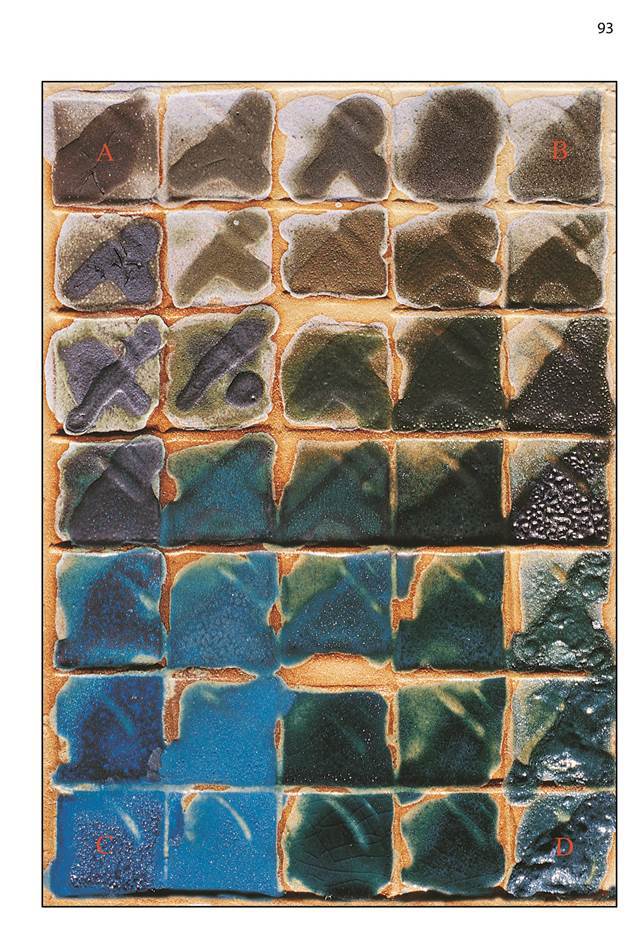
Photographs
F: Corner C* is as follows: 27 Nepheline syenite 27 Whiting 11 Talc 35 Bone ash Fired to Cone 12, reduction. Red stoneware clay.
G and H: Teapots by the author. | 13.5 | Nepheline syenite | | 13.5 | Whiting | | 5.5 | Talc | | 23.1 | Ferro frit 3134 | | 17.5 | Bone ash | | 18.6 | Kaolin | | 8.3 | Silica | | +2% | Cobalt carbonate | | +6% | Titanium dioxide |
With G and H the glaze is applied over a wash of iron oxide slip. (The clay is white stoneware, which does not obtain much response from the glaze) and they were fired in reduction to cone 10
I: Plate by Hank Murrow. Glazed with the original “Cory’s Weird”, developed in 1971 by Cory Levins:
| 32 | Nepheline Syenite |
| 3 | Whiting |
| 32 | Bone Ash |
| 13 | Talc |
| 18 | Kaolin |
| 2 | Silica |
Iron/rutile and iron/cobalt slips brushed over. Cone 10 Reduction
“I used McNamee Kaolin which is high in Ti; but any kaolin is worth a try….
Brush with iron/rutile for iron-red to orange, iron for rich brown, 2iron/cobalt for blue-black, ferric phosphate for ironred,thincobaltforsoftblue.” H.M.
Exploring the Limits
Built into the grid method is the ability to explore to the limits and beyond. When moving into new territory like this, we are nearly always working blind, and never know what will occur or where. The use of the grid with its broad net approach allows us to quickly pinpoint where the interesting glazes are located. The high bone ash glazes explored here arose from a meeting with Hank Murrow at a workshop I conducted in Salem, Oregon, where he showed me a beautiful glaze on a plate he had done decades ago. He called the glaze Cory’s Weird, and it contained over 30% of bone ash - an amount I found hard to imagine using. Upon returning to Australia I prepared a standard grid set based (very loosely) on the glaze. Part of the set is shown opposite in F. It was interesting enough to warrant further investigation, and after addition of cobalt carbonate and titanium dioxide some very interesting things appeared. The glazes are all fairly stiff at stoneware temperature (not unexpected) with several interesting things happening between A and C corners. Many of the glazes show strong colour break, especially over a dark body or slips with colouring oxides, and some exhibit crystal formation and interesting surfaces. To lower the melting point some frit was added to glaze 12. The result was the glaze in G and H. An unusual coarsely mottled texture sometimes appears (see H) giving interesting variation to colour and mattness. Sometimes crystalline spots form, probably caused by the titanium addition.
From Hank Murrow:
“A few words of background to explain the provenance of this high phosphorus notion. While teaching at Anderson Ranch in Snowmass, CO, I was fortunate to share both studio and dinner table with Cory Levins (aged 17, huge appetite, did the dishes). He later went on to study at Alfred University, where he entertained himself during Art History slide lectures by using a penlight to make up new glazes to test. One of his habits was to take any pronouncement of Dan Rhodes (ie; “Can’t have more than 5% bone ash in a glaze”) and multiply it by a factor of ten to test the pronouncement. Naturally, Cory’s Weird (I named it at the Snowmass post office when I first read the recipe in a letter from Cory) came out of this sort of investigation. He graduated from Alfred, married, and bought a dairy farm/maple sugar bush, intending to build a pottery; but died a year later when his tractor turned over; the end to a wonderful and very promising life. I would love to see his work carried on; and I feel Cory’s Weird is a fitting way to begin. I know he’d be tickled; and I wish all could have known him. My source of bone ash is produced by the Eastman Kodak Company from bones. I have gradually become convinced that Phosphorus is a network former (glassformer) from the experimentation which Cory’s Weird began. However, it was your grid tile method which opened a way to really demonstrate my contention.” H.M.
6 Preparing, Firing and Assessing a Grid Set
Glaze Preparation - Volumetric Blending
300 gram Batch Recipes
The first step is to determine the batch recipes of the 4 “corner glazes”. These are the glazes we blend to produce the full set of 35. We usually use 300-gram batches.
The recipes following are batch recipes for the corner glazes for stoneware, midfire and earthenware firing ranges. They are similarly high in lime (CaO) but manage to lower the firing range mainly by addition of B2O3, and substitution of Na2O for K2O. (This can be seen if we convert the recipes to unity formula or Oxide Weight %, but is not shown here.)
All three sets can be used as the basis for further experimentation by replacing some or all of the CaO with other flux oxides. This was discussed in the chapter: “Choosing the Starting Point”.
Glaze C for each of the three sets is shown. Whether we use percentage recipes from the tables multiplied by 3, or the batch recipes from the “Calculations Page”, we should end up with batch recipes for the corner glazes as shown in the 3 tables.
Stoneware Set - The Standard 0.7 Limestone Set: Glaze C: 70% Potash Feldspar, 30% Whiting
Potash Feldspar | Whiting | Kaolin | Silica | Totals | |
Glaze A: | 126.0 | 54.0 | 120.0 | 0.0 | 300.0 |
Glaze B: | 73.5 | 31.5 | 75.0 | 120.0 | 300.0 |
Glaze C: | 210.0 | 90.0 | 0.0 | 0.0 | 300.0 |
Glaze D: | 105.0 | 45.0 | 0.0 | 150.0 | 300.0 |
**Midfire Set: ** Glaze C: 50% Nephe line Syenite, 20% Whiting, 30% Frit 3134
Nepheline Syenite | Whiting | Ferro Frit 3134 | Kaolin | Silica | Totals | |
Glaze A: | 90.0 | 36.0 | 54.0 | 120.0 | 0.0. | 300.0 |
Glaze B: | 52.5 | 21.0 | 31.5 | 75.0 | 120.0 | 300.0 |
Glaze C: | 150.0 | 60.0 | 90.0 | 0.0 | 0.0 | 300.0 |
Glaze D: | 75.0 | 30.0 | 45.0 | 0.0 | 150.0 | 300.0 |
Earthenware Set:. Glaze C: 100% Ferro Fr. it 3134
Ferro Frit 3134 | Kaolin | Silica | Totals | |
Glaze A: | 180.0 | 120.0 | 0.0 | 300.0 |
Glaze B: | 105.0 | 75.0 | 120.0 | 300.0 |
Glaze C: | 300.0 | 0.0 | 0.0 | 300.0 |
Glaze D: | 150.0 | 0.0 | 150.0 | 300.0 |
We can make these up simply as base glazes, or we might decide to put in a small amount of colourant that is going to have minimal effect other than colour. For example, we could add (% cobalt oxide (= 1 gram in a 300 gram batch).
Preparing the Four Glazes
1. Weigh.
Weigh out the four glazes. In the process of preparing the four corner glazes, try not to lose too much of the 300 grams of dry material. The theory of volumetric blending assumes that we have known weights (in this case, identical weights) in identical volumes. If we lose a lot of one of the corner glazes during preparation, this could affect the result.
2. Wet and Sieve.
Add water and sieve. Start with Glaze A and don’t use too much water. Glaze A will usually be the “thickest” of the four glazes (because it contains the most kaolin) and it should be prepared a little thicker than we would normally use for glazing bisque. This means that by the time we make up C and D to the same volume they won’t be too “thin” in consistency.
3. Adjust Volume.
Measure the volume of the four glazes with a measuring cylinder and add water to adjust them to exactly the same Equalizing Volume (total wet volume), at least 460ml*. For 300 grams of glaze, the equalizing volume will often be around half a litre (500 ml). [Note that this does NOT mean add half a litre of water to each dry glaze!] Once this is finished the glazes are gently stirred until they are uniform. We now have four corner glazes containing equal dry weight made up to equal wet volume. This simplifies the maths.
Blending to Produce the 35 Glazes
We can now blend by volume and the maths is the same as if we were blending by weight. We prepare the remaining 31 glazes (we already have 4) by volumetric blending using the Blending Chart (see next page). It’s important to be accurate and careful in our technique so that the actual recipes of the samples correspond to the theoretical recipes (explained in the chapter: “Working Out the 35 Glaze Recipes”).
Layout. Order is important if we are not to become confused or make a mistake. In the blending and the glazing of the grid tiles, we orient the various “grids”* the same way, i.e. with the “A corner” in the “top left corner”. This avoids a major cause of mistakes.
On our workbench, we set out 35 cups exactly as set out on the Blending Chart, in the 5 x 7 format. Write the numbers 1 to 35 on the cups with waterproof marker pen, and also some identification for the glaze set.
The Blending Chart
The Blending Chart on the next page shows how many ml. of each glaze goes into each cup. Note the explanatory key at the bottom of the diagram.
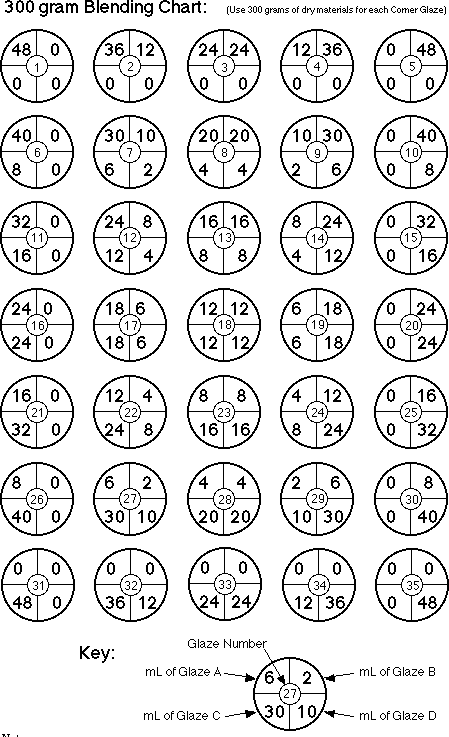
Measuring with a Syringe.
Starting with Corner Glaze A, stir it carefully so it is quite uniform (this is very important), and using a 50 ml plastic veterinary syringe, measure out into each cup the amount of glaze A indicated by the Blending Chart. Repeat for the other 3 corner glazes. (Avoid getting a suspension of fine bubbles in the glaze when stirring as this will affect the accuracy of the volumetric blending.)
If any of the corner glazes are at all watery, do what is required to keep them uniformly suspended, e.g. gentle stirring. Also don’t allow the glaze to settle in the syringe. Glazes C and D will often be a bit watery and settle quickly because they contain no kaolin. The corner glazes must be evenly mixed and uniformly suspended during the syringing process.
Teamwork.
If working in a team of 3 or 4 people, we can break up the jobs thus:
Number 1 works the syringe.
Number 2 keeps track on the blending chart and points to the appropriate cup.
Number 3 keeps the corner glaze suspended if necessary by gentle stirring.
With 4 people we can sometimes work efficiently as two teams, each measuring out two of the corner glazes.
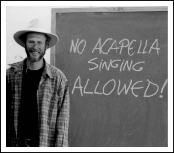
Precautions in the Preparation Stage
The main source of error in this method is someone getting confused. If we are working in a group, we put the control freak in command of this stage! :) It’s particularly important that we take great care from the time we start to weigh out the corner glazes until the time the blending is finished. Any error in this period could affect most or all of the set. There are a number of ways we can ensure that we have done the experiment correctly…
1. Double checking. Make absolutely certain that weights, materials and blending are correct. When applying the 35 glazes to the grid tile (described below) make sure they are applied in the correct order. It is easy to make a mistake. If working in a team have someone double check every action.
2. Visual Order.
In the 5 x 7 layout of the cups, break up the 7 with one or two gaps across the set. This helps us to keep track of where we are.
3. Colour code the blending chart On the blending chart, use 4 colours (e.g. highlighter pen) to colour code the 4 corner glaze ml amounts.
4. Keep the corner glaze suspended Put the corner glaze being syringed into a reasonable large (e.g. 2 litre) container. This makes it easy to stir, easy to syringe, and easy to check there is no glaze settling out. We do this by tipping (without the glaze pouring out!) and checking the base of the container.
5. Check liquid level in the cups.
After blending squat down so the eye is level with the liquid level in the cups, and make sure they all have the same volume. We need identical cups that are transparent or translucent for this. Read to the top liquid level, not to the solids which may have settled. If any cup shows a liquid level higher or lower than the rest, discard the contents, and use the excess corner glazes to blend it again.
Applying the Glazes to the Grid Tiles
Adjusting Water Content
Once the blending is finished, let the 35 glazes stand if possible for an hour or so. Now that the blending is completed it is allowable to add (or remove) water to the 35 glazes to get a good consistency for applying them thickly to the grid tiles. This may mean decanting water off the bottom few rows (low kaolin) and/or adding water to the top few rows (high kaolin). The kaolin functions as a suspender and thickens the glaze. It varies from zero to 40% across the set, and so the glaze water content usually needs to be adjusted in some of the glazes after blending and before applying to the grid tiles.
ID
Print the necessary identification (identification of the set at least, possibly student’s name as well) on the border of each tile using iron oxide or underglaze pencil. ( If the tiles are to be fired in stacks, then don’t write underneath the tile in oxide lest it might fall onto a glaze underneath.)
Layout
Set out the grid tiles ready for glazing. Some of the tiles should be white clay, some iron-y clay. Orient the tiles to correspond with the layout of the glazes on the bench. The “A” marked in the top left corner of each tile corresponds to Corner A (Glaze No.1).
Glaze Application
Stir each glaze before applying it to make sure the blend is mixed together properly.
Apply the glazes one at a time using a well-lubricated syringe, or a small spoon. A syringe is quick as we can apply the glaze to a number of tiles one after another, but it MUST be well lubricated or glaze will squirt into other compartments on the grid. (A smooth action is usually facilitated by putting Vaseline on the plunger.) Try to get thick and thin application with each glaze; thick should be about 2 mm thick. This is important. Use a needle to check it. First apply the thin layer all over the compartment. Once the water is sucked into the bisque and the glaze “set”, apply the second thicker coat covering about half the area.
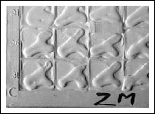
Tips:
- If the glaze consistency is too thick, it goes on rough and lumpy. This can be a problem for non-runny glazes because the glaze does not smooth out in the firing. If the consistency is too thin or runny, it can be hard to get adequate thickness. Experiment with glaze consistency. It should be possible to apply the glazes with a veterinary syringe without much trouble (assuming we are using 200# (200 mesh per inch) or finer materials).
As we syringe the glaze onto the grid tile, it should stay wet for long enough to form into a reasonably smooth layer by liquid surface tension. If it “sets” too quickly add more water.
- Different Syringes. Some designs work better than others. Some are more easily lubricated than others.
- Often the syringe will squirt out of control during glaze application. Hold the syringe at an angle such that it does not squirt onto previously glazed compartments. One person in the team should have the job of cleaning up mistakes like this.
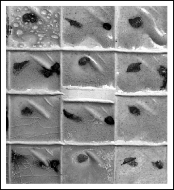
Applying Colouring Oxides (Optional)
We may prefer to fire the glazes as mixed. If however we decide to apply brushstrokes of one or more colouring oxides to the set, this should be done with great care. The main concern is not to swamp the information contained in the systematic variation of fluxes, kaolin and silica. Leave most of each glaze sample untouched, and apply the colourant to only one or two of the grid tiles for the set. Leave the rest plain.
- Apply only a very small dot of colourant with the tip of a fine brush.
- There is usually very little change between adjacent glazes, so there is no need to apply it to more than every second glaze (in both directions).
After the firing, study the oxide dots with a lens. Any colour variation around the edges of the dot gives a hint to what we will achieve if we blend that oxide into the base glaze. It doesn’t tell us how much of the oxide to add, but it does usually indicate if it is worth experimenting more for example with a line blend addition of the oxide to the glaze.
Firing the Grid Tiles
Firing Type
As mentioned elsewhere, there is no correct firing type for any particular set. There is a firing that will produce maximum interesting glazes, one that will produce maximum information for the student trying to understand the way glazes work, and a firing that will reveal those glazes well beyond the usually accepted boundaries… and these are probably all different firings. That’s why we make several replications of the same set. In a grossly over- or under-fired grid tile, there may be just one glaze that makes the whole exercise worthwhile. It’s impossible to know where the real successes will occur, but the “wide net” approach of the systematic method with the grid tiles ensures that if there is anything there, we can find it.
Fast Firing/Slow Firing
There are some glazes that are favoured by quick firing or cooling, but in an experiment like this it narrows the range of possible results, and some qualities simply cannot be achieved. Glazes go through a physical process of fusing, melting, bubbling and smoothing out and at stoneware temperatures attacking the clay body. These things take time. Also crystal growth within the glaze or the clay/glaze interface takes time. Sometimes you have to slow or stop the cooling process at certain temperatures to get certain crystalline effects.
Slow Maturing - Try soaking at the end of the firing. In a cone 10 firing for example, ease back towards the finish so that it takes about an hour from cone 9 to cone 10.
Slow Cooling - Small kilns may have to be fired down to slow the cooling process. This can be done manually, or with a programmable kiln it is possible to set it to do the soaks and slow cooling as part of the firing cycle. Cool at perhaps 100 - 200 deg. C an hour. Alternatively a 30 to 60 minute soak at around 200 - 300deg C below the top temperature can have interesting and beneficial effects.
A similar effect to slow cooling can be achieved with some glazes by re-firing in a bisque. The red colour in shino glaze often benefits from this.
Draw Trials
Draw trials are samples that are taken from the kiln during firing. They give a “snapshot” of kiln/clay/glaze conditions at the time of drawing. They can be used for judging when to finish a firing and for studying the firing and glaze/clay maturing process.
They are particularly useful used in pairs with one left in the kiln to study the role of soaking, fast cooling etc. One can even take out small grid tiles. Any difference found between the pairs of glazes indicates something that can be manipulated by adjusting the rate of cooling.


Virtually Identical Firing Conditions
One of the advantages of using the grid tiles is that we can fire many glazes under virtually identical conditions. This removes the firing as a variable and helps analysis of the results, as we know differences are caused by the chosen variables, and not by extraneous firing variables. In this chapter we are preparing just one set of glazes, but if we embark on a serious course of study, we might soon have a number of sets to fire. We can stack different sets on top of each other, leaving plenty of room for air circulation. Separate the tiles with dobs of kiln wadding about 10mm thick. At stoneware temperatures we may need up to 12 dobs so the tile doesn’t warp too much - 10 around the edge, and 2 in the central area on the raised pads. The number depends on how vitreous the clay becomes in the firing.


Some Aids to Uniform Firing Conditions:
1. Put a spare grid tile on the top as a lid.
2. Avoid resting the bottom tile directly on the kiln shelf, or it will cool slower than the rest.
3. Avoid areas within the kiln where there are steep gradients of temperature etc.* In a small uneven kiln we can help uniformity of firing conditions by using baffles or a saggar.
4. Ensure enough space between tiles for adequate circulation.
A> * We might use these areas sometimes to explore the extremes, but we should be aware if there is likely to be a temperature or other gradient across the grid tile.
At least one set of cones is placed with the stack.
Normally we would fire at least 2 of the tiles, in white and dark clay, more if we have hot and cold spots in the kiln. Store the others to fire under a range of different firing conditions whenever possible.
Bring out the Differences
There are a few precautions worth mentioning that will help us get the most out of each set. A number of things can mask the subtle variations between one glaze and the next in a set, and make them all look very similar.
Glaze Thickness
If the glazes are put on only thinly, this will mask differences. Certainly we do want to see what each glaze looks like thinly applied, but it is most important that we also apply each glaze thickly in part.
Glaze Type. Some glazes are overwhelmed by some ingredient. For example, we can make an interesting set based around a high percentage of manganese oxide to produce bronze and gold metallic glazes. Even if the manganese is treated as a flux (it is a flux as well as a colourant), which means that by this method, it varies substantially across the set, the metallic nature is overbearing, and very little variation occurs across the set.
Clay body
Sometimes a clay body is so powerful in character that it overpowers the glaze. For example bodies with high content of iron oxide, especially if fired in reduction where the iron acts as a flux, can turn most of the 35 glazes in a set into similar iron glazes. On the other hand, the iron-y body can sometimes bring out some interesting quality that is absent on the white clay.
A highly textured clay will sometimes overpower subtle glaze features.
Firing
{float=left}
Too fast firing, too little soak at top temperature, and too fast cooling can all prevent features from emerging. The glaze maturing process takes time; colour-break from the development of the clay/glaze interface zone, the formation of crystals in the cooling and many matt effects… all take time and all contribute to the production of a greater range of interesting features.
Grossly over- or under-firing will usually limit the range of glazes obtained from a set, but will sometimes reveal useful glazes at the extremes of flux, alumina or silica content that might not be discovered otherwise.
Assessing the Results
Once the tiles are drawn from the kiln the job of assessment can begin. With this method there are two levels on which this can occur.. firstly the matter of looking for useful, interesting or beautiful glazes. This is the same in any glaze research. However as a result of the systematic variation of important variables, this method also has the potential to reveal much more. I’m referring to the way cause and effect principles can be revealed when our research has been systematically organized.
It’s important to preserve all details of glaze, clay and firing. This is a matter of thorough and conscientious recording.
For the beginner it’s really useful to plot out results on an Assessment Sheet. Some things are obvious when we look at the grid tile. However some characteristics such as crazing in a dark glaze can only be seen with a lens, and to understand the way crazing changes with varying alumina or silica we have to examine each glaze individually and record whether or not it is crazed on the assessment sheet. We use a different grid for each characteristic, and write a number inside each square corresponding to the property for that glaze on that tile. Use a copy of the assessment sheet on the next page to aid in developing your ability to assess the results.
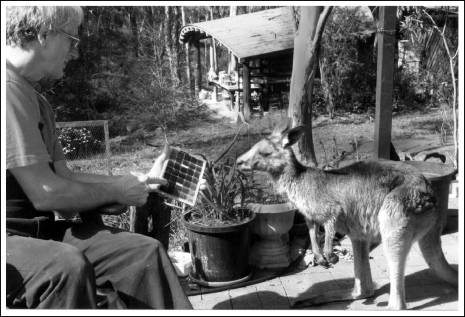
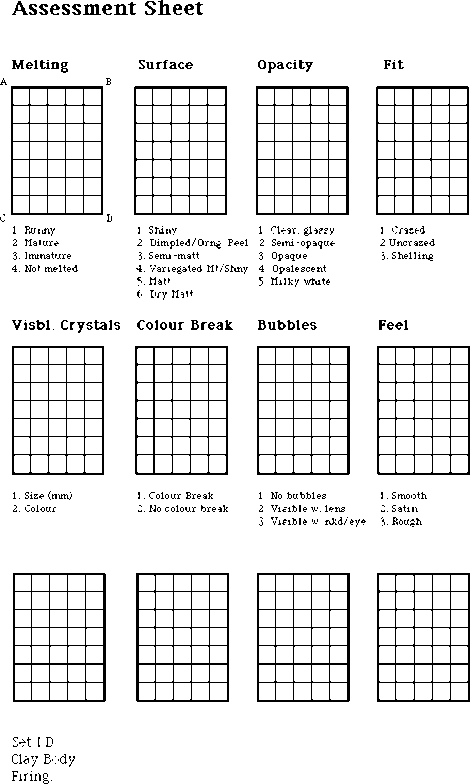
Assessing Glaze Fluidity from the Grid Tiles
One problem with the horizontally-fired grid tiles is seeing how the glazes perform on a vertical surface. The four images here illustrate how we can estimate runniness from the grid tile data.
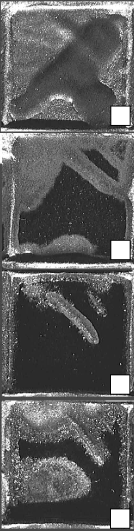
These compartments are 1 inch (25 mm) square. The glaze was applied all over thinly, then a second thick layer was applied in the pattern clearly evident in 1, and still visible as the dark area in 2.
- A very stiff glaze does not thin out over the ridges. (Note the two diagonal ridges in the top right-hand quarter of each compartment.) The glaze does not flow sideways. Thick-thin application is obvious.
- Medium-stiff glazes thin out over the ridges and smooth out, but one can still make out thick and thin application, especially with a non-opaque glaze.
- Runny glazes smooth out to obliterate the difference between single and double application.
- Extremely runny glazes usually reveal themselves by surface tension effects, the glaze leaving bare patches and being drawn up into the edge-angles of the grid compartment.
These examples give a rough guide to glaze runniness. It is not a good idea to assume that our new-found glaze will not run until flow tests have been tried on a small pot or vertically fired tile! See the box: “Dealing with Runny Glazes” on the next page.
Dealing with Runny Glazes
The Next Step
The main purpose of the grid tile is discovery. The normal process of testing individual glazes on larger samples, small pots etc. is still required unless we are willing to risk ruining valuable work and kiln furniture. This process is widely understood and not covered in this text.
Unusable or Dangerous Glazes
Exploring the limits as we do with this approach will always turn up unusable and sometimes even dangerous glazes. Glazes might be under or over fired, poisonous or water-soluble. Sometimes poor glaze fit might cause a pot to shatter in use, or to “shiver” causing the glaze to be shed in dangerous fine shards. There is more in the Appendix on utilitarian risk.
7 Volumetric Addition to a Set
A new set of glazes with very little effort
We have already seen the way that volumetric blending enables a large set of related glazes to be mixed up quickly.
The volumetric blending procedure can be used to extend the results beyond the 35 glazes in the standard grid set. With very little extra work, a whole new set can be obtained.
If we initially produce enough of each glaze, we can split the set into two identical sets, keep one as the original and add something to the other. This is actually very easy to do using volumetric methods. In our example we will add titanium dioxide (TiO2).
Adding Titanium Dioxide to the Set
One of the more interesting opacifiers is titanium dioxide. This is usually introduced either as the pure oxide or as rutile, which contains some iron oxide. But it’s not just an opacifier; like many other ceramic materials it serves in a number of roles in a glaze. One of the main characteristics is the way it readily crystallizes from the glaze, even from additions as low as 1% (Hamer*). Depending on the amount added, the crystals cause a number of interesting effects, including bluish-white opalescence and opacity. It also causes interesting textural breakup of colour and matting of the surface. And like most opacifiers it tends to bleach out colour; the more TiO2 we add, the paler the glaze colour becomes.
A useful exercise to do at least once is to add TiO2 to all the glazes in a grid set and see how it affects them. We will examine here a simple way of adding the same percentage of one ingredient (in this case 5% TiO2) to all the glazes in a set.
Method
Summary
1. Make a “double batch” of the original set.. Weigh up twice the usual of each corner glaze (600 instead of 300 grams dry).
Make these up to at least 920ml Equalizing Volume.
Make a note of the Equalizing Volume.
Use a “double batch” Blending Chart (See box.) and blend the glazes.
2. Divide each glaze in half.
Stir each glaze until it is quite uniform and using the veterinary syringe, draw off 48ml from each one and put it in another cup.
3. Add TiO2 suspension with a small syringe.
Weigh out enough TiO2 to provide the 5% for all 35 glazes, suspend it in water and, using a small syringe, measure out the right amount into each cup. In a few minutes we have a whole new set of glazes. There is some maths involved, but it’s simple to follow.
Quantities
Equalizing Volume (ml) for a “single batch” | Dry Weight per Cup (grams) |
---|---|
700 | 20.6 |
695 | 20.7 |
690 | 20.9 |
685 | 21.0 |
680 | 21.2 |
675 | 21.3 |
670 | 21.5 |
665 | 21.7 |
660 | 21.8 |
655 | 22.0 |
650 | 22.2 |
645 | 22.3 |
640 | 22.5 |
635 | 22.7 |
630 | 22.9 |
625 | 23.0 |
620 | 23.2 |
615 | 23.4 |
610 | 23.6 |
605 | 23.8 |
600 | 24.0 |
595 | 24.2 |
590 | 24.4 |
585 | 24.6 |
580 | 24.8 |
575 | 25.0 |
570 | 25.3 |
565 | 25.5 |
560 | 25.7 |
555 | 25.9 |
550 | 26.2 |
545 | 26.4 |
540 | 26.7 |
535 | 26.9 |
530 | 27.2 |
525 | 27.4 |
520 | 27.7 |
515 | 28.0 |
510 | 28.2 |
505 | 28.5 |
500 | 28.8 |
495 | 29.1 |
490 | 29.4 |
485 | 29.7 |
480 | 30.0 |
475 | 30.3 |
470 | 30.6 |
465 | 31.0 |
460 | 31.3 |
The first part is working out how much dry material there is in one cup of glaze. This varies depending on what Equalizing Volume was used in the blending. To get started, let’s assume that we have made double the usual volume (a “double batch”), and after the blending we’ve divided each glaze into two equal portions. We now have two identical sets of 35 glazes. Working out the Dry Weight of a 1% Addition 1. First we need to work out the dry weight of glaze in one cup. We can use the table on the left, providing that: * A, B, C and D are each 300 gram dry batches (600 if using a “double batch”).* * We have 48 ml of glaze in each cup. * We use 35 cups. * Equalizing Volume is measured in ml.
- Now that we have the dry weight in one cup, it’s easy to work out 1%: 1% Addition = Dry Weight in 1 Cup ÷ 100 Applying this to our example: 1% of 30 grams is 30 ÷ 100 = 0.3 grams.
Working out Volumes for a 5% Addition
Once again we need to launch into some maths, but it’s easy maths and it’s MUCH easier and quicker than weighing out 35 portions and mixing them separately into each cup. Continuing with the example….
Assume we are messy workers, and will spill some! Let’s prepare enough for 40 cups (we only need enough for 35) so we will have a bit left over. We’ve just calculated that a 1% addition to one cup would be 0.3 grams. Therefore a 5% addition would be 1.5 grams. To prepare enough for 40 cups, we would need 40 x 1.5 grams = 60.0 grams.
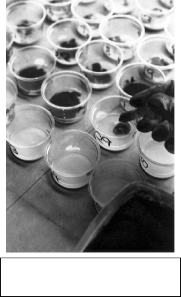
Tip: Use a smaller syringe for this exercise, e.g. 5 ml
Addition Procedure
- Weigh out 60.0grams of titanium dioxide.
- Add water to this and sieve.
- Bring it up to an appropriate Total Volume. (Some easy multiple of 40 would be convenient in this case, perhaps 80 ml?)
- Keeping the solids suspended by gentle stirring, measure out with a small syringe one fortieth of this Total Volume into each of the 35 cups.
- Stir each glaze until the titanium dioxide suspension is uniformly mixed in. The new set is finished and ready for sampling.
8 Using the Grid Method with Natural Materials
Origins
While writing Chapter 26 - Rock Glazes in “Stoneware Glazes - A Systematic Approach” it became obvious that it would be very useful to have an experimental technique enabling systematic variation of alumina and silica where the Seger formula of a rock was not known. The biaxial blends presented on Page 205 (Page 344 in the First Edition) do this. The recipe method presented in this book actually arose from this exercise. So in applying it to natural materials, we are really going back to the source.
One of the big advantages of using recipe rather than Seger formula is that we can use any flux material we like without needing an analysis. Seger formula is great if we are chasing a concept - trying to reproduce a particular type of celadon glaze for example. It may be critical to have (or to exclude) certain oxides, and accurate analyses will enable us to do this, and to accurately measure the amounts. But using the Seger method we will not be able to introduce materials where we have no analysis figures.
Using the recipe grid method as presented here allows us to take any natural material that we know is a flux material and use it in a grid and systematically vary alumina and silica over a large range. This vitally important experiment works even without any idea what the flux material contains.
Although we do not need to know the analysis of a raw material it’s useful to be able to classify it into one of the categories:
flux material
alumina source
silica source (e.g. grass ash)
colourant or opacifier
These will be considered one at a time.
Flux Material
Wood Ashes
Virtually any wood ash can be used as a flux material. They are very variable in composition, but many are high in CaO (lime) and a simple way of introducing wood ash into a glaze is to replace whiting (the most common source of CaO in glazes) with wood ash on a weight for weight basis. (The glaze will almost certainly be different.) If the wood ash is not washed, it will usually contain some soluble flux materials that might make for difficulties in glaze application. They can be very caustic. Use rubber gloves.
Rock and Mineral Materials
It is very easy to test rocks and minerals to see if they will melt in the firing. Enough to glaze a miniature bowl e.g. 2 inches (50mm) across takes only a few minutes to prepare. Almost any rock can be easily crushed with a hammer or a “dolly” to fine gravel, and then ground with some water in a mortar and pestle until most will pass through a fine (say, 100 mesh) sieve.
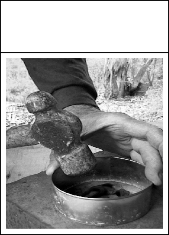
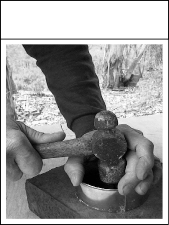
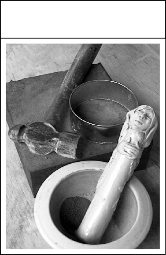
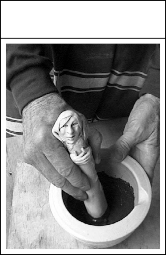
Igneous Rocks
Serpentinite
Pyroxenite
Dunite
Basalt
Dolerite (Diabase)
Gabbro
Andesite
Micro-diorite
Diorite
Trachyte
Micro-syenite
Syenite
Rhyolite
Pumice
Quartz-felsite
Granite
Looking at this list of rocks, the amount of silica incorporated into the rock increases (and therefore the fluxing power decreases) as we move down the list. In general, the rocks at the top of the list (ultrabasic and basic rocks) have a higher flux and iron oxide content and give darker glazes than those at the bottom of the list (acidic rocks, especially granite).
Sedimentary and Metamorphic Rocks
Some of these make excellent flux materials, but many are very high in silica and alumina. It’s difficult to make generalizations about them. Get a geologist friend to help, or just try them and see. If a fusion test melts the rock, it can be used as a flux material. In most cases we are talking about stoneware materials, but many can be used in mid-fire, or in small amounts in earthenware.
Metamorphic rocks form when an existing rock is changed by pressure and/or heat. They will often be similar in composition to the rocks from which they derive. So for example a gneiss might be chemically similar to the original granite. If the rock has been significantly heated, the composition might be changed a lot.
Many sedimentary rocks are high in silica but some will reflect the composition of nearby igneous rocks from which they are derived and be useful as a flux material.
Arcose sandstone is high in feldspar (usually potash).
See the end of this chapter for a list of useful references.
Alumina Sources
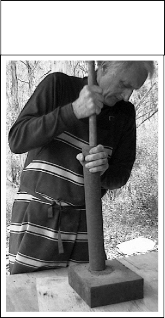
This refers to a material that we are adding to the glaze mainly to provide extra alumina (as opposed to adding for the purpose of providing a flux or extra silica). Any of these materials can be used in place of kaolin (as the source of variable Al2O3) on the vertical axis of a (non-standard) grid. However the Recipe Grid and Recipe Table are designed for kaolin, and using these recipes and substituting other alumina sources will give differing degrees of usefulness. You should find for example that replacing kaolin with alumina gram for gram will give many unfused glazes across the top of the grid. This is where the Seger approach comes into its own but here we are keeping the method as simple as possible by sticking with recipes.
Clays
The most usual alumina sources are clays, kaolin (china clay) and ball clay being the most common. Ball clay has a lot more silica and less alumina than kaolin, and it usually contains a small amount of flux materials and noticeable iron content too.
Alumina etc.
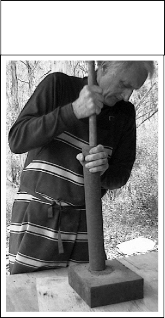
Pure alumina or alumina hydrate are sometimes added to a glaze as a source of Al2O3, especially where we are attempting to simultaneously achieve high Al2O3 and low SiO2 values. The big advantage of using a clay rather than pure alumina as our source of Al2O3 is that clay is also a suspender, and it helps make the glaze less powdery before it is fired. Bauxite is common is some places in Australia. It is essentially Al2O3.2H2O - usually there is a little of the colourant iron oxide as well.
Silica Sources
Quartz, Silica, Flint
General Formula: SiO2 There are many different sources of reasonable pure SiO2, all of which can be used as the source of variable SiO2 in the grid sets. The materials that come to your pottery supplier in bags may be called, “silica”, “flint”, “quartz”, “potters flint”, and they all are much the same and give fairly similar results. If your “flint” is really from ground up flint stones, the glazes will probably craze less.
Opal
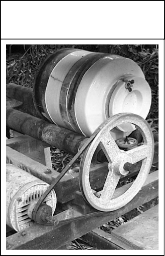
Has the general formula: SiO2.nH2O
The “n” in front of the water molecule indicates variable amount. There are many forms of non-precious opal widely available. One of the most useful is:
Diatomite (diatomaceous earth)
This is formed from the silica rich shells of diatoms and other tiny lifeforms. The water content causes it to shrink a lot as it dries, much like a clay, and just like a clay it will cause crawling if used in large amounts. Any kind of crawling can be used to achieve lizard-skin effects (photo). They usually look best with another glaze underneath bleeding through at the cracks. The underneath glaze does not have to be too thick, and it can have a lower melting point than the top glaze containing the diatomite.
Using Natural Materials in a Standard Recipe Grid.
We can include any natural flux material in Glaze C, our starting point, and make a normal grid. We can even make Glaze C entirely from natural materials as the starting point.
Some suggestions for Glaze C:
- Take any Glaze C recipe containing whiting, and replace this with wood ash.
- 100% Wood ash Also, reduce the wood ash by introducing other flux materials such as dolomite, talc etc.
- 100% Rock powder Also, reduce the rock powder by introducing other flux materials such as whiting, dolomite, talc etc.
- 50% Wood ash 50% Igneous rock (e.g. basalt)
Vary the proportions from 50/50 (e.g. to 75/25)
Appendices
Appendix 1 Equipment and Materials
Most of the requirements are easily available, but some are specialized. Below is a list that would equip a class for a workshop preparing several grid sets of glazes. Work out for yourself what you need from the following guide.
Firstly let us assume a class will contain about 20 students. It will be divided into teams of about 4 people. Some quantities are based on how many teams there are, though some things are calculated per class, or per student.
List of Equipment and Materials
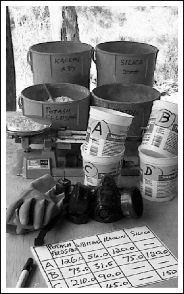
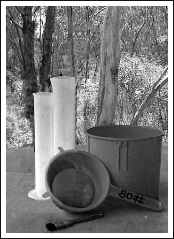
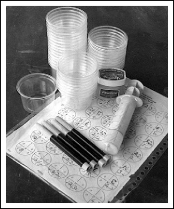
Weighing
1. Accurate Scales, such as Ohaus triple beam balance. At least 1 per team, 2 if possible.
2. Plastic containers for the Corner Glazes (1 or 2 litre, e.g. ice-cream) - 4 per team
3. 300-Gram Batch Recipes for the four corner glazes for each set.
4. Glaze materials - See “Glaze Materials” later.
5. Waterproof Marker Pens - 1 per team.
6. Dust masks - 1 per student.
7. Disposable rubber gloves - A few pairs - 2 or 3 per team.
** Wetting, Sieving, Adjusting**
8. Sieves - 80 mesh or a bit finer, preferably at least 1 per team.
9. Plastic Buckets, mainly for sieving into - 1 per team.
10. Paint Brush (1 inch or 25 mm) - 1 per sieve.
11. Tall Measuring Cylinders - 500 ml or 1 litre (preferably plastic or nylon) 1 per team. Definitely prefer tall scientific measuring cylinders to jugs. A shallow fat jug does not give accurate measurement.
Blending
12. “Blending Chart” enlarged to A4 or Standard Letter size. See diagram Page 102. 2 per team.
13. Highlighter Pens - 4 colours will do for the whole class.
14. Disposable Foam or Plastic Cups - 100ml. Preferably broader (stable) rather than taller - 35 per team.
15. Graduated Veterinary Syringes - 50 or 60ml plastic - 2 per team.
16. Vaseline - 1 container for the whole class.
Application
17. Bisque Fired Grid Tiles - see “Making Grid Tiles” below.
18. Colouring Oxides - See later.
19. Artists’ Brushes for applying oxides - 4 per team
Miscellaneous
20. Pocket Calculator 1 per team.
21. Hand Lens - 1 per student, or 1 per team at least.
22. Ware Boards or cut down cartons to store the sets in their disposable cups.
23. Individual Tiles 2 inches (50mm) square, or very small bowls, thimble or egg-cup size (optional). 5 or ten per student should be adequate. These are for follow-up work after seeing the fired results from the grid tiles; they are used for further testing of promising glazes.
24. Wax emulsion and some bubble wrap would be useful if students are to be taking glazed grid tiles home for firing. Once the tile is ready to go into a firing, it can be painted with wax for safe transport. The tiles can even be sent unfired through the post if well padded.
25. Students should bring an apron or similar, and the usual notebook etc.
Safety Considerations
For safety reasons keep work as dust free as possible. The main dusty part is weighing out the glazes until they are wet up. This should be done in a dust-safe place, either with extractor fans or outside with a breeze or fans blowing dust away. Use effective dust masks and rubber gloves where necessary.
Glaze Materials
Flux Materials - See the chapter “Choosing a Starting Point” for a discussion on what flux materials to try.
Kaolin - initially use something reasonably pure, like Grolleg, EPK or Eckalite.
Silica material - e.g. “silica”, quartz, flint
Colouring oxides - e.g. iron oxide, cobalt oxide (or carbonate), copper oxide (or carbonate), nickel oxide, etc.
The following table gives analyses of pure feldspars and kaolin for comparison, assuming you can get an analysis.
Theoretical Analyses | K2O | Na2O | Al2O3 | SiO2 | Ignition Loss |
Potash Feldspar | 16.9% | 18.3% | 64.8% | ||
Soda Feldspar | 11.8% | 19.4% | 68.8% | ||
Kaolin | 39.5% | 46.6% | 13.9 |
For feldspar, the higher the K2O or Na2O component and the lower the SiO2, the more pure it is.
For kaolin, the higher the Al2O3, the more pure. Theoretically it should have no iron (Fe) oxides and no titanium dioxide (TiO2)
In the “standard recipe grid set” we assume that we use fairly pure kaolin and silica material. With non-standard sets, we can use anything we please. It is not the case that we necessarily get better glazes from pure materials. However in initial exploration of glaze theory, it can be useful to eliminate some of the “wild-card” variables for the sake of clearer understanding. Sometimes it is precisely these wild-cards that spice up a recipe.
Making Grid Tiles
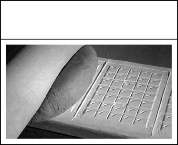
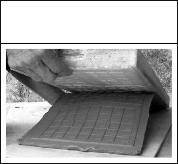
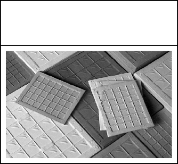
Make them in a variety of clay types but definitely including some white clay, and some iron-y clay. It is a tile with retaining walls for the 35 glazes laid out in the standard grid pattern of 5 glazes across by 7 down. They are easiest made by carving grooves about 3mm deep into a slab of flat plaster so it looks a bit like a shallow block of chocolate, and rolling clay onto this to give 3mm ridges. Make the outside ridges about 10mm (~1/2 inch) to provide a border and somewhere to put kiln wadding when stacking the tiles on each other. Also carve some shallow grooves into the corner of each of the 35 compartments in the plaster. This gives some raised texture on the tile for the glaze to break over. A good size for the compartments is around 1 inch or 25mm square. Engrave an “A” into the top right corner of the plaster so it appears on the top left corner of the tile.
Number of tiles:
Assuming about 20 students, then a total of 50 tiles would be adequate for a one or two-day workshop. Do some in white clay, some in iron-y stoneware clay, perhaps some in terracotta if you use this.
Note: It is possible to design the floor of the grid tile compartments to automatically give varying glaze thickness, and with ridges for the glaze to break over. ?
Appendix 2 Safety and Health
My First Glaze - A cautionary tale
For more than a hundred years the issue of safety in the ceramic industry has been a matter of growing concern. It began with the discovery that lead glazes were poisoning potters and their families, and also people using the pots. We are still discovering the hazards due to some commonly used ceramic materials and practices.
The best way to achieve safety is not to use dangerous materials in the first place. Use safe substitutes in place of them. See later the section on non-poisonous materials.
Safety considerations fall into three broad categories:
1.. safety for the person making the ceramics and their family
2.. safety for people who may be in the studio (friends, visitors, clients, children, employees, students).
3.. safety for the user or owner of the ceramic piece.
There is no consensus on some issues so here we need to keep on the safe side. It is difficult to draw a line between safe and unsafe. Concern for our well-being tugs towards a lowest common denominator, while the desire of most artists to have access to the widest possible palette of colours, surfaces etc. lures us towards materials that have some safety problems. There is always a tradeoff between the foolproof or safe on the one hand, and the expressive or responsive on the other
The teacher and student ceramic worker need to be aware of a number of safety factors:
- Their legal obligations
- The hazards and how to control them
- Special problems for the users of the ceramic
- Special problems with young children
- Resources for Health and Safety
Legal Obligations
You are legally responsible for the safety and health of anyone in your studio. This is known as a “duty of care”, and there are significant penalties if you fail to provide a safe environment.
Laws relating to work places including potters’ studios are designed chiefly to protect the health and safety of employees. If you occasionally pay someone to assist you, you need to be familiar with your obligations under these laws; penalties for breaches are severe. The relevant law is the Occupational Health and Safety Act in your state in Australia. Details can be obtained from the government department usually called the Department of Occupational Health and Safety, or in some states, “Worksafe”. As well as information on the laws, these departments are excellent resources for information on hazards.
Hazards from Raw Materials
We need to be aware of the dangers posed to us, our students and customers, by the materials we use. In Australia, the US and the UK there are standards and guidelines that we can use. Material Safety Data Sheets (MSDSs) are used to provide information on a product’s hazards and how to use it safely. MSDS reliability is variable because usually it’s up to the material manufacturer or supplier to provide them. However they are usually very informative and they should be made available to all who use these products, especially students. Where students are young they should be denied access to certain dangerous materials. See recommendations for non-poisonous materials later.
Of particular interest in the MSDS are the sections dealing with precautions for use, and safe handling. Time-weighted Average values (TWAs) and/or Threshold Limit Values (TLVs) are used to quantify exposure risk. TWAs and TLVs are numbers expressed in parts per million for gases or vapours, or in milligrams per cubic metre for dust or particulate matter. The number indicates a level of contamination that is acceptable as posing no significant risk in the normal work environment. The smaller the TLV or TWA number, the more dangerous the material. This is useful because we can make comparisons with things we know. For example the TLV value for cadmium is smaller than that for arsenic; cadmium is therefore considerably more dangerous.
Non-poisonous Materials
It is possible to achieve a wide range of colours and effects using non-poisonous materials. There is little poisons hazard associated with most of the following oxides in standard ceramic materials.
Base Glaze constituents: K2O, Na2O, CaO, MgO, ZnO, SrO, Al2O3, SiO2*.
Colourants and opacifiers: iron oxide, tin oxide, zircon, titanium oxide and rutile are relatively non-poisonous. Although one could spend a lifetime using just these materials, most ceramics workers use a wide range of materials that have some degree of poisons hazard.
Utilitarian Risk
Functional pots can pose both physical and chemical risks to the user arising from the glaze. The main physical risk comes from a glaze that is in compression causing the glaze to shiver off in dangerous glassy shards, or in rare cases the fault can cause the pot to shatter while full of hot food or liquid. This usually happens during a sudden temperature change, like pulling it from the hot kiln, filling it with boiling water, or taking it from a hot oven. The potter can perform tests for these problems including use of exaggerated temperature changes to provoke a failure. The oldest and most common test is for the potter to use a sample of the ware in their own home. The main chemical risk to the user is from leaching of poisons from certain glazes especially under the influence of acid or alkaline foods or drinks. Certain oxides can become soluble under certain circumstances, and this allows their ingestion with food or drink. Some materials are best avoided on the inside of functional ware unless the potter is willing to have their glazes regularly tested for leaching. Of the usual flux oxides, lead is the worst by far, and should be avoided if possible. Fritting the lead (i.e. industrially incorporating the lead in a glass) reduces the risk of leaching but the lead may become soluble again depending on how, and with what, the frit is used. Other flux materials with “problems” are lithium, barium (carbonate), manganese (which is a flux as well as a colouring oxide) and possibly boron. A number of other colourants have problems too. Copper can promote solubility of other dangerous ingredients. Uranium can be both poisonous and radioactive. Most colourants apart from iron oxide have problems especially if used in excess to the point of overload and should be used with care.
Children
Children cannot be expected to know how to avoid danger. Most workshops and studios are NOT safe places for children, and they should be supervised at all times; keep them out of your workspace unless they are being supervised.
Occupational Health and Safety Resources
The subject of safety in ceramics has been well studied in recent years, and there are some excellent texts available This text does not provide a comprehensive coverage, and the reader is directed to the references listed here in the box.
In the last 30 years there has been a great blossoming of involvement with ceramic arts. Sadly we are now seeing some of the results of our ignorance of the risks involved. It would be a pity if we fail to learn from these sad lessons. There are those who would impose much stricter rules on what we may use in our works, and saddle us with restrictive legislation. If we wish to continue to freely use potentially hazardous materials we must use them in a responsible way. Artists have always used dangerous tools and materials, and we CAN use them safely. But to do this we need to inform ourselves of the dangers and the precautions we can take.
Special thanks go to Dr. David Biggins for his help in preparing this section.
Appendix 3 Useful Maths and Chemistry
Reading a Chemical Formula
Having this skill makes available a large range of valuable information for potters.
Presented here are the tools necessary to:
1. Read a Seger formula
2. Compare materials using Seger formula or oxide weight % and estimate their usefulness
3. Understand the idea of glaze reformulation.
Some Raw Materials
Question: What oxides (or carbonates, water etc.) do these materials contain, and in what proportions?
Note how the big numbers in front of each oxide indicates the ratio of the various oxides one to another. (If there is no big number, understand this to mean “1”.) This ratio is not a weight ratio, it is a “molecular ratio”. In the formula for kaolin (Al2O3.2SiO2.2H2O) we have one molecule of alumina to two of silica and two of water.
Many of the raw materials are natural unrefined minerals, and as such they usually contain impurities. For this reason the molecular ratios of natural materials are rarely neat whole numbers. (For example the formula for nepheline syenite is 0.25K2O?0.75Na2O?1.11Al2O3?4.6SiO2 (variable)). The ratios give an indication of the degree of purity (by comparison with the theoretical formula) and also give a useful guide to the beginner of the effectiveness of one material compared to another in introducing (or excluding!) a certain oxide. For example if we wish to introduce magnesia (MgO) to a glaze, magnesium carbonate is more effective than dolomite on a weight for weight basis, because the dolomite is bringing in lime as well (compare the two formulae opposite); the molecular ratio numbers give the precise amount. Another example would be to compare the effectiveness of various frits in introducing, say, soda (Na2O) to a glaze. In general terms, the larger the soda figure and the smaller the others, especially the alumina and silica, the more effective it is as a source of soda. You can do this for yourself by comparing the analyses of, say, Ferro frit #3110 with Ferro frit #3134.
K2O | Na2O | CaO | B2O3 | Al2O3 | SiO2 | |
Ferro frit #3110 | 0.06 | 0.65 | 0.29 | 0.10 | 0.10 | 3.00 |
Ferro frit #3134 | 0.00 | 0.32 | 0.68 | 0.63 | 0.00 | 1.47 |
Question: Which is the stronger source of soda? Which is the stronger source of boric oxide? This information is obvious to anyone who learns the 12 oxides presented in the book Introduction. There are numerous sources for the analyses of these frits. For example: Cushing’s Handbook Page 68, and from the Internet.
Three Ways to Look at a Glaze
We have three different ways of looking at the chemical composition of a glaze (or clay body): Recipe, Seger formula and oxide weight %
There used to be active debate about which was the most useful way to look at a glaze, but this argument has become somewhat irrelevant now we have access to clever software that can easily convert from one form to another. The fact is that each way has its advantages and its disadvantages, and so all three methods will continue to be used. One thing that needs to be understood though is that glaze calculation software can not be used properly without understanding some of the theory.
Recipe
This shows the weight ratio of raw materials before the firing. This is the most accessible way for most people of looking at a glaze. It has some disadvantages however when you are trying to make a comparison between glazes using different raw materials. But this is the one form that every ceramic artist understands, e.g.:
Glaze Recipe:
50 Potash Feldspar
35 Whiting
15 Kaolin
We normally express the base glaze recipe as a percentage to make it easier to compare glazes. Colourants and opacifiers are additional to the 100% of base glaze. For example:
100% base glaze
+2% colouring oxide.
Oxide Weight %
Here we are looking at the weight of the fired oxides expressed as a percentage. It is theoretically possible to make up a glaze using the pure oxides in the recipe. We don’t usually do this because many of the oxides are water soluble, or have other problems. But if we were to mix a glaze in this way, the oxide weight % analysis and the recipe % would be identical. This is explained further below. We need to be familiar with this sort of expression because many analyses of our materials , and of clays and glazes in texts, are expressed in this form.
Reading Oxide Weight %
This is the oxide weight % analysis of a glaze after the firing. It shows the proportion of the various oxides present expressed as a weight percentage:
9.4% K2O
4.5% CaO
18.3% BaO
8.1% ZnO
12.1% Al2O3
47.7% SiO2
So if we were to weigh out the pure oxides in the proportions shown, mix them dry and fire them, we would obtain this glaze. This is what I meant earlier by “if we were to mix a glaze in this way, the oxide weight % analysis and the recipe % would be identical”. One advantage of using oxide weight % analysis of a glaze is that we can convert from analysis to recipe without having to know Seger formula or molecular weights.
Reading Weight % Figures on a Raw Material Analysis Sheet:
As mentioned before, the raw materials often contain materials that burn out. The Weight % figures on an analysis sheet look like an oxide weight % analysis, but these figures apply to the material before it is fired, and there are often some extra entries; there is commonly an L.O.I. (loss on ignition) figure. The “loss on ignition” is due to anything that burns out during the firing. In clays it is mostly water (H2O). It might be carbon dioxide (CO2) from carbonates, or sulphur dioxide (SO2) from sulphates. Some materials contain ordinary carbon (C) that burns out. Chlorine (Cl) burns out, and fluorine (F) sometimes burns out. Sometimes these materials are separately listed on the analysis sheet, but often they are all included under the one heading of L.O.I. Sometimes they are simply omitted, but you will find that the % analysis does not add up to 100%. The difference is (or should be) the L.O.I. The analysis in the box is for an Australian ball clay from Victoria:
Typical Chemical Analysis:
% by weight air dry analysis
| SiO2 | 60.03 |
| Al2O3 | 23.35 |
| Fe2O3 | 0.83 |
| CaO | 0.01 |
| MgO | 0.76 |
| K2O | 2.71 |
| TiO2 | 1.95 |
| Na2O | 0.12 |
| L.O.I. | 9.16 |
Soluble Salts:
| NaCl | 0.42 |
This all adds up to 99.34%, including the L.O.I. and the NaCl (salt). A slight discrepancy is normal when dealing with actual analyses of real materials, as opposed to theoretical figures. See also “Loss on Ignition - Calcining Calculations” on page 157.
Seger Formula
Also called the unity formula or unity molecular formula, this shows the molecular ratio of the oxides after the firing. This is also referred to as a molecular formula. It expresses a glaze (or clay) composition as a molecular ratio: so many of this molecule to so many of that. The main disadvantage of this method is that it is not a particularly intuitive way of looking at glaze materials because we have no way of “counting” molecules.
Seger (Unity) Formula
| 0.2K2O | | |
| | 0.33Al2O3 | 1.46SiO2 |
| 0.8CaO | | |
Both the oxide weight % method and the unity (Seger) formula method make it possible to substitute completely different raw materials in a glaze formula and achieve a virtually identical glaze. This is illustrated later under “Chemically Identical Glazes from Different Materials”(P. 150).
Reading a Seger Formula
To make various glaze formulae more easily compared, the convention is for all glazes to be mathematically adjusted so that the fluxes add to 1.0 (unity).
[Most clays however have low or zero fluxes, so the convention here is for the alumina to be expressed as unity, which makes the numbers more manageable. This may seem arbitrary, but the molecular weight also changes depending on what we choose to make unity, and this balances out the maths in the end. Trust me!! ]
This is a typical Seger formula for a glaze:
0.3 K2O | ||
0.25 MgO | 0.35 Al2O3 | 3.8 SiO2 |
0.45 CaO |
Firstly notice that the five oxides are sorted into their categories of flux, alumina and silica.
Secondly, note that the three fluxes on the left add up to 1 (unity).
Thirdly, be aware that the numbers refer not to the weight of the oxides, but to their molecular proportions… To make it easier to understand, let’s deal with whole numbers rather than decimals; multiply all the numbers by 100….
30 K2O | ||
25 MgO | 35 Al2O3 | 380 SiO2 |
45 CaO |
Then we can say that for this glaze there will be 30 molecules of K2O to every 25 molecules of MgO, to 45 of CaO, to 35 of alumina and 380 of silica. If it were possible to count them out in the numbers indicated, mix and fuse them, we would have this glaze. But unfortunately we can’t count out molecules… we do it by weighing out the materials. And to get the right weights, we have to do a formula to recipe conversion, which is beyond the immediate scope of this book. It takes 5 or 10 minutes with a calculator, or if you have glaze calculation software running, as long as it takes to type in the numbers.
Comparing Recipe and Seger Formula for 3 Standard Recipe Grids
The graph on the next page illustrates three standard grids from the Limestone/Feldspar Series that was introduced in Chapter 3, Choosing a Starting Point. It illustrates one of the shortcomings of relying only on recipe data ignoring oxide information. The three grids illustrated represent sets 0.9L, 0.7L and 0.6F from the Limestone/Feldspar Series Table.
If we were to plot out kaolin and silica values for the 35 recipes in each set, the three “grids” would be identical; this is built into this recipe method because the kaolin and silica values for each of the 35 glazes are the same from set to set. If however we plot the Al2O3 and SiO2 figures for the Seger formulae for each glaze, the grids look quite different from each other.
The recipes for Glaze C for sets 0.9L, 0.7L and 0.6F are marked on the diagram.
In many sets, glaze C is correctly regarded as a “low alumina/ low silica” glaze. However it can be seen here that if the flux set is high in feldspar (e.g. set 0.6F) then Glaze C will already be high in alumina and silica before we generate the rest of the set. The strong fluxing action of the potash and soda from the feldspar (compared with the lime from the whiting) determines that many of the glazes will melt in a stoneware firing, in spite of the high Al2O3 and SiO2 values.
In spite of the much larger area covered by set 0.6F, the differences with-in the set (between the 35 glazes) are much less marked than in set 0.9L.
So the extra Al2O3 and SiO2 brought in with feldspar can lead to confusion if we stick strictly to recipe and ignore the oxides present. This can be seen in a number of glaze phenomena. For example cobalt oxide in association with TiO2 in high Al2O3 glazes will often give greens rather than cobalt blues. If the set contains cobalt and TiO2 we often find these greens around Corner A, the “high alumina” corner. However if we look at the recipe for a well-known example of this effect, the recipe contains 8% kaolin (see the recipe for Reitz Green in “Feldspathic Glazes”, P.82.) This would put it at about Glaze 26, immediately above glaze C on the grid.
Reformulating Glazes
Chemically Identical Glazes from Different Materials
The following table shows two limestone glazes expressed in all three formats. Note that the recipes are quite different, but they have the same oxides in the same proportions. So once the two different recipes are fired, they yield chemically identical glazes, in theory at least. In reality they will usually show some differences because the physical nature of the raw materials does have some effect, and one can rarely obtain such theoretically pure raw materials. But the two glazes are more alike than not, and we can see clearly how the unity formula or the oxide weight % figures are a better guide to the chemistry of the glaze than is the recipe.
Recipe | Oxide Weight % | Seger Formula: |
---|---|---|
Glaze 1: | ||
54.8% K Feldspar | 10.4% K2O | 0.3 K2O |
23.0% Whiting | 14.5% CaO | 0.4 Al2O3 2.7 SiO2 |
8.5% Kaolin | 15.0% Al2O3 | 0.7 CaO |
13.8% Silica | 59.9% SiO2 | |
Glaze 2: | ||
60.9% Feldspar | 10.4% K2O | 0.3 K2O |
29.7% Wollastonite | 14.5% CaO | 0.4 Al2O3 2.7 SiO2 |
9.4% Kaolin | 15.0% Al2O3 | 0.7 CaO |
59.9% SiO2 |
In glaze 2 we have replaced whiting with wollastonite as the source of CaO. Because the wollastonite brings in a lot of silica (SiO2), the recipes are quite different if we wish to maintain the oxides in their correct proportions. When we make replacements like this, we need to use formula to recipe conversion. This will not be covered in this recipe-based course, but students with glaze calculation software can easily experiment with using different sources of the same oxides and see what effect it has on the recipes.
Essential Maths
Percentages
The convention used in most cases in this course is where the dry weight of the base glaze adds up to 100%. Usually we add colouring oxides and opacifiers on top of this figure. See the following example:
70% Feldspar
30% Whiting
+5% Red Iron Oxide
Percentage Calculation:
Recipes, especially batch recipes, are often expressed in “parts” that are not “percentage parts”. It is easier to compare two recipes if they are both expressed as percentages. There is a simple maths procedure that converts a “parts” recipe to a “percentage” recipe:
Example for Calculating Percentages:
A recipe is given as:
3 parts Feldspar
2 parts Whiting
1 part Kaolin
Step 1: Add up the “parts”. In this case “Parts Total” = 3 + 2 + 1 = 6
Step 2: Apply the Percentage Formula:
% of Material = (“Parts of Material” ÷ “Parts Total”) × 100
Therefore:
% of Feldspar = (3 ÷ 6) × 100 = 50%
Similarly:
% of Whiting = (2 ÷ 6) × 100 =33.3%
% of Kaolin = (1 ÷ 6) × 100 =16.7%
Step 3: Double check by adding the percentage figures to make sure they come to 100% or very close. If they don’t you’ve made a calculation error.
Ratios and Proportions
If we have twice as much feldspar in a recipe as whiting, we say the ratio of feldspar to whiting is two to one. We may write this “2:1” or “2/1”. In a simple case like this the maths is easy, and we can see that if the feldspar in the batch were for example 1800 grams, then the whiting would be 900; in this case the whiting is always half the feldspar. Some people have problems with numerically more difficult examples. They are easy to understand if we use one of the two following methods.
Graph Method
{float=left}
The sloping line in the first diagram illustrates the simple case presented above with two materials in the ratio of 2 to 1. We can see immediately that we don’t need to stay locked into these numbers. For example if we have 3.5 feldspar, we can read off the corresponding amount of whiting at the arrow (equals 1.75).
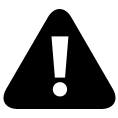
Maths Method
{float=left}
If we wish to do it mathematically rather than on a graph (and maths is much quicker) then we use the following fact:
(x / y) = (a / b)
We can rearrange this so that if we know a, b and y, we can calculate x:
x = y × (a / b)
Example 1:
Suppose we are a bit short of feldspar, and want to make up as much glaze as possible using what little feldspar we have, and using the following recipe:
64% Feldspar
23% Whiting
13% Kaolin
Let’s assume we have 427 grams of feldspar. The problem is set out as follows:
(Note - We can use the same diagram but it is NOT to scale for this example)
Feldspar:
64 grams of feldspar (b) requires 23 grams of whiting (a)
427 grams of feldspar (y) requires x grams of whiting (x)
x = y × (a / b) = 427 × (23 / 64) = 153.5 approximately
We would have to do a similar calculation for the kaolin as well.
Volumetric Addition to a Set
This outlines the theory behind the volumetric addition technique that was explained in Chapter 7. The formula given for that chapter applies to our standard experimental method. Any change to that method will require a re-jigging of the formula; that is explained here. Our main mathematical task is working out how much to add to each cup to achieve a certain percentage addition. Firstly we do it for 1%:
In the method used in Chapter 7, it was suggested we make a double batch if we want to end up with two sets. Therefore we start out with 600 grams of each of the 4 corner glazes. The Total Dry Weight is therefore 600 × 4 = 2400 grams.
Assume that each corner glaze was made up to an Equalizing Volume of 920ml. (The 920ml is an arbitrary figure, and we don’t actually use all of it in the blending process.) So we have a Total Wet Volume of 920 × 4 = 3680ml of glaze.
There are 35 cups with 96ml* in each, so we actually use 35 × 96ml = 3360ml Used Wet Volume.
This provides us with a means of calculating the amount of dry material in each cup using ratio or proportions. This is illustrated on the next page using either graph paper or simple maths.
Graph Method
Using a large sheet of graph paper we plot in lines representing a and b and draw in the diagonal line through the intersection. We now draw in the y- line, and project down from the diagonal line to find x, which equals approximately 2191 grams.
Maths Method
Draw a rough diagram similar to the graph on the left. Looking at the diagram, we already have a, b and y. We need to calculate x.
x = y × (a ? b)
= 3360 × (2400 ? 3680)
= 2191 grams approximately
Dry Weight in One Cup
So whether we use the graph method, or the maths method, we can now work out the dry weight in each cup:
Dry weight in One Cup = x ? 35 = 2191 ? 35 = 62.6 grams
If we divide each cup into two equal volumes then each cup will now have 31.3 grams (62.6 ? 2).
Calculating 1%
If we wish to add 1% of any material to a cup of this glaze, we would use 0.313 grams (divide 31.3 by 100).
Note that these results apply only to this example where the Equalizing Volume (E.V.) of the double batch was 920 ml.
Working out a general formula for the Dry Weight in One Cup:
If we use the standard amounts (such as 300 grams for each corner glaze, and 35 cups) then we can come up with the simplified formula that we used in Chapter 7. Even though we might be using a double batch (or a greater multiple), it is easiest understood if we use 300-gram batches.
1
x = y × (a ? b)
Used Dry Weight = Used Wet Volume × (Total Dry Weight ? Total Wet Volume) = (35 cups, each 48 ml) × (4 Corner Glazes, each 300 grams) ? (4 times the E.V.) = (35 × 48) × (4 × 300) ? (4 × E.V.) = 1680 × 1200 ? (4 × E.V.) = 504000 ? E.V. Divide this by 35 to obtain the dry weight in one cup: = 14400 ? E.V
This enables us to state a formula for a standard set:
For a Normal Batch: Dry Wt. in 1 Cup (in grams) = 14400 ÷ E.V.
For a Double Batch: If using half a “double batch”, the Equalizing Volume figure is twice as large. We must divide it by 2 before we use it in the formula above.
1
The formula for 1% of Dry Weight Addition:
2
3
**1% Addition = Dry Weight in 1 Cup ÷ 100**
Loss on Ignition - Calcining Calculations
Many materials lose weight when they are fired; something goes up the chimney! Sometimes this affects our calculations for the glaze recipe, so we need to know how to deal with it. The most direct way to measure loss on ignition (L.O.I.) is to weigh a sample, fire it and weigh it again. The weight lost represents the L.O.I.
A raw material analysis sheet typically shows a list of oxides and there is commonly an L.O.I. figure. See under “Reading Weight % Figures on a Raw Material Analysis Sheet” earlier in this section.
The L.O.I. figure is sometimes necessary for our calculations. For example…
- Wood ash and straw ash are traditional glaze materials. Depending on how they are prepared or where they are collected, there may be considerable amounts of charcoal included (sometimes over 50%). This burns out and takes no part in the glaze, so it’s weight in the recipe must be accounted for.
- If a glaze is crawling because of a high clay content, we can calcine (bisque fire) all or part of the powdered clay to stop it from shrinking and crawling. If we wish to mix up a chemically identical glaze with the calcined clay, we need to allow for the water that has been burned off in the calcining process.
Calculating L.O.I.
If the L.O.I. figure is unavailable, we can obtain our own by direct measurement:
- Take a small covered bisque fired pot and weigh it or set the tare poise so the scales are zeroed.
- With the pot still on the scales, add exactly 100 grams of test material.
- Bisque fire the lidded pot containing the test material.
- As soon as the pot and material cools, weigh it again.
- The loss of weight measured in grams indicates the L.O.I.% of the test material.
Precautions:
- Some materials absorb water from the atmosphere after calcining. For this reason the final weighing should be done promptly after the firing.
- It’s important to use a lidded pot to prevent material from jumping out and upsetting the weight calculation.
- The bisque firing should be oxidised as usual, not reduced.
- Some materials require a higher temperature to burn out, but a bisque should be adequate for our purposes.
Calcining Calculations
If we wish to replace a raw material with the same material calcined in a recipe, we need to know how to calculate the appropriate weight. The following formula will work for any material as long as we have the L.O.I.% figure:
Calcined weight = raw weight ×(100 - L.O.I.%) ÷ 100
Example - Converting a Raw Glaze to a Bisque Glaze:
Assume that a raw (once-firing) glaze contains 50% of the Australian ball clay listed earlier (L.O.I. = 9.16%), and we wish to convert this to a glaze for bisque without changing the chemistry. We do this by replacing most of the raw clay with calcined. Let’s decide to keep 15% of the ball clay raw to suspend the glaze, and the other 35% will be replaced by the appropriate amount of calcined clay.
The question becomes… How much calcined ball clay will replace 35% of raw ball clay? Substitute the figures in the formula:
Calcined weight = raw weight ×(100 - L.O.I.%) ÷ 100 = 35 × (100 - 9.16) ÷ 100 = 31.8 approx.*
Calcined Kaolin
In the special case of pure kaolin, L.O.I. is 14%. Therefore we can use this formula for kaolin:
Calcined kaolin weight = raw kaolin weight × 0.86
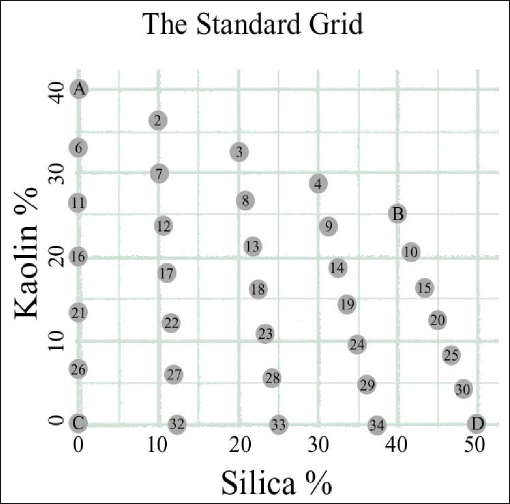
The values for kaolin and silica from the Recipe Table (see opposite) are here plotted for each glaze. We can plot a glaze recipe onto this grid and can categorize the glaze, thereby predicting some of it’s properties. For example, if it is near Corner A it is a high alumina glaze, near C it is high in fluxes, near D it will be high in silica etc. Some of the characteristics of these zones are given in Chapter 5 - A Guided tour. This works for many glaze recipes, but not so well where a glaze contains a lot of clay that is very different from kaolin or china clay.
Appendix 4 The Recipe Table and Flux Breakup Tables
1. The Recipe Table
Glaze | Total Flux Materials | Kaolin | Silica |
1 (A) | 60.00 | 40.00 | 0.00 |
2 | 53.75 | 36.25 | 10.00 |
3 | 47.50 | 32.50 | 20.00 |
4 | 41.25 | 28.75 | 30.00 |
5 (B) | 35.00 | 25.00 | 40.00 |
6 | 66.67 | 33.33 | 0.00 |
7 | 59.38 | 30.21 | 10.42 |
8 | 52.08 | 27.08 | 20.83 |
9 | 44.79 | 23.96 | 31.25 |
10 | 37.50 | 20.83 | 41.67 |
11 | 73.33 | 26.67 | 0.00 |
12 | 65.00 | 24.17 | 10.83 |
13 | 56.67 | 21.67 | 21.67 |
14 | 48.33 | 19.17 | 32.50 |
15 | 40.00 | 16.67 | 43.33 |
16 | 80.00 | 20.00 | 0.00 |
18 | 61.25 | 16.25 | 22.50 |
19 | 51.88 | 14.38 | 33.75 |
20 | 42.50 | 12.50 | 45.00 |
21 | 86.67 | 13.33 | 0.00 |
22 | 76.25 | 12.08 | 11.67 |
23 | 65.83 | 10.83 | 23.33 |
24 | 55.42 | 9.58 | 35.00 |
25 | 45.00 | 8.33 | 46.67 |
26 | 93.33 | 6.67 | 0.00 |
27 | 81.88 | 6.04 | 12.08 |
28 | 70.42 | 5.42 | 24.17 |
29 | 58.96 | 4.79 | 36.25 |
30 | 47.50 | 4.17 | 48.33 |
**31 (C) | 100.00 | 0.00 | 0.00** |
32 | 87.50 | 0.00 | 12.50 |
33 | 75.00 | 0.00 | 25.00 |
34 | 62.50 | 0.00 | 37.50 |
35 (D) | 50.00 | 0.00 | 50.00 |
2. Flux Breakup Tables
| Glaze No. | 1% | 2% | 3% | 4% | 5% | | 6% | 7% | 8% | 9% | 10% | | 1 (A) | 0.60 | 1.20 | 1.80 | 2.40 | 3.00 | | 3.60 | 4.20 | 4.80 | 5.40 | 6.00 | | 2 | 0.54 | 1.08 | 1.61 | 2.15 | 2.69 | | 3.23 | 3.76 | 4.30 | 4.84 | 5.38 | | 3 | 0.48 | 0.95 | 1.43 | 1.90 | 2.38 | | 2.85 | 3.33 | 3.80 | 4.28 | 4.75 | | 4 | 0.41 | 0.83 | 1.24 | 1.65 | 2.06 | | 2.48 | 2.89 | 3.30 | 3.71 | 4.13 | | 5(B) | 0.35 | 0.70 | 1.05 | 1.40 | 1.75 | | 2.10 | 2.45 | 2.80 | 3.15 | 3.50 | | | | | | | | | | | | | | | 6 | 0.67 | 1.33 | 2.00 | 2.67 | 3.33 | | 4.00 | 4.67 | 5.33 | 6.00 | 6.67 | | 7 | 0.59 | 1.19 | 1.78 | 2.38 | 2.97 | | 3.56 | 4.16 | 4.75 | 5.34 | 5.94 | | 8 | 0.52 | 1.04 | 1.56 | 2.08 | 2.60 | | 3.13 | 3.65 | 4.17 | 4.69 | 5.21 | | 9 | 0.45 | 0.90 | 1.34 | 1.79 | 2.24 | | 2.69 | 3.14 | 3.58 | 4.03 | 4.48 | | 10 | 0.38 | 0.75 | 1.13 | 1.50 | 1.88 | | 2.25 | 2.63 | 3.00 | 3.38 | 3.75 | | | | | | | | | | | | | | | 11 | 0.73 | 1.47 | 2.20 | 2.93 | 3.67 | | 4.40 | 5.13 | 5.87 | 6.60 | 7.33 | | 12 | 0.65 | 1.30 | 1.95 | 2.60 | 3.25 | | 3.90 | 4.55 | 5.20 | 5.85 | 6.50 | | 13 | 0.57 | 1.13 | 1.70 | 2.27 | 2.83 | | 3.40 | 3.97 | 4.53 | 5.10 | 5.67 | | 14 | 0.48 | 0.97 | 1.45 | 1.93 | 2.42 | | 2.90 | 3.38 | 3.87 | 4.35 | 4.83 | | 15 | 0.40 | 0.80 | 1.20 | 1.60 | 2.00 | | 2.40 | 2.80 | 3.20 | 3.60 | 4.00 | | | | | | | | | | | | | | | 16 | 0.80 | 1.60 | 2.40 | 3.20 | 4.00 | | 4.80 | 5.60 | 6.40 | 7.20 | 8.00 | | 17 | 0.71 | 1.41 | 2.12 | 2.83 | 3.53 | | 4.24 | 4.94 | 5.65 | 6.36 | 7.06 | | 18 | 0.61 | 1.23 | 1.84 | 2.45 | 3.06 | | 3.68 | 4.29 | 4.90 | 5.51 | 6.13 | | 19 | 0.52 | 1.04 | 1.56 | 2.08 | 2.59 | | 3.11 | 3.63 | 4.15 | 4.67 | 5.19 | | 20 | 0.43 | 0.85 | 1.28 | 1.70 | 2.13 | | 2.55 | 2.98 | 3.40 | 3.83 | 4.25 | | | | | | | | | | | | | | | 21 | 0.87 | 1.73 | 2.60 | 3.47 | 4.33 | | 5.20 | 6.07 | 6.93 | 7.80 | 8.67 | | 22 | 0.76 | 1.53 | 2.29 | 3.05 | 3.81 | | 4.58 | 5.34 | 6.10 | 6.86 | 7.63 | | 23 | 0.66 | 1.32 | 1.98 | 2.63 | 3.29 | | 3.95 | 4.61 | 5.27 | 5.93 | 6.58 | | 24 | 0.55 | 1.11 | 1.66 | 2.22 | 2.77 | | 3.33 | 3.88 | 4.43 | 4.99 | 5.54 | | 25 | 0.45 | 0.90 | 1.35 | 1.80 | 2.25 | | 2.70 | 3.15 | 3.60 | 4.05 | 4.50 | | | | | | | | | | | | | | | 26 | 0.93 | 1.87 | 2.80 | 3.73 | 4.67 | | 5.60 | 6.53 | 7.47 | 8.40 | 9.33 | | 27 | 0.82 | 1.64 | 2.46 | 3.28 | 4.09 | | 4.91 | 5.73 | 6.55 | 7.37 | 8.19 | | 28 | 0.70 | 1.41 | 2.11 | 2.82 | 3.52 | | 4.23 | 4.93 | 5.63 | 6.34 | 7.04 | | 29 | 0.59 | 1.18 | 1.77 | 2.36 | 2.95 | | 3.54 | 4.13 | 4.72 | 5.31 | 5.90 | | 30 | 0.48 | 0.95 | 1.43 | 1.90 | 2.38 | | 2.85 | 3.33 | 3.80 | 4.28 | 4.75 | | | | | | | | | | | | | | | **31 (C) | 1.00 | 2.00 | 3.00 | 4.00 | 5.00 | | 6.00 | 7.00 | 8.00 | 9.00 | 10.00 **| | 32 | 0.88 | 1.75 | 2.63 | 3.50 | 4.38 | | 5.25 | 6.13 | 7.00 | 7.88 | 8.75 | | 33 | 0.75 | 1.50 | 2.25 | 3.00 | 3.75 | | 4.50 | 5.25 | 6.00 | 6.75 | 7.50 | | 34 | 0.63 | 1.25 | 1.88 | 2.50 | 3.13 | | 3.75 | 4.38 | 5.00 | 5.63 | 6.25 | | 35 (D) | 0.50 | 1.00 | 1.50 | 2.00 | 2.50 | | 3.00 | 3.50 | 4.00 | 4.50 | 5.00 |
Flux Breakup Tables continued…
| Glaze No. | 11% | 12% | 13% | 14% | 15% | | 16% | 17% | 18% | |19% |20% | | 1 (A) | 6.60 | 7.20 | 7.80 | 8.40 | 9.00 | | 9.60 | 10.20 | 10.80 | 11.40 | 12.00 | | 2 | 5.91 | 6.45 | 6.99 | 7.53 | 8.06 | | 8.60 | 9.14 | 9.68 | 10.21 | 10.75 | | 3 | 5.23 | 5.70 | 6.18 | 6.65 | 7.13 | | 7.60 | 8.08 | 8.55 | 9.03 | 9.50 | | 4 | 4.54 | 4.95 | 5.36 | 5.78 | 6.19 | | 6.60 | 7.01 | 7.43 | 7.84 | 8.25 | | 5 (B) | 3.85 | 4.20 | 4.55 | 4.90 | 5.25 | | 5.60 | 5.95 | 6.30 | 6.65 | 7.00 | | | | | | | | | | | | | | | 6 | 7.33 | 8.00 | 8.67 | 9.33 | 10.00 | | 10.67 | 11.33 | 12.00 | 12.67 | 13.33 | | 7 | 6.53 | 7.13 | 7.72 | 8.31 | 8.91 | | 9.50 | 10.09 | 10.69 | 11.28 | 11.88 | | 8 | 5.73 | 6.25 | 6.77 | 7.29 | 7.81 | | 8.33 | 8.85 | 9.38 | 9.90 | 10.42 | | 9 | 4.93 | 5.38 | 5.82 | 6.27 | 6.72 | | 7.17 | 7.61 | 8.06 | 8.51 | 8.96 | | 10 | 4.13 | 4.50 | 4.88 | 5.25 | 5.63 | | 6.00 | 6.38 | 6.75 | 7.13 | 7.50 | | | | | | | | | | | | | | | 11 | 8.07 | 8.80 | 9.53 | 10.27 | 11.00 | | 11.73 | 12.47 | 13.20 | 13.93 | 14.67 | | 12 | 7.15 | 7.80 | 8.45 | 9.10 | 9.75 | | 10.40 | 11.05 | 11.70 | 12.35 | 13.00 | | 13 | 6.23 | 6.80 | 7.37 | 7.93 | 8.50 | | 9.07 | 9.63 | 10.20 | 10.77 | 11.33 | | 14 | 5.32 | 5.80 | 6.28 | 6.77 | 7.25 | | 7.73 | 8.22 | 8.70 | 9.18 | 9.67 | | 15 | 4.40 | 4.80 | 5.20 | 5.60 | 6.00 | | 6.40 | 6.80 | 7.20 | 7.60 | 8.00 | | | | | | | | | | | | | | | 16 | 8.80 | 9.60 | 10.40 | 11.20 | 12.00 | | 12.80 | 13.60 | 14.40 | 15.20 | 16.00 | | 17 | 7.77 | 8.48 | 9.18 | 9.89 | 10.59 | | 11.30 | 12.01 | 12.71 | 13.42 | 14.13 | | 18 | 6.74 | 7.35 | 7.96 | 8.58 | 9.19 | | 9.80 | 10.41 | 11.03 | 11.64 | 12.25 | | 19 | 5.71 | 6.23 | 6.74 | 7.26 | 7.78 | | 8.30 | 8.82 | 9.34 | 9.86 | 10.38 | | 20 | 4.68 | 5.10 | 5.53 | 5.95 | 6.38 | | 6.80 | 7.23 | 7.65 | 8.08 | 8.50 | | | | | | | | | | | | | | | 21 | 9.53 | 10.40 | 11.27 | 12.13 | 13.00 | | 13.87 | 14.73 | 15.60 | 16.47 | 17.33 | | 22 | 8.39 | 9.15 | 9.91 | 10.68 | 11.44 | | 12.20 | 12.96 | 13.73 | 14.49 | 15.25 | | 23 | 7.24 | 7.90 | 8.56 | 9.22 | 9.88 | | 10.53 | 11.19 | 11.85 | 12.51 | 13.17 | | 24 | 6.10 | 6.65 | 7.20 | 7.76 | 8.31 | | 8.87 | 9.42 | 9.98 | 10.53 | 11.08 | | 25 | 4.95 | 5.40 | 5.85 | 6.30 | 6.75 | | 7.20 | 7.65 | 8.10 | 8.55 | 9.00 | | | | | | | | | | | | | | | 26 | 10.27 | 11.20 | 12.13 | 13.07 | 14.00 | | 14.93 | 15.87 | 16.80 | 17.73 | 18.67 | | 27 | 9.01 | 9.83 | 10.64 | 11.46 | 12.28 | | 13.10 | 13.92 | 14.74 | 15.56 | 16.38 | | 28 | 7.75 | 8.45 | 9.15 | 9.86 | 10.56 | | 11.27 | 11.97 | 12.68 | 13.38 | 14.08 | | 29 | 6.49 | 7.08 | 7.66 | 8.25 | 8.84 | | 9.43 | 10.02 | 10.61 | 11.20 | 11.79 | | 30 | 5.23 | 5.70 | 6.18 | 6.65 | 7.13 | | 7.60 | 8.08 | 8.55 | 9.03 | 9.50 | | | | | | | | | | | | | | | **31 (C) | 11.00 | 12.00 | 13.00 | 14.00 | 15.00 | | 16.00 | 17.00 | 18.00 | 19.00 | 20.00 **| | 32 | 9.63 | 10.50 | 11.38 | 12.25 | 13.13 | | 14.00 | 14.88 | 15.75 | 16.63 | 17.50 | | 33 | 8.25 | 9.00 | 9.75 | 10.50 | 11.25 | | 12.00 | 12.75 | 13.50 | 14.25 | 15.00 | | 34 | 6.88 | 7.50 | 8.13 | 8.75 | 9.38 | | 10.00 | 10.63 | 11.25 | 11.88 | 12.50 | | 35 (D) | 5.50 | 6.00 | 6.50 | 7.00 | 7.50 | | 8.00 | 8.50 | 9.00 | 9.50 | 10.00 |
Flux Breakup Tables continued…
| Glaze No. | 21% | 22% | 23% | 24% | 25% | | 26% | 27% | 28% | |29% |30% | | 1 (A) | 12.60 | 13.20 | 13.80 | 14.40 | 15.00 | | 15.60 | 16.20 | 16.80 | 17.40 | 18.00 | | 2 | 11.29 | 11.83 | 12.36 | 12.90 | 13.44 | | 13.98 | 14.51 | 15.05 | 15.59 | 16.13 | | 3 | 9.98 | 10.45 | 10.93 | 11.40 | 11.88 | | 12.35 | 12.83 | 13.30 | 13.78 | 14.25 | | 4 | 8.66 | 9.08 | 9.49 | 9.90 | 10.31 | | 10.73 | 11.14 | 11.55 | 11.96 | 12.38 | | 5 (B) | 7.35 | 7.70 | 8.05 | 8.40 | 8.75 | | 9.10 | 9.45 | 9.80 | 10.15 | 10.50 | | | | | | | | | | | | | | | 6 | 14.00 | 14.67 | 15.33 | 16.00 | 16.67 | | 17.33 | 18.00 | 18.67 | 19.33 | 20.00 | | 7 | 12.47 | 13.06 | 13.66 | 14.25 | 14.84 | | 15.44 | 16.03 | 16.63 | 17.22 | 17.81 | | 8 | 10.94 | 11.46 | 11.98 | 12.50 | 13.02 | | 13.54 | 14.06 | 14.58 | 15.10 | 15.63 | | 9 | 9.41 | 9.85 | 10.30 | 10.75 | 11.20 | | 11.65 | 12.09 | 12.54 | 12.99 | 13.44 | | 10 | 7.88 | 8.25 | 8.63 | 9.00 | 9.38 | | 9.75 | 10.13 | 10.50 | 10.88 | 11.25 | | | | | | | | | | | | | | | 11 | 15.40 | 16.13 | 16.87 | 17.60 | 18.33 | | 19.07 | 19.80 | 20.53 | 21.27 | 22.00 | | 12 | 13.65 | 14.30 | 14.95 | 15.60 | 16.25 | | 16.90 | 17.55 | 18.20 | 18.85 | 19.50 | | 13 | 11.90 | 12.47 | 13.03 | 13.60 | 14.17 | | 14.73 | 15.30 | 15.87 | 16.43 | 17.00 | | 14 | 10.15 | 10.63 | 11.12 | 11.60 | 12.08 | | 12.57 | 13.05 | 13.53 | 14.02 | 14.50 | | 15 | 8.40 | 8.80 | 9.20 | 9.60 | 10.00 | | 10.40 | 10.80 | 11.20 | 11.60 | 12.00 | | | | | | | | | | | | | | | 16 | 16.80 | 17.60 | 18.40 | 19.20 | 20.00 | | 20.80 | 21.60 | 22.40 | 23.20 | 24.00 | | 17 | 14.83 | 15.54 | 16.24 | 16.95 | 17.66 | | 18.36 | 19.07 | 19.78 | 20.48 | 21.19 | | 18 | 12.86 | 13.48 | 14.09 | 14.70 | 15.31 | | 15.93 | 16.54 | 17.15 | 17.76 | 18.38 | | 19 | 10.89 | 11.41 | 11.93 | 12.45 | 12.97 | | 13.49 | 14.01 | 14.53 | 15.04 | 15.56 | | 20 | 8.93 | 9.35 | 9.78 | 10.20 | 10.63 | | 11.05 | 11.48 | 11.90 | 12.33 | 12.75 | | | | | | | | | | | | | | | 21 | 18.20 | 19.07 | 19.93 | 20.80 | 21.67 | | 22.53 | 23.40 | 24.27 | 25.13 | 26.00 | | 22 | 16.01 | 16.78 | 17.54 | 18.30 | 19.06 | | 19.83 | 20.59 | 21.35 | 22.11 | 22.88 | | 23 | 13.83 | 14.48 | 15.14 | 15.80 | 16.46 | | 17.12 | 17.78 | 18.43 | 19.09 | 19.75 | | 24 | 11.64 | 12.19 | 12.75 | 13.30 | 13.85 | | 14.41 | 14.96 | 15.52 | 16.07 | 16.63 | | 25 | 9.45 | 9.90 | 10.35 | 10.80 | 11.25 | | 11.70 | 12.15 | 12.60 | 13.05 | 13.50 | | | | | | | | | | | | | | | 26 | 19.60 | 20.53 | 21.47 | 22.40 | 23.33 | | 24.27 | 25.20 | 26.13 | 27.07 | 28.00 | | 27 | 17.19 | 18.01 | 18.83 | 19.65 | 20.47 | | 21.29 | 22.11 | 22.93 | 23.74 | 24.56 | | 28 | 14.79 | 15.49 | 16.20 | 16.90 | 17.60 | | 18.31 | 19.01 | 19.72 | 20.42 | 21.13 | | 29 | 12.38 | 12.97 | 13.56 | 14.15 | 14.74 | | 15.33 | 15.92 | 16.51 | 17.10 | 17.69 | | 30 | 9.98 | 10.45 | 10.93 | 11.40 | 11.88 | | 12.35 | 12.83 | 13.30 | 13.78 | 14.25 | | | | | | | | | | | | | | | **31 (C) | 21.00 | 22.00 | 23.00 | 24.00 | 25.00 | | 26.00 | 27.00 | 28.00 | 29.00 | 30.00 **| | 32 | 18.38 | 19.25 | 20.13 | 21.00 | 21.88 | | 22.75 | 23.63 | 24.50 | 25.38 | 26.25 | | 33 | 15.75 | 16.50 | 17.25 | 18.00 | 18.75 | | 19.50 | 20.25 | 21.00 | 21.75 | 22.50 | | 34 | 13.13 | 13.75 | 14.38 | 15.00 | 15.63 | | 16.25 | 16.88 | 17.50 | 18.13 | 18.75 | | 35 (D) | 10.50 | 11.00 | 11.50 | 12.00 | 12.50 | | 13.00 | 13.50 | 14.00 | 14.50 | 15.00 |
Flux Breakup Tables continued…
| Glaze No. | 31% | 32% | 33% | 34% | 35% | | 36% | 37% | 38% | |39% |40% | | 1 (A) | 18.60 | 19.20 | 19.80 | 20.40 | 21.00 | | 21.60 | 22.20 | 22.80 | 23.40 | 24.00 | | 2 | 16.66 | 17.20 | 17.74 | 18.28 | 18.81 | | 19.35 | 19.89 | 20.43 | 20.96 | 21.50 | | 3 | 14.73 | 15.20 | 15.68 | 16.15 | 16.63 | | 17.10 | 17.58 | 18.05 | 18.53 | 19.00 | | 4 | 12.79 | 13.20 | 13.61 | 14.03 | 14.44 | | 14.85 | 15.26 | 15.68 | 16.09 | 16.50 | | 5 (B) | 10.85 | 11.20 | 11.55 | 11.90 | 12.25 | | 12.60 | 12.95 | 13.30 | 13.65 | 14.00 | | | | | | | | | | | | | | | 6 | 20.67 | 21.33 | 22.00 | 22.67 | 23.33 | | 24.00 | 24.67 | 25.33 | 26.00 | 26.67 | | 7 | 18.41 | 19.00 | 19.59 | 20.19 | 20.78 | | 21.38 | 21.97 | 22.56 | 23.16 | 23.75 | | 8 | 16.15 | 16.67 | 17.19 | 17.71 | 18.23 | | 18.75 | 19.27 | 19.79 | 20.31 | 20.83 | | 9 | 13.89 | 14.33 | 14.78 | 15.23 | 15.68 | | 16.13 | 16.57 | 17.02 | 17.47 | 17.92 | | 10 | 11.63 | 12.00 | 12.38 | 12.75 | 13.13 | | 13.50 | 13.88 | 14.25 | 14.63 | 15.00 | | | | | | | | | | | | | | | 11 | 22.73 | 23.47 | 24.20 | 24.93 | 25.67 | | 26.40 | 27.13 | 27.87 | 28.60 | 29.33 | | 12 | 20.15 | 20.80 | 21.45 | 22.10 | 22.75 | | 23.40 | 24.05 | 24.70 | 25.35 | 26.00 | | 13 | 17.57 | 18.13 | 18.70 | 19.27 | 19.83 | | 20.40 | 20.97 | 21.53 | 22.10 | 22.67 | | 14 | 14.98 | 15.47 | 15.95 | 16.43 | 16.92 | | 17.40 | 17.88 | 18.37 | 18.85 | 19.33 | | 15 | 12.40 | 12.80 | 13.20 | 13.60 | 14.00 | | 14.40 | 14.80 | 15.20 | 15.60 | 16.00 | | | | | | | | | | | | | | | 16 | 24.80 | 25.60 | 26.40 | 27.20 | 28.00 | | 28.80 | 29.60 | 30.40 | 31.20 | 32.00 | | 17 | 21.89 | 22.60 | 23.31 | 24.01 | 24.72 | | 25.43 | 26.13 | 26.84 | 27.54 | 28.25 | | 18 | 18.99 | 19.60 | 20.21 | 20.83 | 21.44 | | 22.05 | 22.66 | 23.28 | 23.89 | 24.50 | | 19 | 16.08 | 16.60 | 17.12 | 17.64 | 18.16 | | 18.68 | 19.19 | 19.71 | 20.23 | 20.75 | | 20 | 13.18 | 13.60 | 14.03 | 14.45 | 14.88 | | 15.30 | 15.73 | 16.15 | 16.58 | 17.00 | | | | | | | | | | | | | | | 21 | 26.87 | 27.73 | 28.60 | 29.47 | 30.33 | | 31.20 | 32.07 | 32.93 | 33.80 | 34.67 | | 22 | 23.64 | 24.40 | 25.16 | 25.93 | 26.69 | | 27.45 | 28.21 | 28.98 | 29.74 | 30.50 | | 23 | 20.41 | 21.07 | 21.73 | 22.38 | 23.04 | | 23.70 | 24.36 | 25.02 | 25.68 | 26.33 | | 24 | 17.18 | 17.73 | 18.29 | 18.84 | 19.40 | | 19.95 | 20.50 | 21.06 | 21.61 | 22.17 | | 25 | 13.95 | 14.40 | 14.85 | 15.30 | 15.75 | | 16.20 | 16.65 | 17.10 | 17.55 | 18.00 | | | | | | | | | | | | | | | 26 | 28.93 | 29.87 | 30.80 | 31.73 | 32.67 | | 33.60 | 34.53 | 35.47 | 36.40 | 37.33 | | 27 | 25.38 | 26.20 | 27.02 | 27.84 | 28.66 | | 29.48 | 30.29 | 31.11 | 31.93 | 32.75 | | 28 | 21.83 | 22.53 | 23.24 | 23.94 | 24.65 | | 25.35 | 26.05 | 26.76 | 27.46 | 28.17 | | 29 | 18.28 | 18.87 | 19.46 | 20.05 | 20.64 | | 21.23 | 21.81 | 22.40 | 22.99 | 23.58 | | 30 | 14.73 | 15.20 | 15.68 | 16.15 | 16.63 | | 17.10 | 17.58 | 18.05 | 18.53 | 19.00 | | | | | | | | | | | | | | | **31 (C) | 31.00 | 32.00 | 33.00 | 34.00 | 35.00 | | 36.00 | 37.00 | 38.00 | 39.00 | 40.00 **| | 32 | 27.13 | 28.00 | 28.88 | 29.75 | 30.63 | | 31.50 | 32.38 | 33.25 | 34.13 | 35.00 | | 33 | 23.25 | 24.00 | 24.75 | 25.50 | 26.25 | | 27.00 | 27.75 | 28.50 | 29.25 | 30.00 | | 34 | 19.38 | 20.00 | 20.63 | 21.25 | 21.88 | | 22.50 | 23.13 | 23.75 | 24.38 | 25.00 | | 35 (D) | 15.50 | 16.00 | 16.50 | 17.00 | 17.50 | | 18.00 | 18.50 | 19.00 | 19.50 | 20.00 |
Flux Breakup Tables continued…
| Glaze No. | 41% | 42% | 43% | 44% | 45% | | 46% | 47% | 48% | | 49% | 50% | | 1 (A) | 24.60 | 25.20 | 25.80 | 26.40 | 27.00 | | 27.60 | 28.20 | 28.80 | 29.40 | 30.00 | | 2 | 22.04 | 22.58 | 23.11 | 23.65 | 24.19 | | 24.73 | 25.26 | 25.80 | 26.34 | 26.88 | | 3 | 19.48 | 19.95 | 20.43 | 20.90 | 21.38 | | 21.85 | 22.33 | 22.80 | 23.28 | 23.75 | | 4 | 16.91 | 17.33 | 17.74 | 18.15 | 18.56 | | 18.98 | 19.39 | 19.80 | 20.21 | 20.63 | | 5 (B) | 14.35 | 14.70 | 15.05 | 15.40 | 15.75 | | 16.10 | 16.45 | 16.80 | 17.15 | 17.50 | | | | | | | | | | | | | | | 6 | 27.33 | 28.00 | 28.67 | 29.33 | 30.00 | | 30.67 | 31.33 | 32.00 | 32.67 | 33.33 | | 7 | 24.34 | 24.94 | 25.53 | 26.13 | 26.72 | | 27.31 | 27.91 | 28.50 | 29.09 | 29.69 | | 8 | 21.35 | 21.88 | 22.40 | 22.92 | 23.44 | | 23.96 | 24.48 | 25.00 | 25.52 | 26.04 | | 9 | 18.36 | 18.81 | 19.26 | 19.71 | 20.16 | | 20.60 | 21.05 | 21.50 | 21.95 | 22.40 | | 10 | 15.38 | 15.75 | 16.13 | 16.50 | 16.88 | | 17.25 | 17.63 | 18.00 | 18.38 | 18.75 | | | | | | | | | | | | | | | 11 | 30.07 | 30.80 | 31.53 | 32.27 | 33.00 | | 33.73 | 34.47 | 35.20 | 35.93 | 36.67 | | 12 | 26.65 | 27.30 | 27.95 | 28.60 | 29.25 | | 29.90 | 30.55 | 31.20 | 31.85 | 32.50 | | 13 | 23.23 | 23.80 | 24.37 | 24.93 | 25.50 | | 26.07 | 26.63 | 27.20 | 27.77 | 28.33 | | 14 | 19.82 | 20.30 | 20.78 | 21.27 | 21.75 | | 22.23 | 22.72 | 23.20 | 23.68 | 24.17 | | 15 | 16.40 | 16.80 | 17.20 | 17.60 | 18.00 | | 18.40 | 18.80 | 19.20 | 19.60 | 20.00 | | | | | | | | | | | | | | | 16 | 32.80 | 33.60 | 34.40 | 35.20 | 36.00 | | 36.80 | 37.60 | 38.40 | 39.20 | 40.00 | | 17 | 28.96 | 29.66 | 30.37 | 31.08 | 31.78 | | 32.49 | 33.19 | 33.90 | 34.61 | 35.31 | | 18 | 25.11 | 25.73 | 26.34 | 26.95 | 27.56 | | 28.18 | 28.79 | 29.40 | 30.01 | 30.63 | | 19 | 21.27 | 21.79 | 22.31 | 22.83 | 23.34 | | 23.86 | 24.38 | 24.90 | 25.42 | 25.94 | | 20 | 17.43 | 17.85 | 18.28 | 18.70 | 19.13 | | 19.55 | 19.98 | 20.40 | 20.83 | 21.25 | | | | | | | | | | | | | | | 21 | 35.53 | 36.40 | 37.27 | 38.13 | 39.00 | | 39.87 | 40.73 | 41.60 | 42.47 | 43.33 | | 22 | 31.26 | 32.03 | 32.79 | 33.55 | 34.31 | | 35.08 | 35.84 | 36.60 | 37.36 | 38.13 | | 23 | 26.99 | 27.65 | 28.31 | 28.97 | 29.63 | | 30.28 | 30.94 | 31.60 | 32.26 | 32.92 | | 24 | 22.72 | 23.28 | 23.83 | 24.38 | 24.94 | | 25.49 | 26.05 | 26.60 | 27.15 | 27.71 | | 25 | 18.45 | 18.90 | 19.35 | 19.80 | 20.25 | | 20.70 | 21.15 | 21.60 | 22.05 | 22.50 | | | | | | | | | | | | | | | 26 | 38.27 | 39.20 | 40.13 | 41.07 | 42.00 | | 42.93 | 43.87 | 44.80 | 45.73 | 46.67 | | 27 | 33.57 | 34.39 | 35.21 | 36.03 | 36.84 | | 37.66 | 38.48 | 39.30 | 40.12 | 40.94 | | 28 | 28.87 | 29.58 | 30.28 | 30.98 | 31.69 | | 32.39 | 33.10 | 33.80 | 34.50 | 35.21 | | 29 | 24.17 | 24.76 | 25.35 | 25.94 | 26.53 | | 27.12 | 27.71 | 28.30 | 28.89 | 29.48 | | 30 | 19.48 | 19.95 | 20.43 | 20.90 | 21.38 | | 21.85 | 22.33 | 22.80 | 23.28 | 23.75 | | | | | | | | | | | | | | | **31 (C) | 41.00 | 42.00 | 43.00 | 44.00 | 45.00 | | 46.00 | 47.00 | 48.00 | 49.00 | 50.00 **| | 32 | 35.88 | 36.75 | 37.63 | 38.50 | 39.38 | | 40.25 | 41.13 | 42.00 | 42.88 | 43.75 | | 33 | 30.75 | 31.50 | 32.25 | 33.00 | 33.75 | | 34.50 | 35.25 | 36.00 | 36.75 | 37.50 | | 34 | 25.63 | 26.25 | 26.88 | 27.50 | 28.13 | | 28.75 | 29.38 | 30.00 | 30.63 | 31.25 | | 35 (D) | 20.50 | 21.00 | 21.50 | 22.00 | 22.50 | | 23.00 | 23.50 | 24.00 | 24.50 | 25.00 |
Flux Breakup Tables continued…
| Glaze No. | 51% | 52% | 53% | 54% | 55% | | 56% | 57% | 58% | | 59% | 60% | | 1 (A) | 30.60 | 31.20 | 31.80 | 32.40 | 33.00 | | 33.60 | 34.20 | 34.80 | 35.40 | 36.00 | | 2 | 27.41 | 27.95 | 28.49 | 29.03 | 29.56 | | 30.10 | 30.64 | 31.18 | 31.71 | 32.25 | | 3 | 24.23 | 24.70 | 25.18 | 25.65 | 26.13 | | 26.60 | 27.08 | 27.55 | 28.03 | 28.50 | | 4 | 21.04 | 21.45 | 21.86 | 22.28 | 22.69 | | 23.10 | 23.51 | 23.93 | 24.34 | 24.75 | | 5 (B) | 17.85 | 18.20 | 18.55 | 18.90 | 19.25 | | 19.60 | 19.95 | 20.30 | 20.65 | 21.00 | | | | | | | | | | | | | | | 6 | 34.00 | 34.67 | 35.33 | 36.00 | 36.67 | | 37.33 | 38.00 | 38.67 | 39.33 | 40.00 | | 7 | 30.28 | 30.88 | 31.47 | 32.06 | 32.66 | | 33.25 | 33.84 | 34.44 | 35.03 | 35.63 | | 8 | 26.56 | 27.08 | 27.60 | 28.13 | 28.65 | | 29.17 | 29.69 | 30.21 | 30.73 | 31.25 | | 9 | 22.84 | 23.29 | 23.74 | 24.19 | 24.64 | | 25.08 | 25.53 | 25.98 | 26.43 | 26.88 | | 10 | 19.13 | 19.50 | 19.88 | 20.25 | 20.63 | | 21.00 | 21.38 | 21.75 | 22.13 | 22.50 | | | | | | | | | | | | | | | 11 | 37.40 | 38.13 | 38.87 | 39.60 | 40.33 | | 41.07 | 41.80 | 42.53 | 43.27 | 44.00 | | 12 | 33.15 | 33.80 | 34.45 | 35.10 | 35.75 | | 36.40 | 37.05 | 37.70 | 38.35 | 39.00 | | 13 | 28.90 | 29.47 | 30.03 | 30.60 | 31.17 | | 31.73 | 32.30 | 32.87 | 33.43 | 34.00 | | 14 | 24.65 | 25.13 | 25.62 | 26.10 | 26.58 | | 27.07 | 27.55 | 28.03 | 28.52 | 29.00 | | 15 | 20.40 | 20.80 | 21.20 | 21.60 | 22.00 | | 22.40 | 22.80 | 23.20 | 23.60 | 24.00 | | | | | | | | | | | | | | | 16 | 40.80 | 41.60 | 42.40 | 43.20 | 44.00 | | 44.80 | 45.60 | 46.40 | 47.20 | 48.00 | | 17 | 36.02 | 36.73 | 37.43 | 38.14 | 38.84 | | 39.55 | 40.26 | 40.96 | 41.67 | 42.38 | | 18 | 31.24 | 31.85 | 32.46 | 33.08 | 33.69 | | 34.30 | 34.91 | 35.53 | 36.14 | 36.75 | | 19 | 26.46 | 26.98 | 27.49 | 28.01 | 28.53 | | 29.05 | 29.57 | 30.09 | 30.61 | 31.13 | | 20 | 21.68 | 22.10 | 22.53 | 22.95 | 23.38 | | 23.80 | 24.23 | 24.65 | 25.08 | 25.50 | | | | | | | | | | | | | | | 21 | 44.20 | 45.07 | 45.93 | 46.80 | 47.67 | | 48.53 | 49.40 | 50.27 | 51.13 | 52.00 | | 22 | 38.89 | 39.65 | 40.41 | 41.18 | 41.94 | | 42.70 | 43.46 | 44.23 | 44.99 | 45.75 | | 23 | 33.58 | 34.23 | 34.89 | 35.55 | 36.21 | | 36.87 | 37.53 | 38.18 | 38.84 | 39.50 | | 24 | 28.26 | 28.82 | 29.37 | 29.93 | 30.48 | | 31.03 | 31.59 | 32.14 | 32.70 | 33.25 | | 25 | 22.95 | 23.40 | 23.85 | 24.30 | 24.75 | | 25.20 | 25.65 | 26.10 | 26.55 | 27.00 | | | | | | | | | | | | | | | 26 | 47.60 | 48.53 | 49.47 | 50.40 | 51.33 | | 52.27 | 53.20 | 54.13 | 55.07 | 56.00 | | 27 | 41.76 | 42.58 | 43.39 | 44.21 | 45.03 | | 45.85 | 46.67 | 47.49 | 48.31 | 49.13 | | 28 | 35.91 | 36.62 | 37.32 | 38.03 | 38.73 | | 39.43 | 40.14 | 40.84 | 41.55 | 42.25 | | 29 | 30.07 | 30.66 | 31.25 | 31.84 | 32.43 | | 33.02 | 33.61 | 34.20 | 34.79 | 35.38 | | 30 | 24.23 | 24.70 | 25.18 | 25.65 | 26.13 | | 26.60 | 27.08 | 27.55 | 28.03 | 28.50 | | | | | | | | | | | | | | | **31 (C) | 51.00 | 52.00 | 53.00 | 54.00 | 55.00 | | 56.00 | 57.00 | 58.00 | 59.00 | 60.00 **| | 32 | 44.63 | 45.50 | 46.38 | 47.25 | 48.13 | | 49.00 | 49.88 | 50.75 | 51.63 | 52.50 | | 33 | 38.25 | 39.00 | 39.75 | 40.50 | 41.25 | | 42.00 | 42.75 | 43.50 | 44.25 | 45.00 | | 34 | 31.88 | 32.50 | 33.13 | 33.75 | 34.38 | | 35.00 | 35.63 | 36.25 | 36.88 | 37.50 | | 35 (D) | 25.50 | 26.00 | 26.50 | 27.00 | 27.50 | | 28.00 | 28.50 | 29.00 | 29.50 | 30.00 |
Flux Breakup Tables continued…
| Glaze No. | 61% | 62% | 63% | 64% | 65% | | 66% | 67% | 68% | | 69% | 70% | | 1 (A) | 36.60 | 37.20 | 37.80 | 38.40 | 39.00 | | 39.60 | 40.20 | 40.80 | 41.40 | 42.00 | | 2 | 32.79 | 33.33 | 33.86 | 34.40 | 34.94 | | 35.48 | 36.01 | 36.55 | 37.09 | 37.63 | | 3 | 28.98 | 29.45 | 29.93 | 30.40 | 30.88 | | 31.35 | 31.83 | 32.30 | 32.78 | 33.25 | | 4 | 25.16 | 25.58 | 25.99 | 26.40 | 26.81 | | 27.23 | 27.64 | 28.05 | 28.46 | 28.88 | | 5 (B) | 21.35 | 21.70 | 22.05 | 22.40 | 22.75 | | 23.10 | 23.45 | 23.80 | 24.15 | 24.50 | | | | | | | | | | | | | | | 6 | 40.67 | 41.33 | 42.00 | 42.67 | 43.33 | | 44.00 | 44.67 | 45.33 | 46.00 | 46.67 | | 7 | 36.22 | 36.81 | 37.41 | 38.00 | 38.59 | | 39.19 | 39.78 | 40.38 | 40.97 | 41.56 | | 8 | 31.77 | 32.29 | 32.81 | 33.33 | 33.85 | | 34.38 | 34.90 | 35.42 | 35.94 | 36.46 | | 9 | 27.32 | 27.77 | 28.22 | 28.67 | 29.11 | | 29.56 | 30.01 | 30.46 | 30.91 | 31.35 | | 10 | 22.88 | 23.25 | 23.63 | 24.00 | 24.38 | | 24.75 | 25.13 | 25.50 | 25.88 | 26.25 | | | | | | | | | | | | | | | 11 | 44.73 | 45.47 | 46.20 | 46.93 | 47.67 | | 48.40 | 49.13 | 49.87 | 50.60 | 51.33 | | 12 | 39.65 | 40.30 | 40.95 | 41.60 | 42.25 | | 42.90 | 43.55 | 44.20 | 44.85 | 45.50 | | 13 | 34.57 | 35.13 | 35.70 | 36.27 | 36.83 | | 37.40 | 37.97 | 38.53 | 39.10 | 39.67 | | 14 | 29.48 | 29.97 | 30.45 | 30.93 | 31.42 | | 31.90 | 32.38 | 32.87 | 33.35 | 33.83 | | 15 | 24.40 | 24.80 | 25.20 | 25.60 | 26.00 | | 26.40 | 26.80 | 27.20 | 27.60 | 28.00 | | | | | | | | | | | | | | | 16 | 48.80 | 49.60 | 50.40 | 51.20 | 52.00 | | 52.80 | 53.60 | 54.40 | 55.20 | 56.00 | | 17 | 43.08 | 43.79 | 44.49 | 45.20 | 45.91 | | 46.61 | 47.32 | 48.03 | 48.73 | 49.44 | | 18 | 37.36 | 37.98 | 38.59 | 39.20 | 39.81 | | 40.43 | 41.04 | 41.65 | 42.26 | 42.88 | | 19 | 31.64 | 32.16 | 32.68 | 33.20 | 33.72 | | 34.24 | 34.76 | 35.28 | 35.79 | 36.31 | | 20 | 25.93 | 26.35 | 26.78 | 27.20 | 27.63 | | 28.05 | 28.48 | 28.90 | 29.33 | 29.75 | | | | | | | | | | | | | | | 21 | 52.87 | 53.73 | 54.60 | 55.47 | 56.33 | | 57.20 | 58.07 | 58.93 | 59.80 | 60.67 | | 22 | 46.51 | 47.28 | 48.04 | 48.80 | 49.56 | | 50.33 | 51.09 | 51.85 | 52.61 | 53.38 | | 23 | 40.16 | 40.82 | 41.48 | 42.13 | 42.79 | | 43.45 | 44.11 | 44.77 | 45.43 | 46.08 | | 24 | 33.80 | 34.36 | 34.91 | 35.47 | 36.02 | | 36.58 | 37.13 | 37.68 | 38.24 | 38.79 | | 25 | 27.45 | 27.90 | 28.35 | 28.80 | 29.25 | | 29.70 | 30.15 | 30.60 | 31.05 | 31.50 | | | | | | | | | | | | | | | 26 | 56.93 | 57.87 | 58.80 | 59.73 | 60.67 | | 61.60 | 62.53 | 63.47 | 64.40 | 65.33 | | 27 | 49.94 | 50.76 | 51.58 | 52.40 | 53.22 | | 54.04 | 54.86 | 55.68 | 56.49 | 57.31 | | 28 | 42.95 | 43.66 | 44.36 | 45.07 | 45.77 | | 46.48 | 47.18 | 47.88 | 48.59 | 49.29 | | 29 | 35.96 | 36.55 | 37.14 | 37.73 | 38.32 | | 38.91 | 39.50 | 40.09 | 40.68 | 41.27 | | 30 | 28.98 | 29.45 | 29.93 | 30.40 | 30.88 | | 31.35 | 31.83 | 32.30 | 32.78 | 33.25 | | | | | | | | | | | | | | | **31 (C) | 61.00 | 62.00 | 63.00 | 64.00 | 65.00 | | 66.00 | 67.00 | 68.00 | 69.00 | 70.00 **| | 32 | 53.38 | 54.25 | 55.13 | 56.00 | 56.88 | | 57.75 | 58.63 | 59.50 | 60.38 | 61.25 | | 33 | 45.75 | 46.50 | 47.25 | 48.00 | 48.75 | | 49.50 | 50.25 | 51.00 | 51.75 | 52.50 | | 34 | 38.13 | 38.75 | 39.38 | 40.00 | 40.63 | | 41.25 | 41.88 | 42.50 | 43.13 | 43.75 | | 35 (D) | 30.50 | 31.00 | 31.50 | 32.00 | 32.50 | | 33.00 | 33.50 | 34.00 | 34.50 | 35.00 |
Flux Breakup Tables continued…
| Glaze No. | 71% | 72% | 73% | 74% | 75% | | 76% | 77% | 78% | | 79% | 80% | | 1 (A) | 42.60 | 43.20 | 43.80 | 44.40 | 45.00 | | 45.60 | 46.20 | 46.80 | 47.40 | 48.00 | | 2 | 38.16 | 38.70 | 39.24 | 39.78 | 40.31 | | 40.85 | 41.39 | 41.93 | 42.46 | 43.00 | | 3 | 33.73 | 34.20 | 34.68 | 35.15 | 35.63 | | 36.10 | 36.58 | 37.05 | 37.53 | 38.00 | | 4 | 29.29 | 29.70 | 30.11 | 30.53 | 30.94 | | 31.35 | 31.76 | 32.18 | 32.59 | 33.00 | | 5 (B) | 24.85 | 25.20 | 25.55 | 25.90 | 26.25 | | 26.60 | 26.95 | 27.30 | 27.65 | 28.00 | | | | | | | | | | | | | | | 6 | 47.33 | 48.00 | 48.67 | 49.33 | 50.00 | | 50.67 | 51.33 | 52.00 | 52.67 | 53.33 | | 7 | 42.16 | 42.75 | 43.34 | 43.94 | 44.53 | | 45.13 | 45.72 | 46.31 | 46.91 | 47.50 | | 8 | 36.98 | 37.50 | 38.02 | 38.54 | 39.06 | | 39.58 | 40.10 | 40.63 | 41.15 | 41.67 | | 9 | 31.80 | 32.25 | 32.70 | 33.15 | 33.59 | | 34.04 | 34.49 | 34.94 | 35.39 | 35.83 | | 10 | 26.63 | 27.00 | 27.38 | 27.75 | 28.13 | | 28.50 | 28.88 | 29.25 | 29.63 | 30.00 | | | | | | | | | | | | | | | 11 | 52.07 | 52.80 | 53.53 | 54.27 | 55.00 | | 55.73 | 56.47 | 57.20 | 57.93 | 58.67 | | 12 | 46.15 | 46.80 | 47.45 | 48.10 | 48.75 | | 49.40 | 50.05 | 50.70 | 51.35 | 52.00 | | 13 | 40.23 | 40.80 | 41.37 | 41.93 | 42.50 | | 43.07 | 43.63 | 44.20 | 44.77 | 45.33 | | 14 | 34.32 | 34.80 | 35.28 | 35.77 | 36.25 | | 36.73 | 37.22 | 37.70 | 38.18 | 38.67 | | 15 | 28.40 | 28.80 | 29.20 | 29.60 | 30.00 | | 30.40 | 30.80 | 31.20 | 31.60 | 32.00 | | | | | | | | | | | | | | | 16 | 56.80 | 57.60 | 58.40 | 59.20 | 60.00 | | 60.80 | 61.60 | 62.40 | 63.20 | 64.00 | | 17 | 50.14 | 50.85 | 51.56 | 52.26 | 52.97 | | 53.68 | 54.38 | 55.09 | 55.79 | 56.50 | | 18 | 43.49 | 44.10 | 44.71 | 45.33 | 45.94 | | 46.55 | 47.16 | 47.78 | 48.39 | 49.00 | | 19 | 36.83 | 37.35 | 37.87 | 38.39 | 38.91 | | 39.43 | 39.94 | 40.46 | 40.98 | 41.50 | | 20 | 30.18 | 30.60 | 31.03 | 31.45 | 31.88 | | 32.30 | 32.73 | 33.15 | 33.58 | 34.00 | | | | | | | | | | | | | | | 21 | 61.53 | 62.40 | 63.27 | 64.13 | 65.00 | | 65.87 | 66.73 | 67.60 | 68.47 | 69.33 | | 22 | 54.14 | 54.90 | 55.66 | 56.43 | 57.19 | | 57.95 | 58.71 | 59.48 | 60.24 | 61.00 | | 23 | 46.74 | 47.40 | 48.06 | 48.72 | 49.38 | | 50.03 | 50.69 | 51.35 | 52.01 | 52.67 | | 24 | 39.35 | 39.90 | 40.45 | 41.01 | 41.56 | | 42.12 | 42.67 | 43.23 | 43.78 | 44.33 | | 25 | 31.95 | 32.40 | 32.85 | 33.30 | 33.75 | | 34.20 | 34.65 | 35.10 | 35.55 | 36.00 | | | | | | | | | | | | | | | 26 | 66.27 | 67.20 | 68.13 | 69.07 | 70.00 | | 70.93 | 71.87 | 72.80 | 73.73 | 74.67 | | 27 | 58.13 | 58.95 | 59.77 | 60.59 | 61.41 | | 62.23 | 63.04 | 63.86 | 64.68 | 65.50 | | 28 | 50.00 | 50.70 | 51.40 | 52.11 | 52.81 | | 53.52 | 54.22 | 54.93 | 55.63 | 56.33 | | 29 | 41.86 | 42.45 | 43.04 | 43.63 | 44.22 | | 44.81 | 45.40 | 45.99 | 46.58 | 47.17 | | 30 | 33.73 | 34.20 | 34.68 | 35.15 | 35.63 | | 36.10 | 36.58 | 37.05 | 37.53 | 38.00 | | | | | | | | | | | | | | | **31 (C) | 71.00 | 72.00 | 73.00 | 74.00 | 75.00 | | 76.00 | 77.00 | 78.00 | 79.00 | 80.00 **| | 32 | 62.13 | 63.00 | 63.88 | 64.75 | 65.63 | | 66.50 | 67.38 | 68.25 | 69.13 | 70.00 | | 33 | 53.25 | 54.00 | 54.75 | 55.50 | 56.25 | | 57.00 | 57.75 | 58.50 | 59.25 | 60.00 | | 34 | 44.38 | 45.00 | 45.63 | 46.25 | 46.88 | | 47.50 | 48.13 | 48.75 | 49.38 | 50.00 | | 35 (D) | 35.50 | 36.00 | 36.50 | 37.00 | 37.50 | | 38.00 | 38.50 | 39.00 | 39.50 | 40.00 |
Flux Breakup Tables continued…
| Glaze No. | 81% | 82% | 83% | 84% | 85% | | 86% | 87% | 88% | | 89% | 90% | | 1 (A) | 48.60 | 49.20 | 49.80 | 50.40 | 51.00 | | 51.60 | 52.20 | 52.80 | 53.40 | 54.00 | | 2 | 43.54 | 44.08 | 44.61 | 45.15 | 45.69 | | 46.23 | 46.76 | 47.30 | 47.84 | 48.38 | | 3 | 38.48 | 38.95 | 39.43 | 39.90 | 40.38 | | 40.85 | 41.33 | 41.80 | 42.28 | 42.75 | | 4 | 33.41 | 33.83 | 34.24 | 34.65 | 35.06 | | 35.48 | 35.89 | 36.30 | 36.71 | 37.13 | | 5 (B) | 28.35 | 28.70 | 29.05 | 29.40 | 29.75 | | 30.10 | 30.45 | 30.80 | 31.15 | 31.50 | | | | | | | | | | | | | | | 6 | 54.00 | 54.67 | 55.33 | 56.00 | 56.67 | | 57.33 | 58.00 | 58.67 | 59.33 | 60.00 | | 7 | 48.09 | 48.69 | 49.28 | 49.88 | 50.47 | | 51.06 | 51.66 | 52.25 | 52.84 | 53.44 | | 8 | 42.19 | 42.71 | 43.23 | 43.75 | 44.27 | | 44.79 | 45.31 | 45.83 | 46.35 | 46.88 | | 9 | 36.28 | 36.73 | 37.18 | 37.63 | 38.07 | | 38.52 | 38.97 | 39.42 | 39.86 | 40.31 | | 10 | 30.38 | 30.75 | 31.13 | 31.50 | 31.88 | | 32.25 | 32.63 | 33.00 | 33.38 | 33.75 | | | | | | | | | | | | | | | 11 | 59.40 | 60.13 | 60.87 | 61.60 | 62.33 | | 63.07 | 63.80 | 64.53 | 65.27 | 66.00 | | 12 | 52.65 | 53.30 | 53.95 | 54.60 | 55.25 | | 55.90 | 56.55 | 57.20 | 57.85 | 58.50 | | 13 | 45.90 | 46.47 | 47.03 | 47.60 | 48.17 | | 48.73 | 49.30 | 49.87 | 50.43 | 51.00 | | 14 | 39.15 | 39.63 | 40.12 | 40.60 | 41.08 | | 41.57 | 42.05 | 42.53 | 43.02 | 43.50 | | 15 | 32.40 | 32.80 | 33.20 | 33.60 | 34.00 | | 34.40 | 34.80 | 35.20 | 35.60 | 36.00 | | | | | | | | | | | | | | | 16 | 64.80 | 65.60 | 66.40 | 67.20 | 68.00 | | 68.80 | 69.60 | 70.40 | 71.20 | 72.00 | | 17 | 57.21 | 57.91 | 58.62 | 59.33 | 60.03 | | 60.74 | 61.44 | 62.15 | 62.86 | 63.56 | | 18 | 49.61 | 50.23 | 50.84 | 51.45 | 52.06 | | 52.68 | 53.29 | 53.90 | 54.51 | 55.13 | | 19 | 42.02 | 42.54 | 43.06 | 43.58 | 44.09 | | 44.61 | 45.13 | 45.65 | 46.17 | 46.69 | | 20 | 34.43 | 34.85 | 35.28 | 35.70 | 36.13 | | 36.55 | 36.98 | 37.40 | 37.83 | 38.25 | | | | | | | | | | | | | | | 21 | 70.20 | 71.07 | 71.93 | 72.80 | 73.67 | | 74.53 | 75.40 | 76.27 | 77.13 | 78.00 | | 22 | 61.76 | 62.53 | 63.29 | 64.05 | 64.81 | | 65.58 | 66.34 | 67.10 | 67.86 | 68.63 | | 23 | 53.33 | 53.98 | 54.64 | 55.30 | 55.96 | | 56.62 | 57.28 | 57.93 | 58.59 | 59.25 | | 24 | 44.89 | 45.44 | 46.00 | 46.55 | 47.10 | | 47.66 | 48.21 | 48.77 | 49.32 | 49.88 | | 25 | 36.45 | 36.90 | 37.35 | 37.80 | 38.25 | | 38.70 | 39.15 | 39.60 | 40.05 | 40.50 | | | | | | | | | | | | | | | 26 | 75.60 | 76.53 | 77.47 | 78.40 | 79.33 | | 80.27 | 81.20 | 82.13 | 83.07 | 84.00 | | 27 | 66.32 | 67.14 | 67.96 | 68.78 | 69.59 | | 70.41 | 71.23 | 72.05 | 72.87 | 73.69 | | 28 | 57.04 | 57.74 | 58.45 | 59.15 | 59.85 | | 60.56 | 61.26 | 61.97 | 62.67 | 63.38 | | 29 | 47.76 | 48.35 | 48.94 | 49.53 | 50.11 | | 50.70 | 51.29 | 51.88 | 52.47 | 53.06 | | 30 | 38.48 | 38.95 | 39.43 | 39.90 | 40.38 | | 40.85 | 41.33 | 41.80 | 42.28 | 42.75 | | | | | | | | | | | | | | | **31 (C) | 81.00 | 82.00 | 83.00 | 84.00 | 85.00 | | 86.00 | 87.00 | 88.00 | 89.00 | 90.00 **| | 32 | 70.88 | 71.75 | 72.63 | 73.50 | 74.38 | | 75.25 | 76.13 | 77.00 | 77.88 | 78.75 | | 33 | 60.75 | 61.50 | 62.25 | 63.00 | 63.75 | | 64.50 | 65.25 | 66.00 | 66.75 | 67.50 | | 34 | 50.63 | 51.25 | 51.88 | 52.50 | 53.13 | | 53.75 | 54.38 | 55.00 | 55.63 | 56.25 | | 35 (D) | 40.50 | 41.00 | 41.50 | 42.00 | 42.50 | | 43.00 | 43.50 | 44.00 | 44.50 | 45.00 |
Flux Breakup Tables continued…
| Glaze No. | 91% | 92% | 93% | 94% | 95% | | 96% | 97% | 98% | | 99% | 100% | | 1 (A) | 54.60 | 55.20 | 55.80 | 56.40 | 57.00 | | 57.60 | 58.20 | 58.80 | 59.40 | 60.00 | | 2 | 48.91 | 49.45 | 49.99 | 50.53 | 51.06 | | 51.60 | 52.14 | 52.68 | 53.21 | 53.75 | | 3 | 43.23 | 43.70 | 44.18 | 44.65 | 45.13 | | 45.60 | 46.08 | 46.55 | 47.03 | 47.50 | | 4 | 37.54 | 37.95 | 38.36 | 38.78 | 39.19 | | 39.60 | 40.01 | 40.43 | 40.84 | 41.25 | | 5 (B) | 31.85 | 32.20 | 32.55 | 32.90 | 33.25 | | 33.60 | 33.95 | 34.30 | 34.65 | 35.00 | | | | | | | | | | | | | | | 6 | 60.67 | 61.33 | 62.00 | 62.67 | 63.33 | | 64.00 | 64.67 | 65.33 | 66.00 | 66.67 | | 7 | 54.03 | 54.63 | 55.22 | 55.81 | 56.41 | | 57.00 | 57.59 | 58.19 | 58.78 | 59.38 | | 8 | 47.40 | 47.92 | 48.44 | 48.96 | 49.48 | | 50.00 | 50.52 | 51.04 | 51.56 | 52.08 | | 9 | 40.76 | 41.21 | 41.66 | 42.10 | 42.55 | | 43.00 | 43.45 | 43.90 | 44.34 | 44.79 | | 10 | 34.13 | 34.50 | 34.88 | 35.25 | 35.63 | | 36.00 | 36.38 | 36.75 | 37.13 | 37.50 | | | | | | | | | | | | | | | 11 | 66.73 | 67.47 | 68.20 | 68.93 | 69.67 | | 70.40 | 71.13 | 71.87 | 72.60 | 73.33 | | 12 | 59.15 | 59.80 | 60.45 | 61.10 | 61.75 | | 62.40 | 63.05 | 63.70 | 64.35 | 65.00 | | 13 | 51.57 | 52.13 | 52.70 | 53.27 | 53.83 | | 54.40 | 54.97 | 55.53 | 56.10 | 56.67 | | 14 | 43.98 | 44.47 | 44.95 | 45.43 | 45.92 | | 46.40 | 46.88 | 47.37 | 47.85 | 48.33 | | 15 | 36.40 | 36.80 | 37.20 | 37.60 | 38.00 | | 38.40 | 38.80 | 39.20 | 39.60 | 40.00 | | | | | | | | | | | | | | | 16 | 72.80 | 73.60 | 74.40 | 75.20 | 76.00 | | 76.80 | 77.60 | 78.40 | 79.20 | 80.00 | | 17 | 64.27 | 64.98 | 65.68 | 66.39 | 67.09 | | 67.80 | 68.51 | 69.21 | 69.92 | 70.63 | | 18 | 55.74 | 56.35 | 56.96 | 57.58 | 58.19 | | 58.80 | 59.41 | 60.03 | 60.64 | 61.25 | | 19 | 47.21 | 47.73 | 48.24 | 48.76 | 49.28 | | 49.80 | 50.32 | 50.84 | 51.36 | 51.88 | | 20 | 38.68 | 39.10 | 39.53 | 39.95 | 40.38 | | 40.80 | 41.23 | 41.65 | 42.08 | 42.50 | | | | | | | | | | | | | | | 21 | 78.87 | 79.73 | 80.60 | 81.47 | 82.33 | | 83.20 | 84.07 | 84.93 | 85.80 | 86.67 | | 22 | 69.39 | 70.15 | 70.91 | 71.68 | 72.44 | | 73.20 | 73.96 | 74.73 | 75.49 | 76.25 | | 23 | 59.91 | 60.57 | 61.23 | 61.88 | 62.54 | | 63.20 | 63.86 | 64.52 | 65.18 | 65.83 | | 24 | 50.43 | 50.98 | 51.54 | 52.09 | 52.65 | | 53.20 | 53.75 | 54.31 | 54.86 | 55.42 | | 25 | 40.95 | 41.40 | 41.85 | 42.30 | 42.75 | | 43.20 | 43.65 | 44.10 | 44.55 | 45.00 | | | | | | | | | | | | | | | 26 | 84.93 | 85.87 | 86.80 | 87.73 | 88.67 | | 89.60 | 90.53 | 91.47 | 92.40 | 93.33 | | 27 | 74.51 | 75.33 | 76.14 | 76.96 | 77.78 | | 78.60 | 79.42 | 80.24 | 81.06 | 81.88 | | 28 | 64.08 | 64.78 | 65.49 | 66.19 | 66.90 | | 67.60 | 68.30 | 69.01 | 69.71 | 70.42 | | 29 | 53.65 | 54.24 | 54.83 | 55.42 | 56.01 | | 56.60 | 57.19 | 57.78 | 58.37 | 58.96 | | 30 | 43.23 | 43.70 | 44.18 | 44.65 | 45.13 | | 45.60 | 46.08 | 46.55 | 47.03 | 47.50 | | | | | | | | | | | | | | | **31 (C) | 91.00 | 92.00 | 93.00 | 94.00 | 95.00 | | 96.00 | 97.00 | 98.00 | 99.00 | 100.00 **| | 32 | 79.63 | 80.50 | 81.38 | 82.25 | 83.13 | | 84.00 | 84.88 | 85.75 | 86.63 | 87.50 | | 33 | 68.25 | 69.00 | 69.75 | 70.50 | 71.25 | | 72.00 | 72.75 | 73.50 | 74.25 | 75.00 | | 34 | 56.88 | 57.50 | 58.13 | 58.75 | 59.38 | | 60.00 | 60.63 | 61.25 | 61.88 | 62.50 | | 35 (D) | 45.50 | 46.00 | 46.50 | 47.00 | 47.50 | | 48.00 | 48.50 | 49.00 | 49.50 | 50.00 |